Did you know that a natural indigo called “Ryukyu ai” is grown in the tropical island of Okinawa? Ryukyu ai is cultivated in the “Oshittai,” a dense forest spreading over Motobu-cho and Nago City’s Genka, where a deep green forest called Yanbaru stretches. There is a dyeing and weaving studio in Motobu-cho that expresses the charm of Okinawan blue by dyeing threads with Ryukyu ai and using the traditional kasuri (patterned fabric) technique.
What is the new “Ryukyu Bigasuri” brand that leverages tradition to create a new appeal?
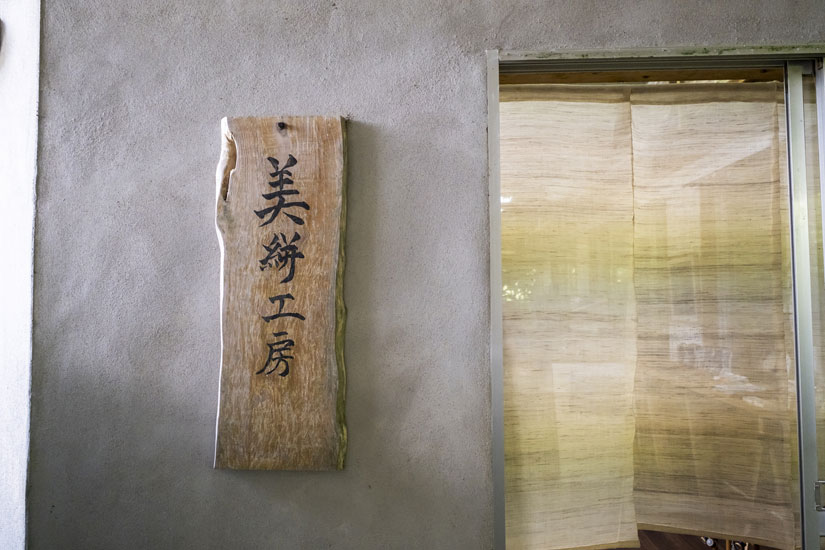
There is a craftsman who combines tradition and innovation using Ryukyu ai. This is Mr. Okikazu Maeshiro, a dyeing and weaving artisan with a studio in Motobu-cho, Okinawa Prefecture. As the third generation of the “Bigasuri Workshop,” he maximizes the historical appeal of Ryukyu ai and breathes new life into the world of dyeing and weaving with his new designs and techniques.
While running the workshop, he has also established his own brand, “Okinawa Blues Shop,” and is expanding the appeal of Ryukyu ai to many people through the sale of indigo-dyed accessories and indigo-dyeing experiences.
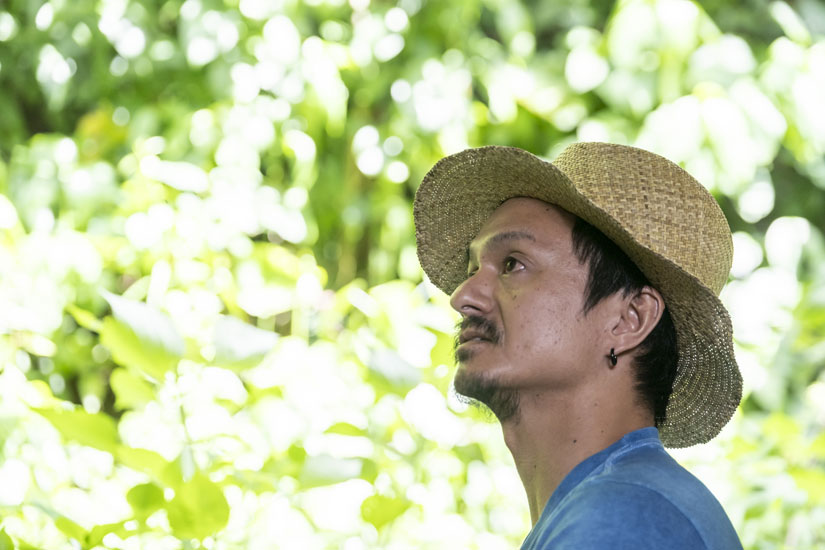
Ryukyu Bigasuri” produced by Bigasuri Studio was started by his grandfather, Kosei Maeshiro. It is a type of dyed fabric that combines the best of Ryukyu ai-dyeing and traditional kasuri techniques with the essence of something new.
Okinawan kasuri developed in the Ryukyu Kingdom between the 15th and 16th centuries. It is believed that this technique was born from a fusion of techniques and cultures brought through trade with Southeast Asia, China, India, and other countries. It is a weaving technique that requires a high level of skill to create complex patterns by meticulously dyeing different threads. The unique, hazy pattern is created by shifting the dyed threads as they are woven. The name “kasuri” comes from the fact that the pattern looks hazy.
The patterns of kasuri are based on motifs of Okinawan nature, scenery, flora and fauna, and are characterized by their vivid colors and detailed patterns. In addition to indigo, they also dye their fabrics using natural materials from the region. By combining the traditional Ryukyu kasuri technique with modern design, he breathes new life into the old. His works have attracted attention not only locally but also from outside the prefecture and abroad because of their beauty and high quality.
Dark and deep, the charm of Ryukyu ai
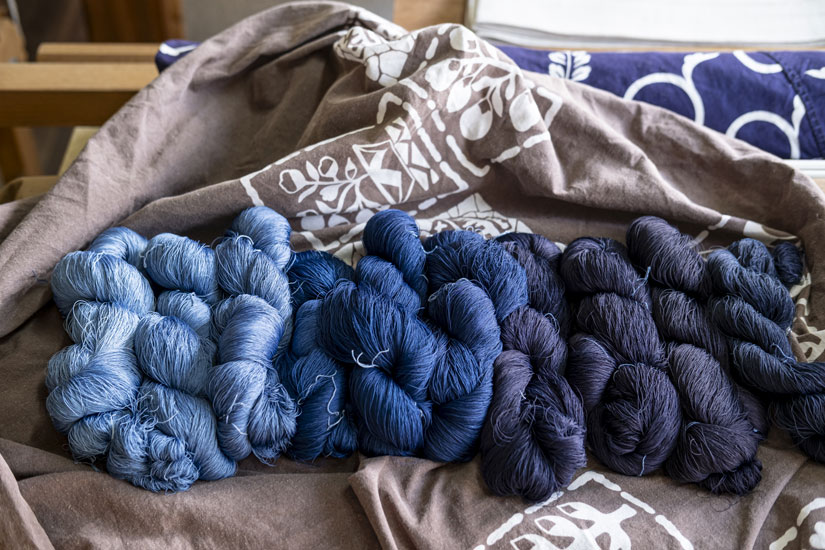
Ryukyu ai is made from “Ryukyu ai,” which is found in the subtropical region called the foxglove family, and differs in type and the process used to make the dye from “tade-ai,” a plant of the tade family found in Tokushima, the familiar indigo production area in Japan. In Honshu and Shikoku, indigo leaves are dried and fermented to make a dye called sukumo, while in Okinawa, cultivated Ryukyu ai leaves are placed in a large pit called a kama, naturally fermented, mixed with lime, and then fermented with water, awamori and lye in a mud-like substance (commonly called mud indigo) that has collected at the bottom. The charm of Ryukyu ai is that it is a natural fermented dye. The charm of Ryukyu indigo is its unique deep blue color. Mr. Maeshiro is passionate about “mastering the deep blue of indigo as he dyes more and more,” and he brings the beauty of this color to life in his work. His works are characterized by the gradation of Ryukyu ai that spreads over many layers. He dyes the yarn in a variety of shades to maximize the natural, deep hues of Ryukyu ai and captivate the viewer.
To achieve this, he conducted repeated research on making a dye called “Doro-ai,” using Ryukyu ai purchased from a local farmer. In the process of trial and error, he also makes full use of his own unique techniques. Mr. Maeshiro is particularly particular about the process of fermenting indigo leaves and processing them into mud indigo. He places great importance on the indigo dyeing process to produce unique shades of color.
Fusion of original design and traditional Ryukyu Kasuri technique
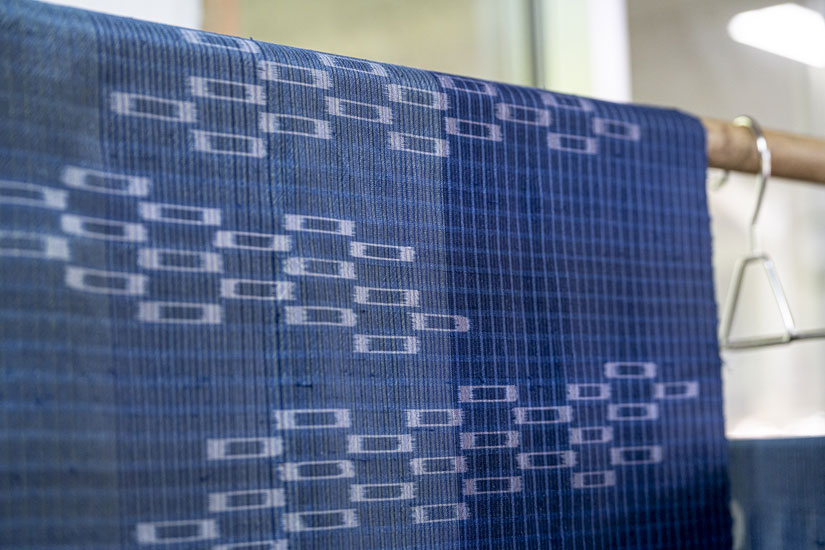
Mr. Maeshiro’s work is a perfect blend of his own originality expressed while faithfully adhering to the traditional kasuri (kasuri) technique handed down from generation to generation in the Ryukyu Islands.
His designs are simple yet sophisticated, featuring patterns inspired by Ryukyuan nature and culture. After graduating from high school, he went to college in Chiba Prefecture, and through surfing, which was his forte, he became fascinated by the rugged Kujukuri Sea, which was completely different from the scenery he had seen on the island where he was born and raised.
The wave patterns in Kujukuri are very different from those in Okinawa, even though they are the same ocean,” says Maeshiro, ”and I found it very original and impactful. Maeshiro says, “The scenery and experiences I saw there made a big impact on me. The scenery and experiences he had there are reflected in the patterns of his kasuri, which is unique.
By incorporating modern elements, such as combining Ryukyu Bigasuri fabric with leather, he has managed to combine tradition and innovation, and is loved by a wide range of people.
Dyeing and weaving that is uniquely you, groping in the face of difficulties
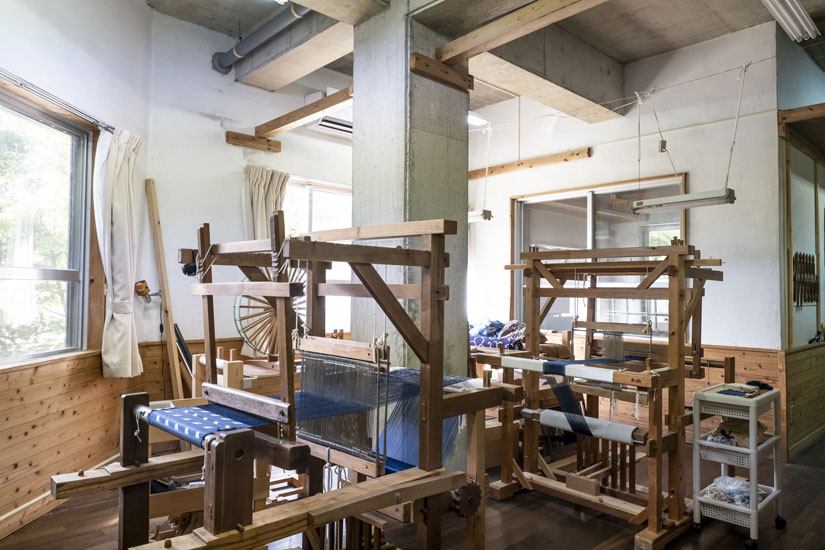
Maeshiro’s path to making things has not been a smooth one; in 2013, he suffered from a spinal cord disease that forced him to live in a wheelchair, and he had to take a break from weaving for a while. The loom that Mr. Maeshiro uses is called a “takabata” loom, a style of weaving that requires the weaver to step on the loom with both feet alternately, which makes weaving impossible with a wheelchair. However, even after living like this, he still wanted to continue the family business and weave.
While he was stuck in the long tunnel of wanting to take over the family business, he suddenly had a turning point. A woodworker with whom he had a connection was so impressed by Maeshiro’s passion that he proposed to support her so that she could continue dyeing and weaving.
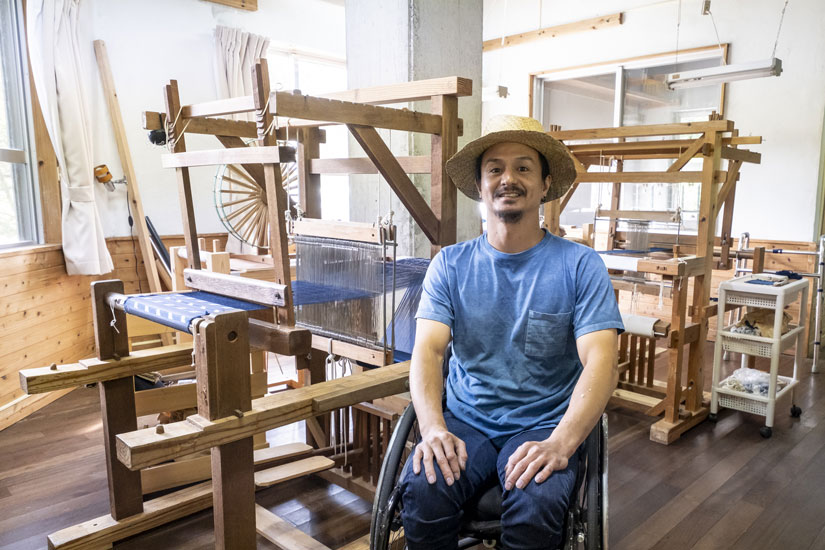
This led to the creation of an original loom tailored to his physical condition. It was designed so that Maeshiro, who rides in a wheelchair, can continue weaving under his own power.
It takes more time than other people, but that is why I continue to weave every day with an expression that only I can do,” he says. I still want to weave kimono fabric. She says with a dazzling smile and full of joy.
Manufacturing that stays with the times for the next generation
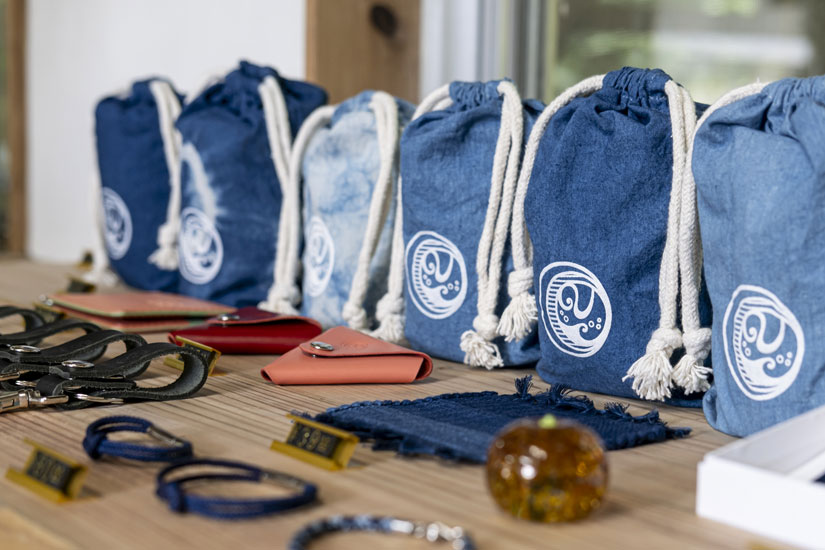
The concept of the craftsmanship that Mr. Maeshiro aims for is one that will be close to the next generation. As lifestyles change from Japanese to Western, the dyeing and weaving industry, which is dominated by the kimono industry, is going through a slowdown nationwide. Despite her desire to weave kimonos, Ms. Maeshiro is able to do what she can in the dyeing and weaving industry, where it is difficult to survive simply by carrying on the tradition. What Maeshiro can do is to find new value in new generations and new places.
In order to pass on the tradition to the future, he holds workshops and lectures to convey the charm of Ryukyu Ai to the younger generation, and is active in passing on his techniques and knowledge.
In 2022, he will hold a solo exhibition “OKINAWA BLUES” in New York. He has been recognized internationally for his talent in introducing the appeal of Ryukyu ai and kasuri. His works are a beautiful fusion of Okinawan tradition and modern design, and have impressed many people with the “OKINAWA BLUE” that Ryukyu Ai attracts.
Mr. Maeshiro’s ambition is to use New York as an opportunity to visit other world cities to convey the charm of Ryukyu Bigasuri and Ryukyu Ai and Kasuri.
Overcoming obstacles, Mr. Maeshiro will continue to inspire many people as a dyeing artist who connects Ryukyu ai and the blue of the sea and pursues the scenery in his eyes with beautiful kasuri, and as the third generation of the Bigasuri workshop he inherited from his grandfather.