Lacquer patterns on moist deerskin leather. Koshu Inden” is a representative craft of Yamanashi, and is sold in many department stores nationwide. In recent years, Yusuke Yamamoto, the third generation of “Inden-no-Yamamoto” (Yamamoto of Inden), has been attracting attention for his innovative attempts. What is the “new form of Inden” that he embodies?
The Roots of Koshu Inden
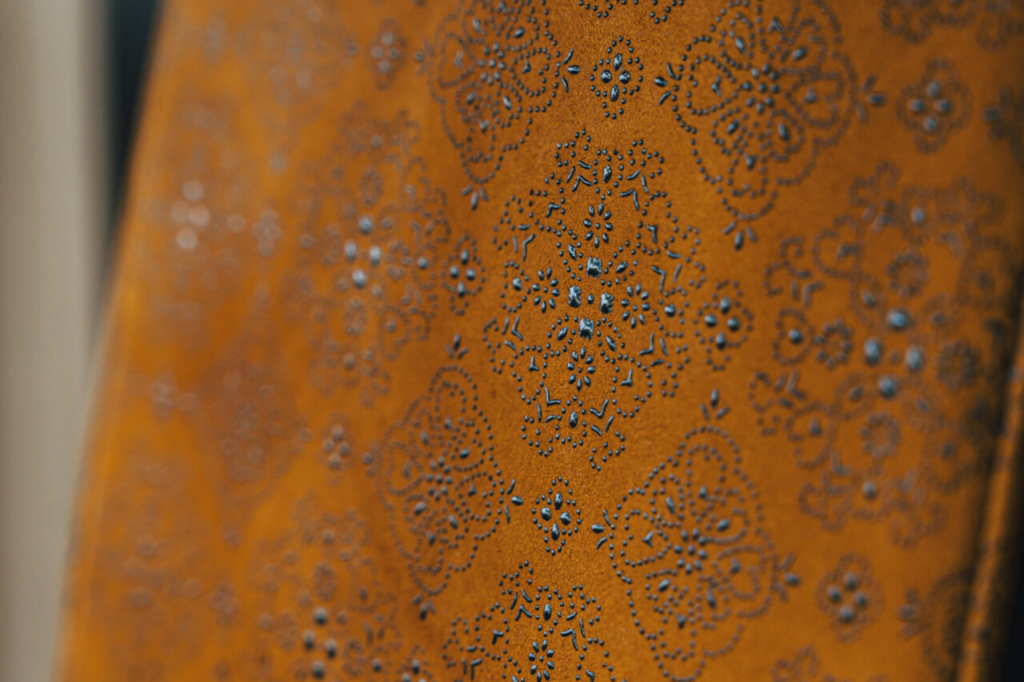
Koshu Inden” is a traditional Yamanashi Prefecture craft in which a pattern is applied to processed deerskin with lacquer. The word “Inden” is said to have originated from “Indea leather,” which was made in the 1600s by imitating the Indian (Indian) ornamental leather presented to the Shogunate from abroad.
Going back in history, it is said that deerskin processing began in Japan in the 400s AD. Deers have been abundant in Japan’s mountain forests since ancient times, and it is said that this is because they were easier to process than cows and horses. Deerskin was used for samurai armor after the Onin War (1467-1477) because of its lightness and high strength, in addition to its flexibility to fit comfortably in the hand. It is said that Shingen Takeda, who later became a feudal lord and protector of Kai Province, was also fond of this material, and came to love to use it for armor and “Shingenbukuro,” a deerskin armor pouch. This is said to have been the foundation of Koshu Inden.
In the Edo period (around 1700), a leather craftsman in Koshu invented the technique of lacquering, which is still used today, and this led to the production of high quality leather products in Yamanashi Prefecture. In the Meiji era (1868-1912), Koshu Inden became well known throughout Japan when it was awarded a medal at the National Industrial Exhibition. Although there have been several places in Japan that produce leather products using lacquer, Koshu Inden is the only one where the manufacturing process is still in use today.
The Beginning of “Inden-no-Yamamoto
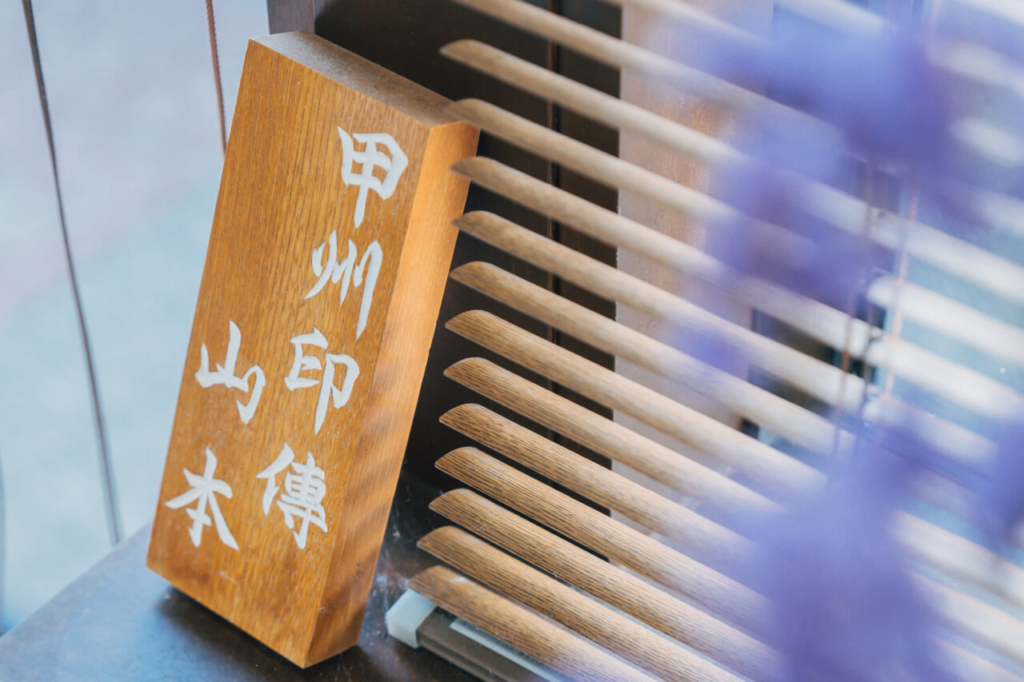
In the late Showa period, there were several Koshu Inden businesses in Yamanashi Prefecture, but today there are only two. One of them is Inden-no-Yamamoto Ltd., which has a workshop in Asake-cho, not far from the center of Kofu City.
Yusuke Yamamoto, a Koshu Inden traditional craftsman (general category), is the third generation to inherit the skills of the company. In addition to workshops and lectures, he has attracted attention for his innovative activities, including collaborations with game companies, animation, manga, and major brands. The history of “Inden-no-Yamamoto” began after the end of World War II, when the city of Kofu was burnt to the ground, according to Yusuke.
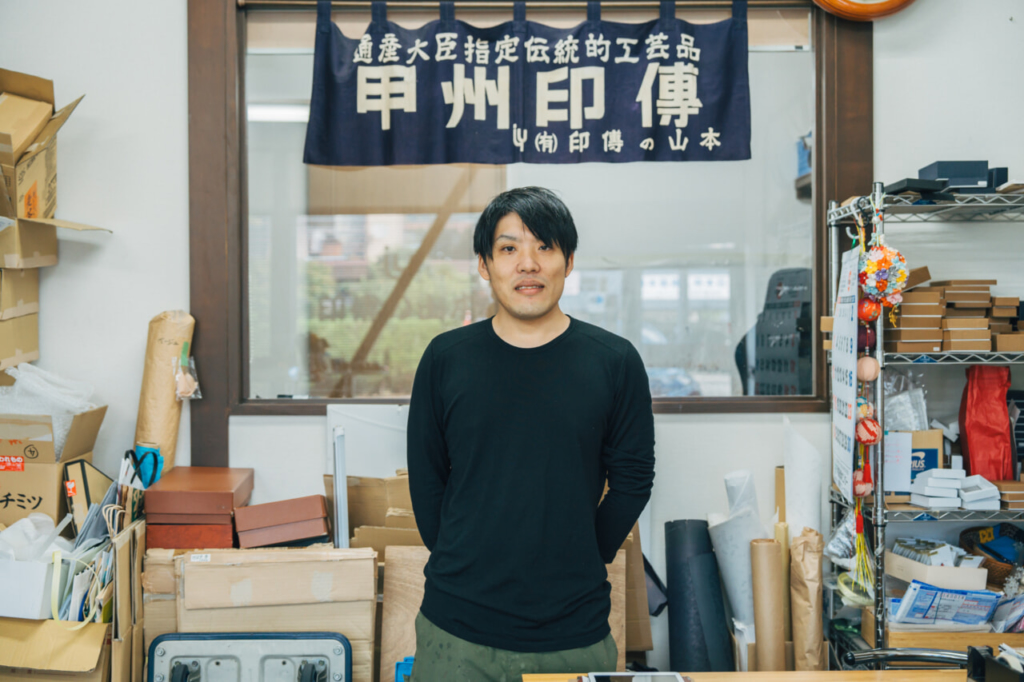
Restoring the Fire of Koshu Inden
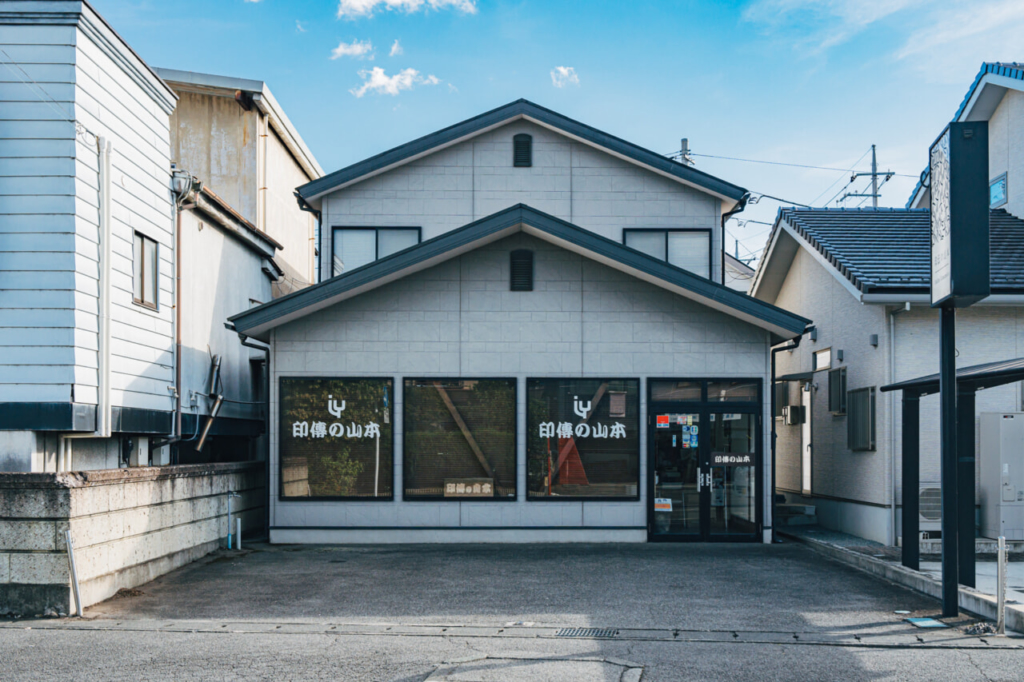
The founder was Kinnosuke Yamamoto, Yusuke’s grandfather. However, due to restrictions on deerskin leather caused by the shortage of supplies during World War II, the Koshu Inden business stagnated. Finally, he too was sent to the war zone. Upon his return, he found the town of Kofu scorched and transformed.
He must have seen the burnt-out ruins of Kofu and thought that everything would have to start from scratch. My grandfather was determined to ‘rekindle the fire of Koshu Inden once again. He established Yamamoto Shoten, a subcontractor to a bag manufacturing company in Tokyo, and began producing Koshu Inden again while saving money by making school bags.
Kinnosuke incorporated the rich colors he witnessed overseas into his products, and began producing products dyed in colors not found in conventional Inden. After the war, restrictions on deerskin leather were lifted in 1952, and the number of inden manufacturers gradually increased along with the demand for products, leading to the establishment of the Kofu Inden Merchant Cooperative Association around 1975.
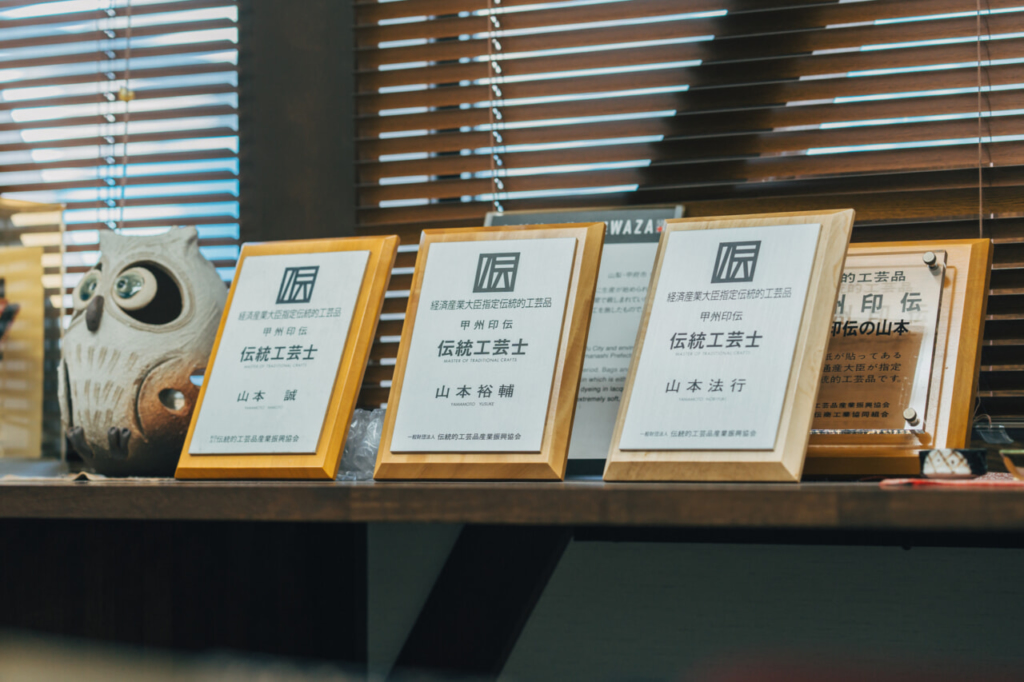
In 1996, he passed the certification examination for traditional craftsman of Koshu Inden, and began to produce a wide variety of products as the only traditional craftsman in the prefecture who handles everything from processing to decoration. Mr. Makoto is the only traditional craftsman in the prefecture who handles everything from processing to decoration.
Instead of the traditional wholesale sales through wholesalers, Makoto has shifted his focus to direct manufacturing and sales, where he listens directly to customers and develops products. By doing so, he expanded new needs and created new products one after another that were not bound by conventional wisdom, combining the techniques he inherited from his predecessors with a rich variety of colors.
As a bearer and communicator
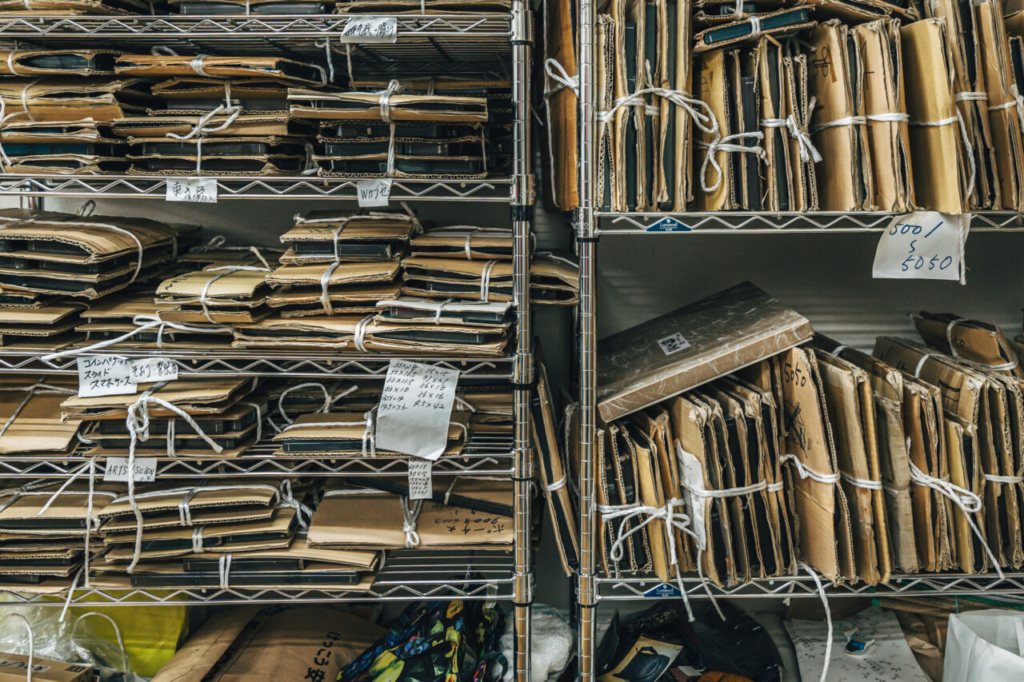
Yusuke looks at the shelves piled with colorful deerskin, “The style of giving shape to customers’ voices has been passed down to this day as one of the strengths of Inden-no-Yamamoto,” he says. Even now, the company is developing products in a variety of color variations, made to order, in response to customer requests.
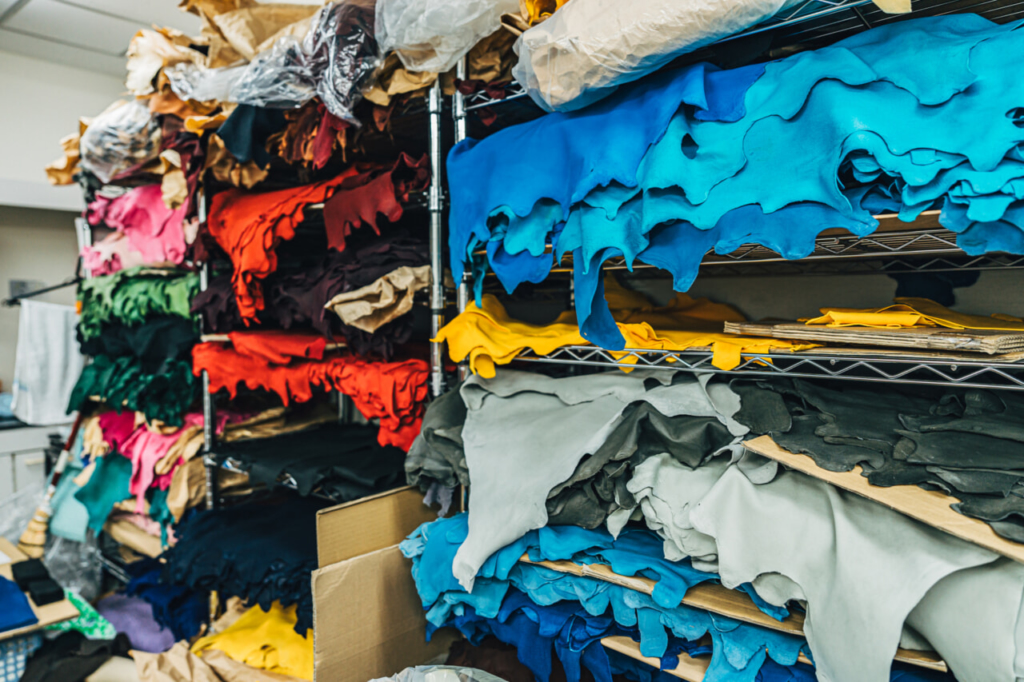
Yusuke decided to enter the world of Koshu Inden when he graduated from junior high school. His father, Makoto, was certified as a “traditional craftsman” by the Association for the Promotion of Traditional Craft Industries. He had never been interested in Koshu Inden before, but he became very curious about the possibilities of Koshu Inden.
By the time he finished high school, he chose to study commerce at a university outside of the prefecture, with an eye toward eventually taking over the family business. After graduating from college, he entered the family business and began his career as a craftsman in earnest.
Technology passed down from generation to generation
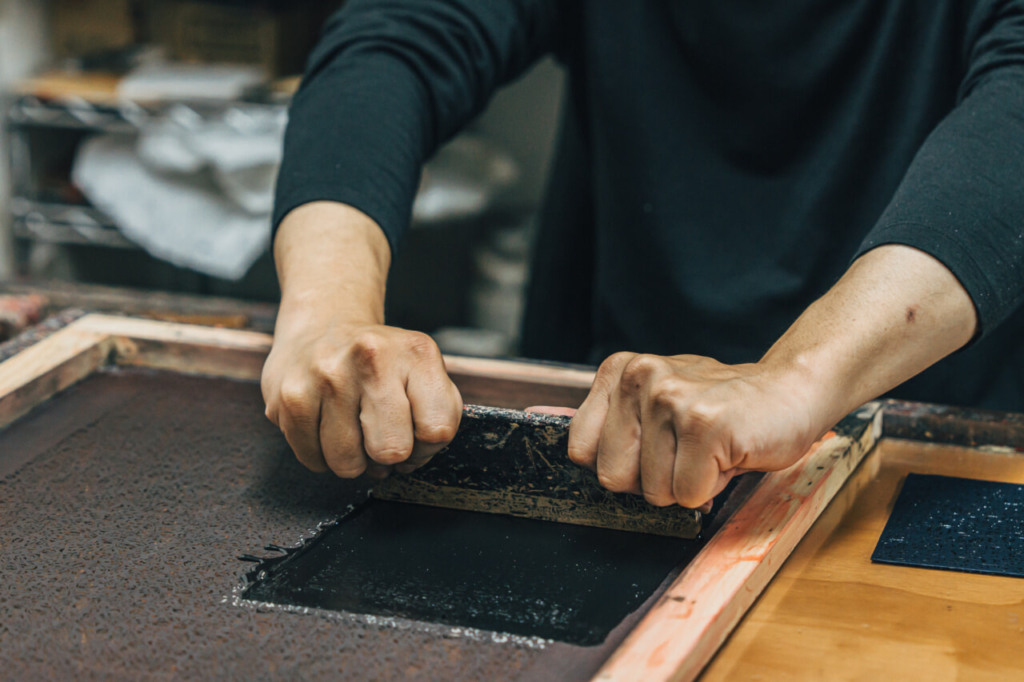
Dyeing: Dyeing the surface of the deerskin by processing and coloring the surface of the minstrel’s skin so that the lacquer will adhere well to the surface. Cutting is done to roughly trim the leather to the appropriate size for the product to be made. Pattern application, which is the essence of Koshu Inden. Sewing: Cutting the leather and shaping it into the product. Yusuke handles all four of these processes by himself.
The lacquering process takes only 5 to 6 seconds, but he says that he puts his utmost effort into these few seconds. He says, “The finish depends on the amount of force I use. It is no exaggeration to say that everything is decided here. The “Urushi-tsuki” technique is applied by layering hand-carved paper stencils on top of deerskin and brushing lacquer onto the surface with a wooden spatula.
In many cases, the materials used for deerskin, paper stencils, and lacquer are sold wholesale to craftspeople rather than to consumers. Yusuke is concerned that “if the production and consumption of Koshu Inden cannot be sustained, the industry of those involved will not be able to survive. The relationship between producers of raw materials and craftspeople is truly “hand in hand. Holding a finely hand-carved pattern in his hand, Yusuke’s expression reflects his sense of responsibility as a bearer of the craftsmanship.
Let’s talk about the future.
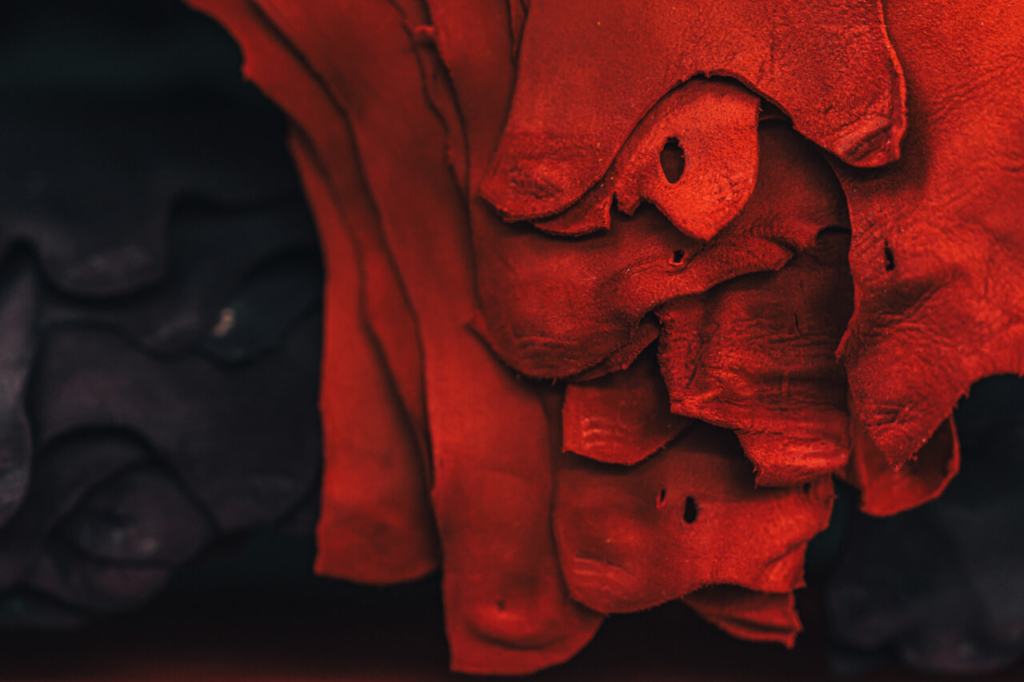
Lacquer trees used to grow in abundance in Yamanashi Prefecture, but due to changes in demand and lifestyles, the number of lacquer trees has decreased significantly. He and other volunteers are attempting to plant lacquer trees in Hokuto City, saying, “We rely on imports from China for the lacquer we use to make patterns, but eventually we would like to make products only from Japanese lacquer.
While it has become more difficult to purchase deerskin from abroad in recent years, the number of wild deer in Yamanashi Prefecture is on the rise. It is said that about 70,000 Japanese deer live in the prefecture, and in recent years, animal damage has become a serious problem in cultivated land. In 2014, the company launched “URUSHINASHIKA,” which competes with Yamanashi Prefecture’s project to prevent beast damage, and is working to make effective use of Japanese deer captured as vermin in Koshu Inden.
He hopes that this will be a breakthrough in securing materials, saying, “If it becomes possible to make inden from deerskin produced in Yamanashi Prefecture, the prefecture’s traditional handicrafts will gain more depth. Yusuke’s desire to continue and popularize Koshu Inden as a bearer and a conveyer of the art is spreading like ripples.
New Inden Shape
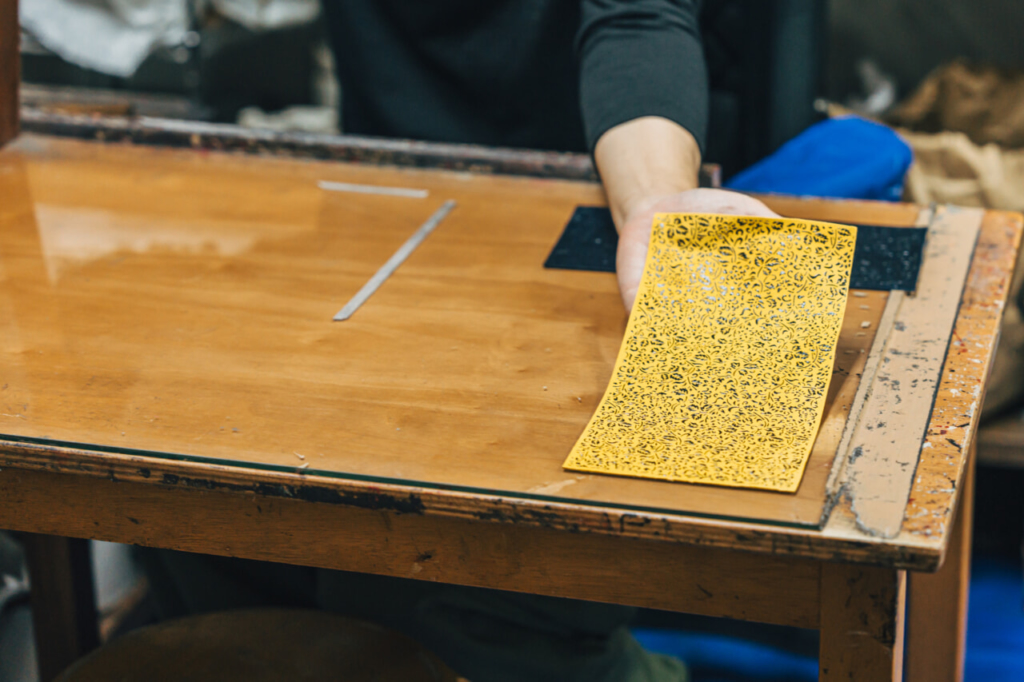
Currently, Inden-no-Yamamoto is brushing up on the policy of his father Makoto, who mainly sold his products in department stores, and focusing on expanding sales channels through direct orders and sales at the workshop, which is one of the company’s strengths, corporate collaboration product development, and on the Internet. The demand for their products ranges from order-made products, which can be commissioned even for a single item, to the development of cup sleeves in collaboration with a major coffee chain, wall panels for stores, and the production of card holders for government officials.
Koshu Inden has become well known in the market. Recently, we are working on new product development so that the appeal of Koshu Inden can be known not only in Japan but also overseas.
Many people overseas do not like animal products such as deerskin leather from the viewpoint of ethics and environmental pollution during the manufacturing process,” says Yusuke. Therefore, in early 2023, he will release a new brand “obudo (obudo) ®︎” using “ultra-suede,” a leather made from vegetable materials instead of deer skin. The company has released a series of products that are animal-free and have a sophisticated design not seen in previous Koshu Inden products.
The company hopes that its new brand, “obudo,” will help people to understand the appeal of Koshu Inden to a wide range of people,” and presents a new and free form of Inden that meets the needs of the times, while preserving the tradition. The company’s next step is to pass on its techniques to the future.
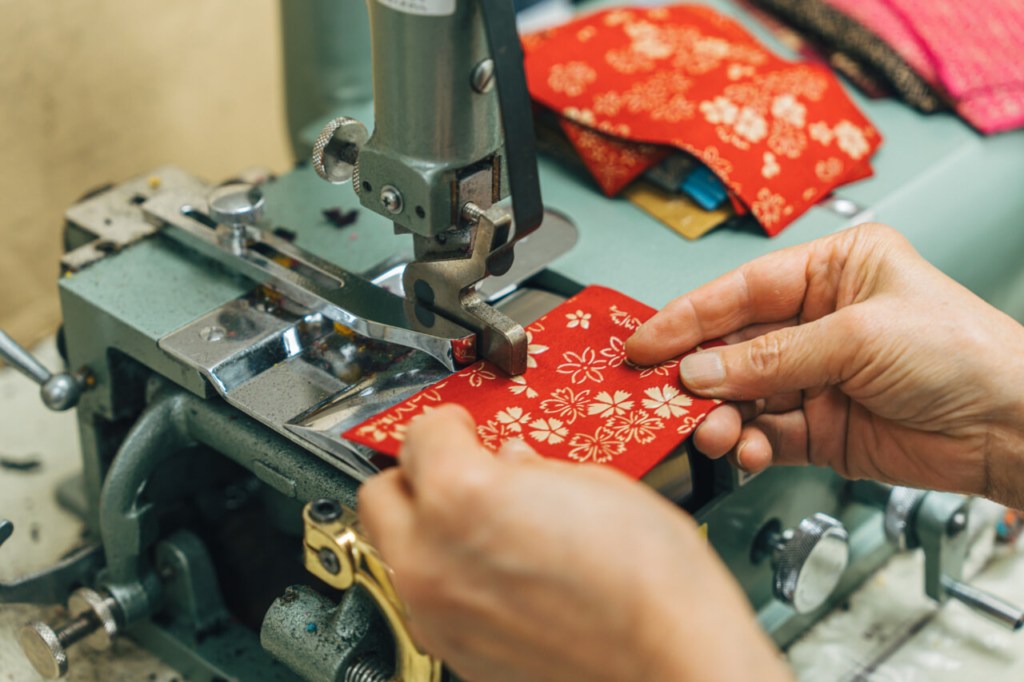
While demand for Koshu Inden is increasing, it is undeniable that the region lacks power. The company is also working to create a foundation for more people to be involved in the business by promoting the use of electronic manuals and the digitalization of paper patterns.
The essence of Inden is technology. I would like to broaden the scope of Inden with more free ideas and create products that are demanded by customers and the times,” says Yusuke, who is full of energy.
A strong belief that conveys the backbone and identity of the company. A lighthearted attitude that is not bound by molds or stereotypes. A soft and flexible imagination that adapts to the needs and lifestyles of the people who hold them in their hands. Yusuke’s works and techniques, which continue to embody “a new form of Inden,” may be rewriting the future of traditional crafts.
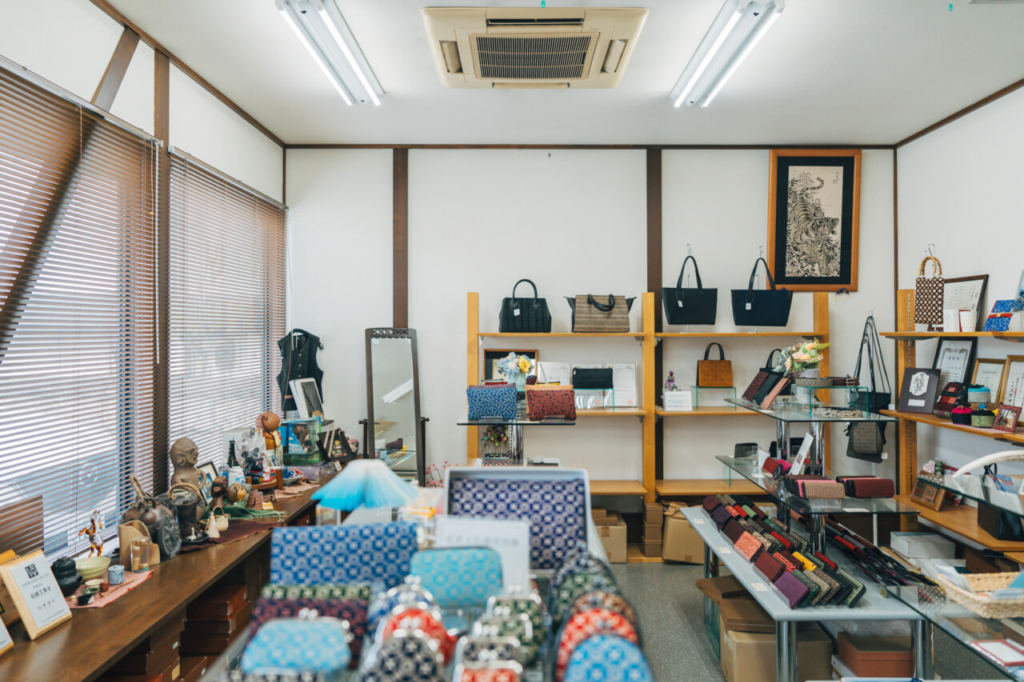