Okinawa is home to many pottery artists of various tastes, including “Yachimun. Masayuki Miyagi, who was born and raised in Okinawa, opened his own kiln 11 years ago after training in traditional Okinawan yachimun making. What kind of pottery does Mr. Miyagi create and aim for every day?
While working as an office worker, I began to think vaguely that I wanted to make things.
Masayuki Miyagi of Miyagi Pottery has a workshop in a peaceful location surrounded by sugar cane fields in Nanjo City in the southern part of Okinawa’s main island, about 40 minutes by car from Naha.
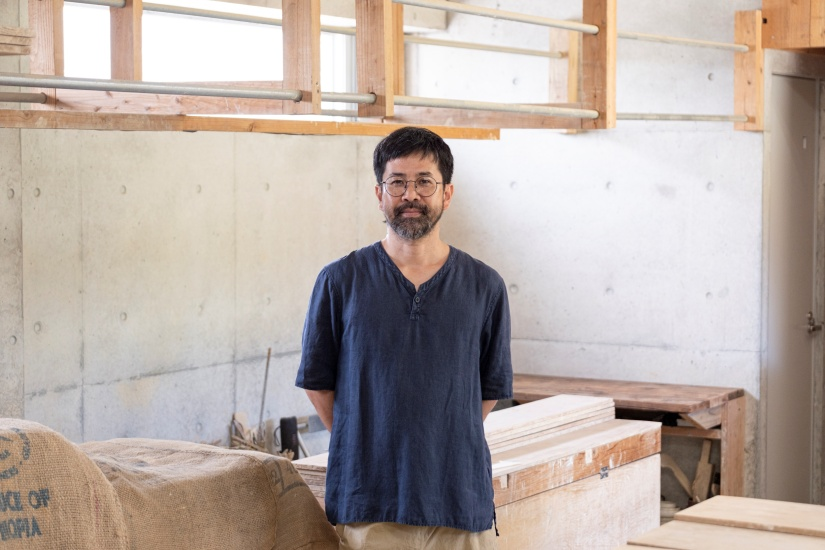
Mr. Miyagi’s pottery has a simple yet dignified presence. Miyagi’s works are popular both inside and outside of the prefecture, and he holds solo exhibitions in central Tokyo several times a year, and his studio’s open days, which are held a few days a month, always attract many reservations.
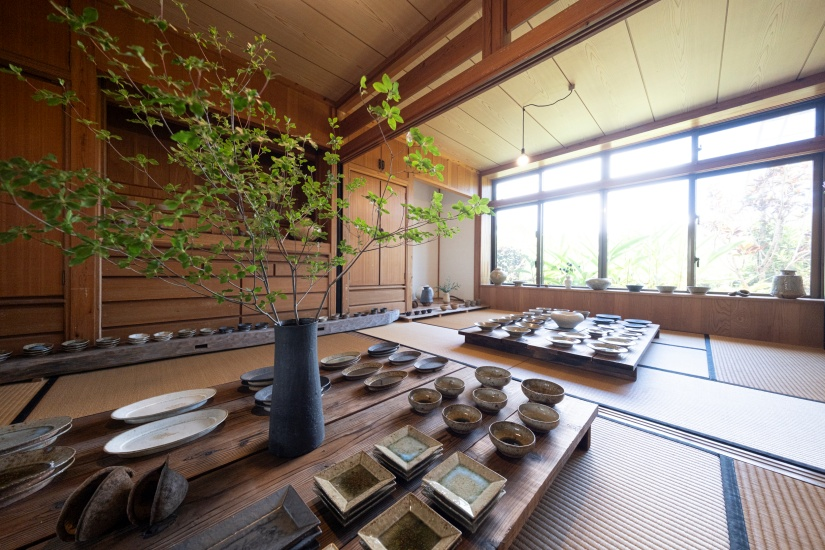
This gallery makes use of the atmosphere of an old Okinawan house as it is. If you look closely, you will see a Buddhist altar. This is a room for entertaining guests, called ichiban-za and niban-za in Okinawa. This old house is the family home of Aki’s wife. They were classmates in junior high school. Mr. Miyagi was born and raised just around the corner.
Pottery made from clay was something that clicked with me.
About 20 years ago, while working at a company as an office worker, Mr. Miyagi began to vaguely think that he wanted to make things. He felt that he was familiar with many traditional crafts in Okinawa, such as dyed fabrics, dyed patterned textiles, pottery, lacquerware, and sanshin (a three-stringed musical instrument), and that he was rather familiar with making things for a living. Of these, he says that pottery made from clay was the most appealing to him.
The most famous type of Okinawan pottery is yachimun, which is thick and heavy, and has impressive colorful dyed patterns. Yachimun is the Okinawan word for pottery. Yachimun is a word meaning “pottery” in the Okinawan language, and there are two major yachimun production centers in the prefecture: Tsuboya in Naha City and Yomitan Village in the northern part of the prefecture. The history of Okinawan pottery is long, but the origin of today’s Okinawan yachimun is Tsuboya-yaki, which was created after the war when three kilns were integrated in Tsuboya to promote the pottery industry.
At the age of 25, Mr. Miyagi apprenticed himself to Iki Koji, a potter in the Tsuboya ware tradition, and spent 10 years learning yachimun production methods under Iki in Yomitan. He later became independent in 2013 and opened his own kiln at the current location.
I want to keep it as simple as possible. I want to make vessels that show off the food.
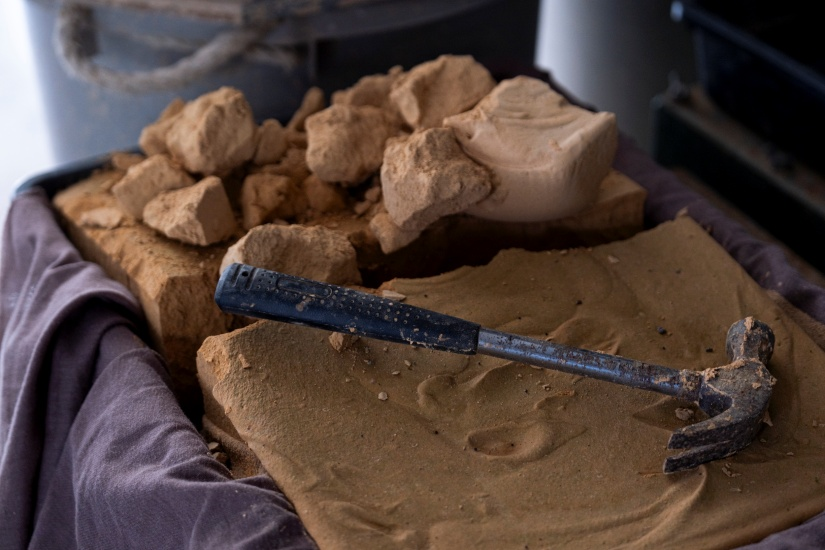
The soil of Okinawa is a clayey red clay unique to the Nansei Islands. Miyagi Pottery uses mainly clay from the northern part of the main island of Okinawa and blends several other types of clay, taking into consideration not only texture but also strength and stability. The red clay from the southern part of the main island is not suitable for glazing because of its low refractoriness. On the other hand, it is suitable for red tiles, which are unglazed at low temperatures and unique to Okinawa, and this area is a production center for red tiles.
Daring to retain the rough texture of natural materials
Every day, Mr. Miyagi wants to emphasize the texture of the soil itself, bringing out its own flavor. The feeling of iron powder in the raw clay, whitish small stones, and black sesame seeds. He makes the most of such textures of natural materials and leaves a rough presence in the bare earth.
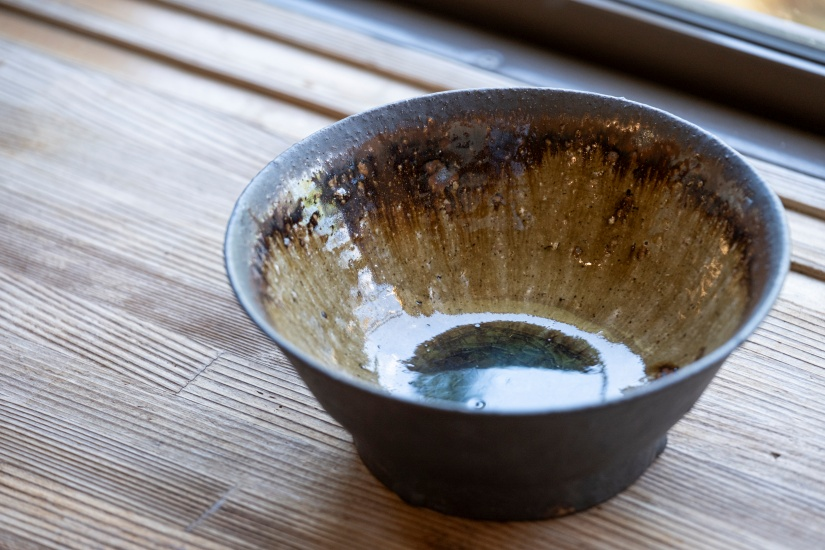
This bowl is called “makai” in the Okinawan language. It is a glaze called “ash glaze” with a beautiful deep green puddle on the bottom of the rough, coarse firing. The glaze is made from the ashes of oak and sawtooth oak from the kiln of a pizza parlor with which he has a close relationship, and mixed with the clay.
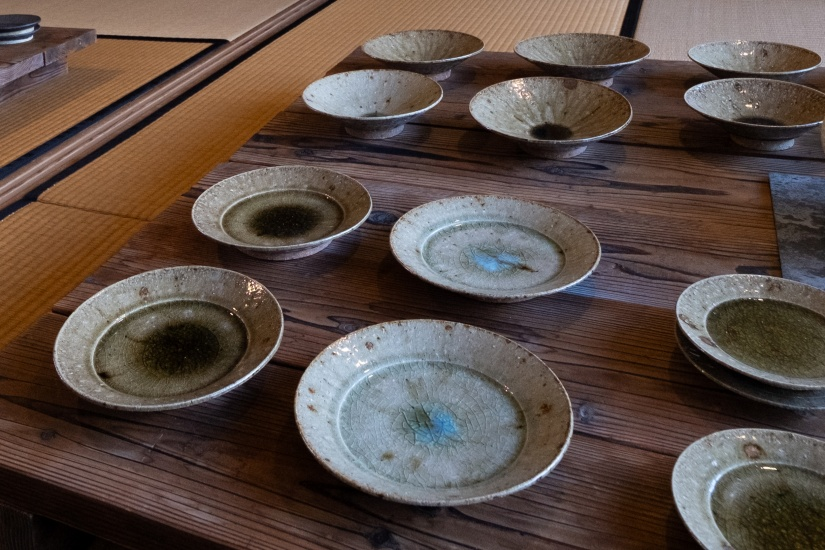
Miyagi himself often makes vessels with ash glaze because he likes the combination of roughness and shiny, glass-like texture.
The blending of clay, and the combinations of clay and glaze, are endless. He makes a hypothesis, makes subtle changes to the mixture, and fires it repeatedly, and when he has achieved the firing he likes, he actually puts it into the vessel. This difficulty, he says, is what makes pottery making so interesting.
Miyagi’s vessels have a different impression from the Okinawan style. When he first started out on his own, he used to dye his pieces a little more rounded and colorful, but as he pursued what he wanted to create day after day, he settled on the interesting appearance he has today.
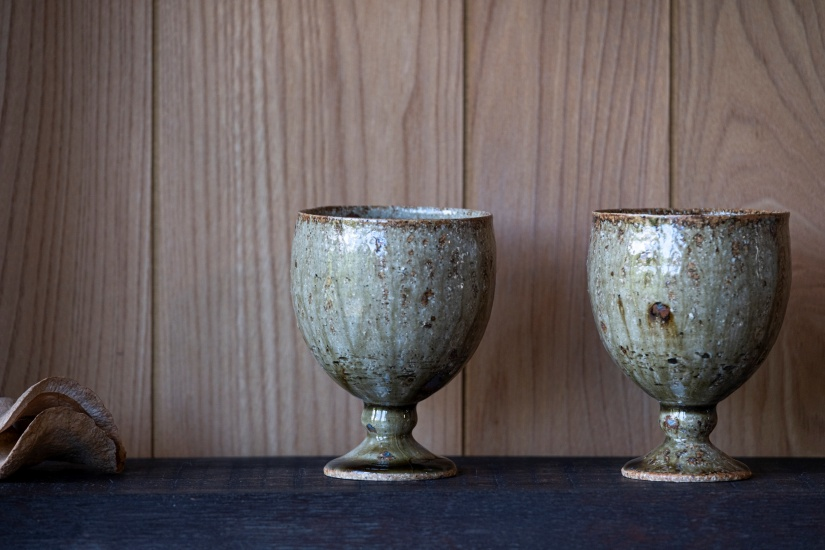
This goblet is one of the most popular pieces. The slightly burnt rim design is also a point of attention. We want people to take what they like in their hands, whether it is beer, wine, or coffee, and drink it as they like it, without deciding what to use it for.
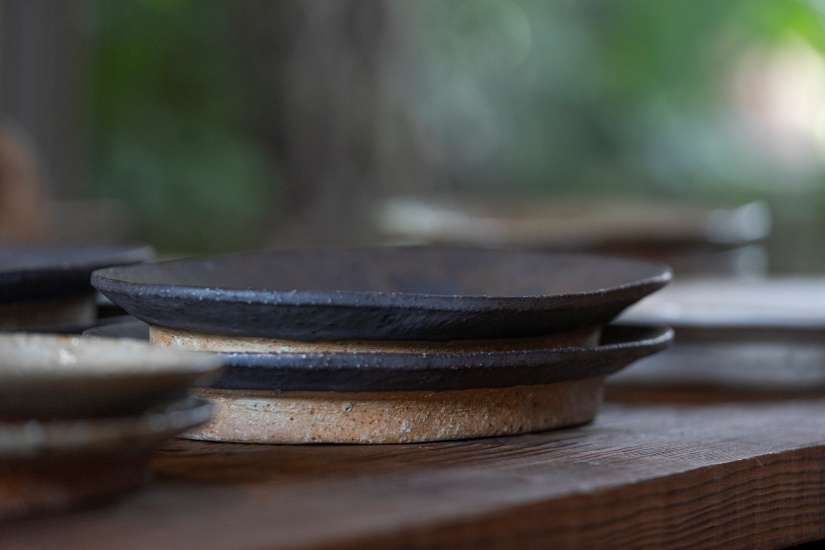
For daily-use pottery, the hand-held pieces should be light and gently comfortable in the hand, while the plates should be thicker to add stability. The most important consideration when creating the dishes is the usability for the people who actually use them at the table. Although Aki does all the cooking, she loves eating, drinking, and relaxing, so she considers the functionality of the plates and the way they look with food to be very important.
At Miyagi Pottery, Mr. Miyagi is in charge of the rokuro (potter’s wheel) and Aki and other staff members are in charge of the tatara, a technique that uses molds. In both Tsuboya and Yomitan, there has long been a division of labor, with the men of the family kneading and molding the dough, and the women painting. As was the case with his master, the Miyagi family has adopted this system, which can be said to be uniquely Okinawan.
It’s a tool, so it has to be used.
Recently, we can see on social networking sites how people who have purchased our products actually use them at home or in the store. This makes him more than happy. Mr. Miyagi says, “It’s a tool, so it has to be used.
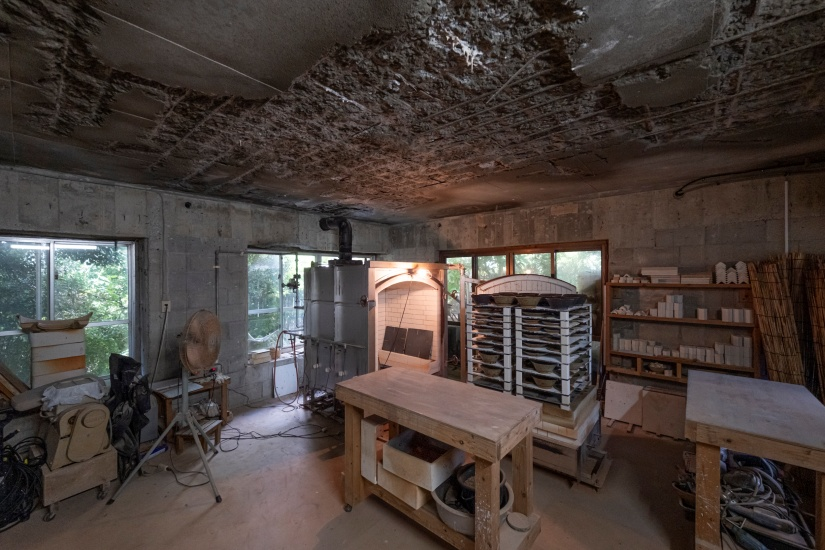
Mr. Miyagi has been firing in a gas kiln ever since he became independent. However, in the past few years, he has been particularly interested in firing in a wood-fired kiln, and recently he has been firing in a wood-fired kiln jointly with several fellow potters in the prefecture. Compared to gas kilns, wood-fired kilns are more difficult because they are less stable. However, he is attracted by the expression that cannot be produced by a machine, and his immediate goal is to have his own wood-fired kiln, saying, “I want to make things that are created by experiencing the flame in a more analog way.
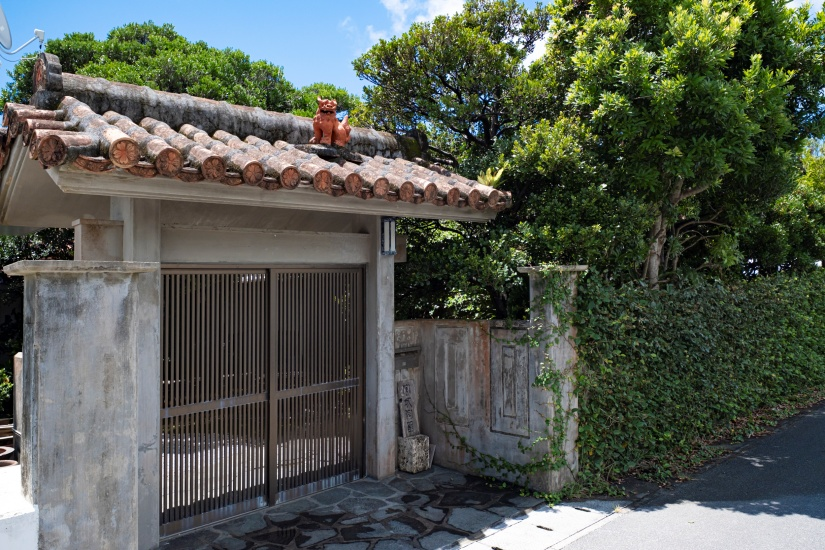
Both the vessel and the method of production are simpler. Thankfully, he cannot deny the feeling of being overwhelmed by the production process. However, instead of just doing the work, Miyagi says quietly, “I hope to make it more like a life’s work rather than a job. I chose pottery because I trusted my instincts, and that’s what I found. He will continue to study with an inquisitive mind and create tools that will be a part of people’s lives.