Tokoname City, Aichi Prefecture, one of the Six Old Kilns of Japan, has flourished as a pottery production area since the late Heian period. The city is characterised by its reddish-brown clay, which turns reddish-brown when fired, and a representative traditional craft is the kyusu (teapot). Gafu Ito, who was born and raised in Tokoname City, majoured in ceramics at high school and university and honed his skills as an apprentice under kyusu potter Fugetsu Murakoshi, who studied under living national treasure Tsuneyama Yamada III, is one of those rare people who make their own kyusu from the clay. We asked him about his passion for kyusu.
Tokoname ware with red clay.
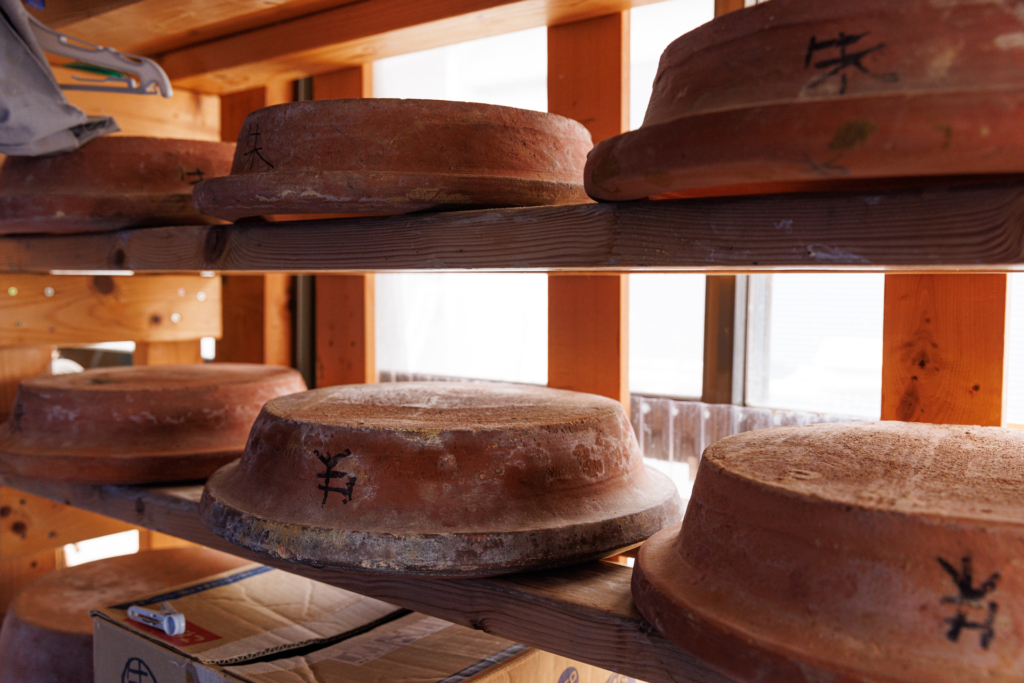
Tokoname ware is made mainly in Tokoname City, Aichi Prefecture, and is said to have started in the late Heian period. At that time, anagama kilns were built in Tokoname City and almost the entire hilly area of the Chita Peninsula, and the area developed into the largest pottery production area among the six oldest kilns in Japan. The clay from the Chita Peninsula is rich in iron, which gives it a vermilion colour when fired, and is known as shudei, which became a characteristic of Tokoname ware.
In the Heian period (794-1185), jars and pots were made, in the Kamakura period (1185-1333) tea bowls and vessels were made, and from the late Edo period (1603-1868) ceramic earthenware pipes and red clay teapots were produced. The spread of tea culture from around the middle of the Edo period also spurred the production of teapots in Tokoname. The development of vermilion mud became a focus, and the region became nationally known as a teapot production centre.
Teapots developed through a combination of pottery clay and technology.
Tokoname ware is still loved today because the iron content mellows out the bitterness and astringency of the tea, but one of the reasons for its development is that Tokoname’s vermilion mud is suitable for making kyusu. The fine texture of vermilion mud makes it strong enough not to wear out even when thinly finished, and its high iron content makes it suitable for kyusu in that it can be tightly baked. In addition, the more you use a kyusu made of vermillion mud, the more lustrous it becomes, and it is also called a “kyusu that grows”.
However, making kyusu requires a high level of skill. The body, lid, handle, spout and other parts of the kyusu are made individually and then combined at the end. Naturally, if the matching parts are not the right size and angle, the teapot will not be usable, and the balance of the appearance when the parts are combined also greatly affects the quality.
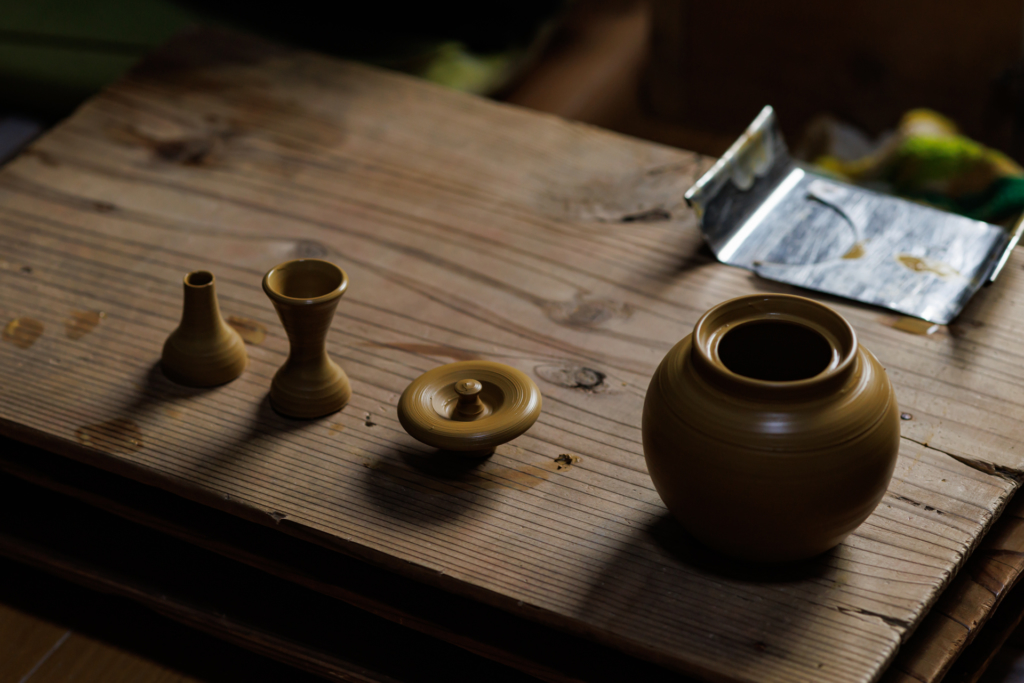
Unlike containers and teacups, which are used to put food on and drink into, kyusu teapots are used to brew tea, and ease of use is also an important point. It is not only a question of whether the parts fit together perfectly or whether the appearance is balanced, but also how difficult it is to make a kyusu that is also easy to use. It is said that the development of kyusu production in Tokoname ware is due in part to the fact that many highly skilled craftsmen grew up in the area.
Born and raised in Tokoname City, ceramics is close to home
In Tokoname City, there is a tourist attraction called the ‘Yakimono Walkway’. The popular spot called ‘Dokeizaka’ (earthen pipe slope), where earthen pipes from the Meiji era and shochu bottles from the early Showa era are on the walls and the slope is covered with waste wood used during the firing of earthen pipes, and the historic climbing kilns can also be seen.
Mr Ito was born and raised in such a pottery town. Although she had opportunities to experience pottery making as a child, she did not think at the time that she would pursue a career in ceramics in the future. When she decided to go on to high school, she asked herself if there was a good high school within cycling distance, and she decided on Aichi Prefectural Tokoname High School. There was a ceramics course in the industrial department, and he decided to enter the school with a light heart, thinking at the time that “pottery is fun and I would like to try it”. Gradually, however, he became completely absorbed in the fascination of pottery.
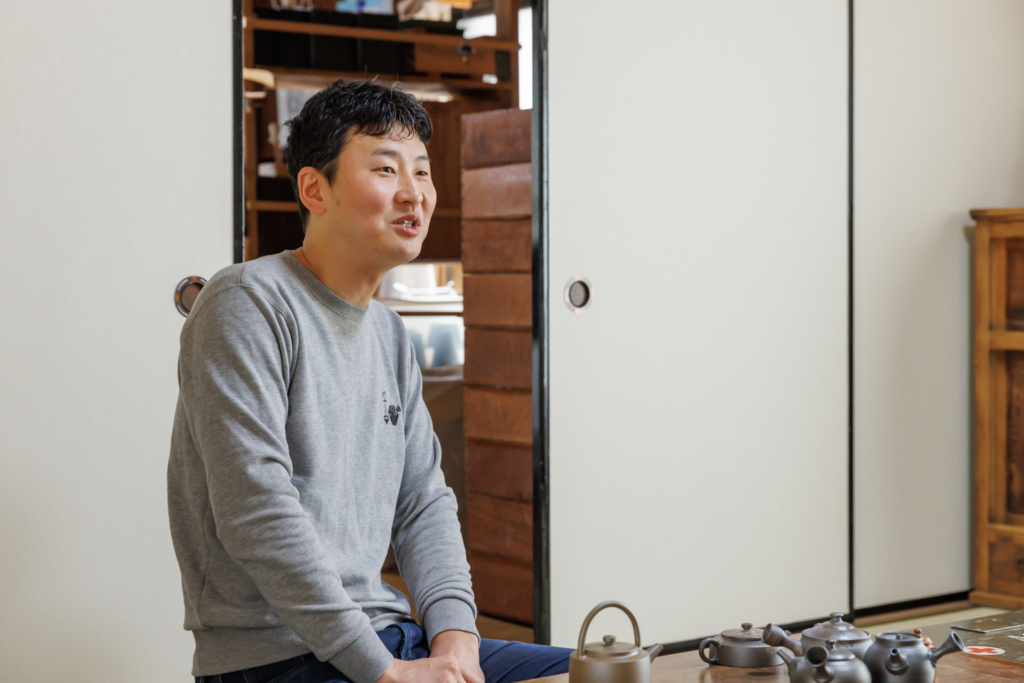
Mr Ito started making kyusu when he was a student. Until then, he had taken Tokoname ware kyusu for granted, but when he tried making one himself, he was surprised at the high level of skill involved and gave up on the idea that it was impossible for him. However, when he discovered the depth of kyusu, he suddenly became interested in kyusu making, saying that he could do anything if he mastered kyusu. He went on to study ceramics at university and became an apprentice under Murakoshi Fugetsu while still a student.
Old style Tokoname ware.
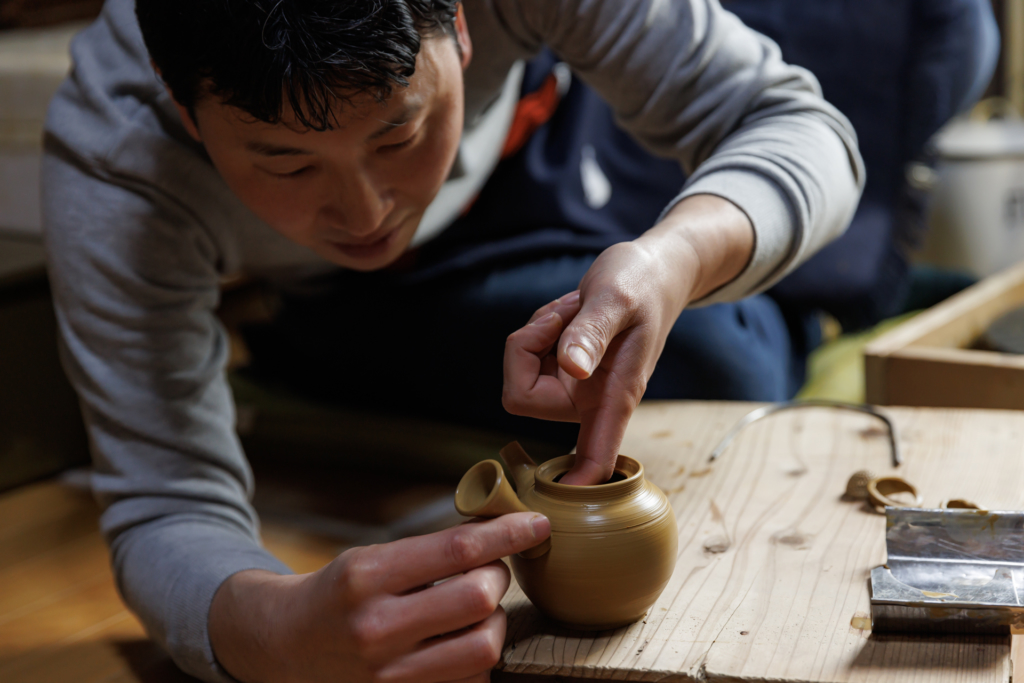
After graduating from university, he set up his own business and, as a kyusu maker, he worked diligently to hone his kyusu-making skills. There are many potters in Tokoname who make kyusu, but in Mr Ito’s eyes, many of them seemed to be trying to develop their own individuality. In this context, Mr Ito aimed to create a kyusu from the late Edo period, when the Shudo kyusu was born. The design is simple, but uncompromising in every detail. He wanted to master the old style of Tokoname ware in terms of the moulding, techniques and clay production method.
Soil preparation is a daily routine; three years in ceramic clay.
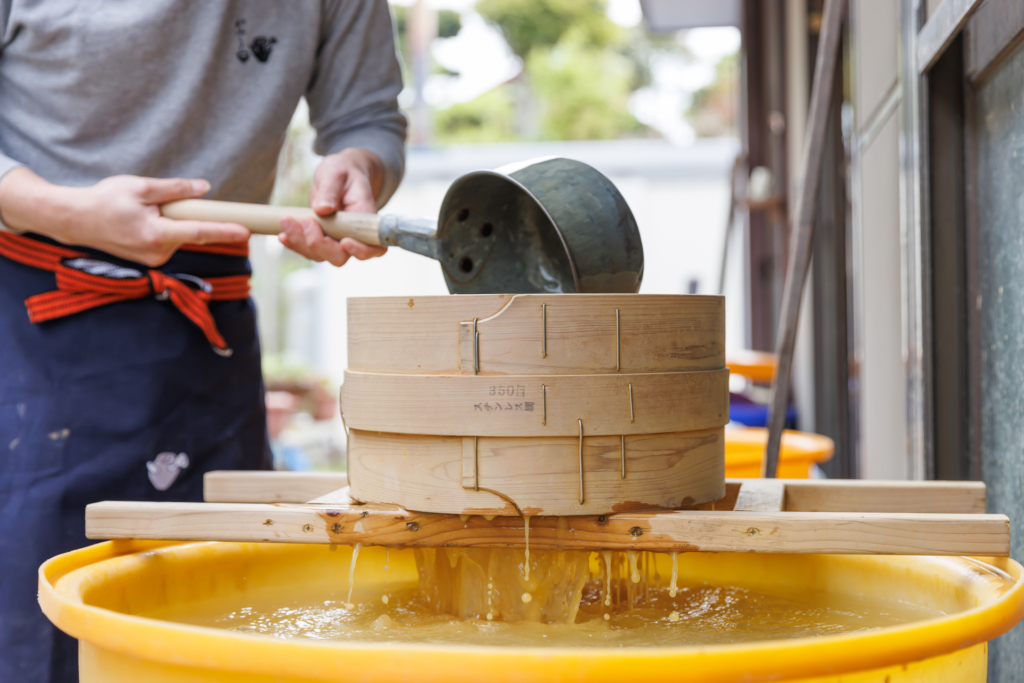
As well as mastering the art of kyusu making, Mr Ito also worked on clay making. Most Tokoname ware today uses a blend of vermilion mud to ensure a stable finish, but Mr Ito insists on using traditional natural vermilion mud, “honshu mud”, and uses a method called “suihi”, which was used in the late Edo period to make the clay. The clay directly influences the texture of the finished teapot, which is fired without glaze. By making the clay yourself, you can pursue the texture and colour to your own taste. Every day, the process starts with making the clay. The clay is stirred in a jar filled with water and the supernatant is filtered through a sieve. This process continues once a day for a year, taking 30-40 minutes per day. After one year, the clay is laid down to remove the water. At first, the teapots were used after a year’s sleep, but they cracked during the process of making them and the handles came off when they were assembled. Also, the surface could become scratched, so they tried and tested the period of laying down, and found that laying it down for at least three years worked well.
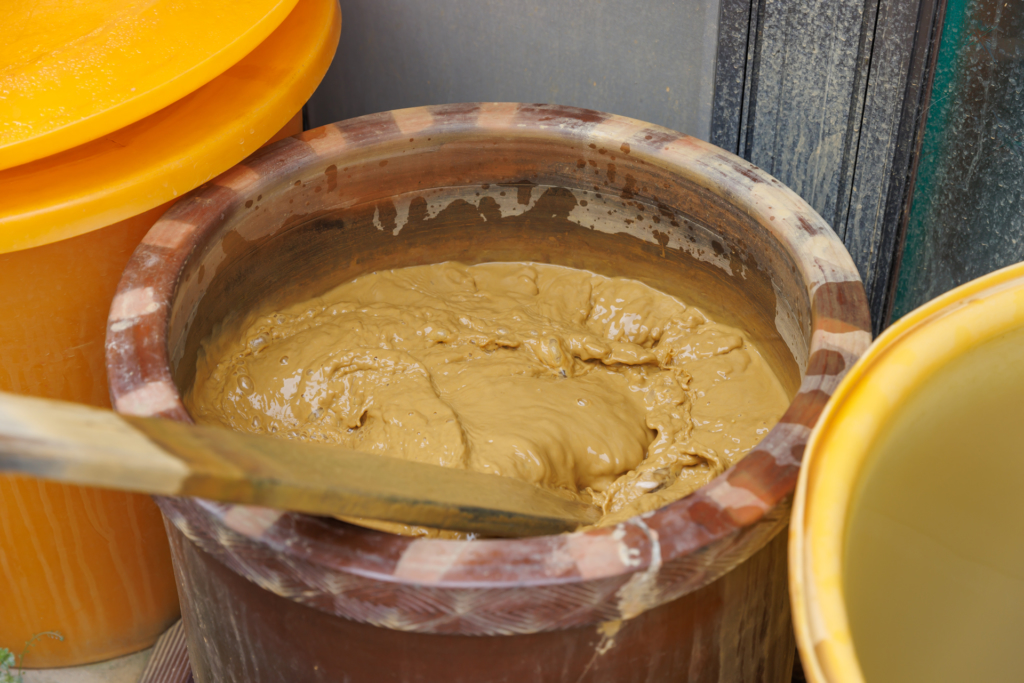
Colour changes with clay and firing method
Can’t we keep the base of vermillion mud, but change it in some way? The artist is also experimenting with new methods. A traditional method used in Tokoname is to seal rice husks and other materials together with the clay to form carbon on the surface, burn it black, and then polish it slightly with sandpaper to bring out the vermilion colour. Mr Ito arranges this method and pursues his preferred finish, asking himself if he can achieve a metallic, metallic-like black. He also sometimes blends the vermilion mud he makes himself with a slightly different ceramic clay to enjoy the change in colour.
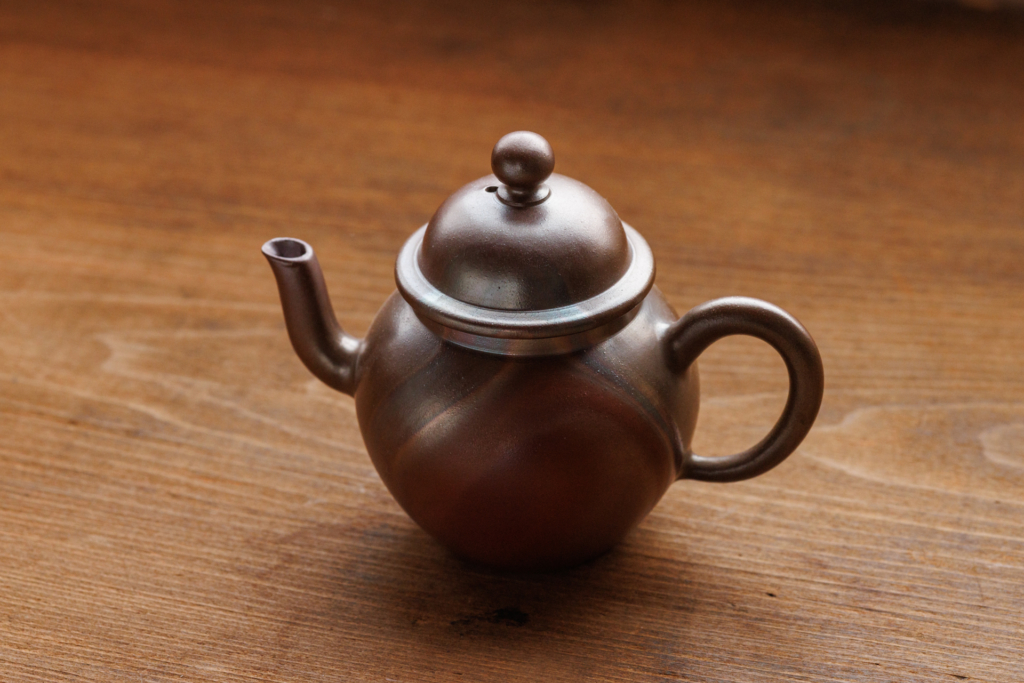
Arranging algae hangings.
Tokoname ware has a technique called ‘mo-gake’ that has been used since the Edo period. The technique is unique to Tokoname ware, in which seaweed is wrapped around the base and fired, causing the seaweed to melt and vitrify, giving the ware a pattern that is pleasing to the eye.
The only thing is that it’s just the same old technique done the same way as before. With this in mind, he has been searching for something that no one else has done yet, and has recently begun to use a method in which cedar leaves are rolled around the pot instead of seaweed. The charm of Ito-san’s kyusu is that it has the calmness of an old-style kyusu, but with a slightly sharp sense of style.
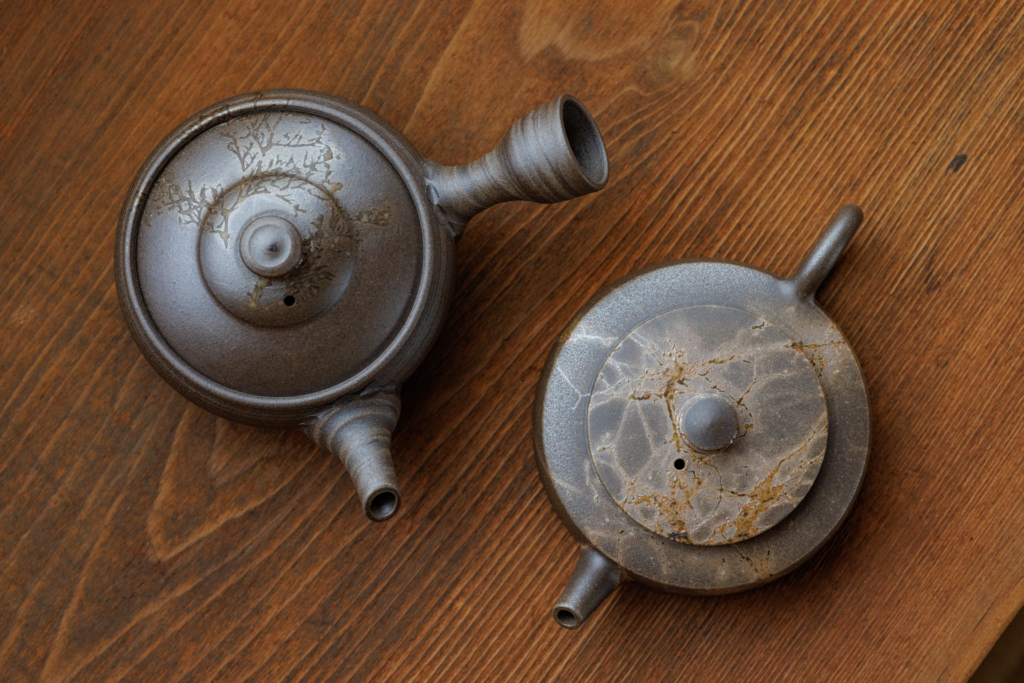
A teapot that makes you want to brew tea.
Mr Ito says he himself enjoys tea time on a daily basis. She is also active in new approaches to kyusu in the hope of helping more people to enjoy their tea time. Recently, she has been trying to make kyusu using soil from tea-producing regions, and is also involved in a unique initiative in which she invites people to send her soil via social networking sites, which is then made into a kyusu and returned to her.
While pursuing the old-style kyusu by arranging it to his own taste, he is also light on his feet when it comes to innovative approaches. We can’t take our eyes off what kind of chemical reactions they will create in the future.