Works that change the atmosphere
There are certain pieces of work that brings a kind of tension in the air. Works by Istuo Shoji whom we interviewed was like that.
What Shoji make are cast metal craft work. Melted metal is cast into molds and cooled so it would form a shape. After it’s taken out from the mold, the item is polished and decorated for completion. The presence of the cold beauty and the luster of the metal changes the atmosphere of the room it is in.
Shoji is an artist belonging to the Japan Kogei Association who’s won many awards. One of his recent works with which he won an award in 2008 was a rogin flower vase. The award was given to his work with a unique flat flower vase that betrayed people’s conception of a pot shaped container. Instead, in addition to the flat shape, the work repeated a triangular design at the mouth and the overall shape and has a kind of rhythm in the its shape.
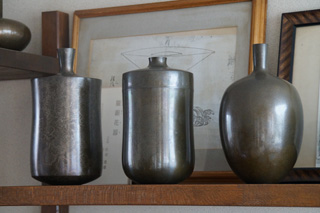
Creating the expression of metal
What heightened the value of the design was the surface or “skin” of the vase. Cast metal needs to have a mold, which determines its overall shape. At the same time, processes like polishing define cast metal work. Shoji’s flat vase expressed the texture of the ”rogin” material well, with an exquisite balance.
Nakata, looking at the shelf were Shoji’s work was lined up, stopped at a deep brown vase. “Did you paint this with “urushi” lacquer?” Nakata asked Shoji, who answered
“Yes. Cast metal is not just about showing bare metal. I sometimes paint over with “urushi” lacquer, etc. to give it a different expression.“
“You know I just noticed that the ones on the right and the ones on the left seem to be a little different from each other?” Nakata noted. On one side were larger works, and the other side had smaller ones.
”These are crafts, not just art pieces. They have to be usable, in other words they have to be something that people want to buy and use. That’s an important point. If it’s too large, it would take up too much space. That’s why they are staying with me. I sometimes present them to facilities like schools.”
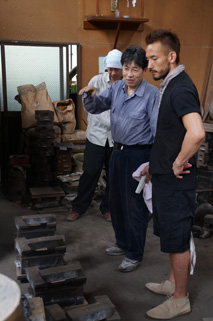
Using fire and alloy
After we were done talking, he showed us how he melts metal and makes the castings. First Shoji brought a bronze bar. It even looked like a piece of wood at first, but when he set it on the floor, it made a metallic sound that made us realize what it was made of . It was heavy, but this time he was going to make a lid for a metal kettle, so he was working with a relatively small amount of bronze, but if he was going to make anything larger, the amount of bronze needed would be substantial. He then placed the bronze into the burning flame that was making a big noise as the flame burned. When it was all molten, the metal was taken out of the flame. “This is the hard part. He smiled as he worked. “Even if you feel hot, or even if you get a burn, you can’t spill this. We were wondering how he could smile in this situation. The timing when the metal is taken out of the fire changes according to the alloys and the mold. That timing makes a big difference to the outcome of the work, so it is really where the craftsman’s experience and instincts count. After being removed from the heat, the metal is set in the mold and cooled. The metal is smoking even when in the mold, and it is easy to tell how hot it was. When the metal cooled down, we could see how it was molded cleanly into a lid. It was then finished by polishing.
The heat and the flames of the workshop was unimaginable from the cool and serene impression of his work.
Shoji is the representative of a casting workshop called “Sanoya”. Sanoya is said to be founded around the year 1350, so the workshop has about 600 years of history. In addition to keeping the tradition, he adds new taste and contiues delivering his products out to world.
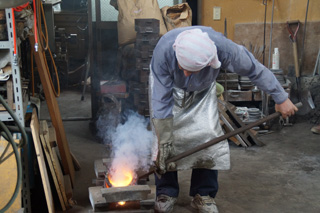
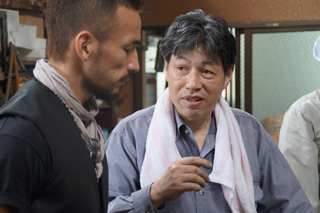