Textile that is passed on in Nagai, Yamagata
Oitama Tsumugi, designated as a traditional ”kotei” of Yamagata Prefecture, is the collective name for traditional textiles made in three regions within Yamagata Prefecture. To name each, they are Yonezawa Ori, Shirataka Ori, and the Nagai Tsumugi produced in the Nagai Basin. Nagai Tsumugi flourished due to the promotion of the textile by Yozan Uesugi who became the lord of Yonezawa during the Edo period. It was developed further when instructors were invited from Niigata, and the skills for making “kasuri” spread, and the modern-day Nagai Tsumugi developed into the current form. One of the attributes that make ”Nagai Tsumugi” popular, is how it has brilliant and vivid patterns in spite of the soft texture.
The vivid patterns are another feature, very similar to Yoneryu Kasuri from the Ryukyu region. We interviewed traditional craftsman Masayuki Nagaoka, who weaves the beautiful Nagai Tsumugi.
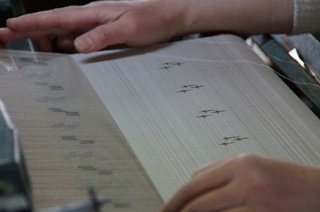
The ”Kasuri” skills used on Nagai Tsumugi.
Nagaoka has been working on Nagai Tsumugi for nearly 30 years. He has won awards at dyeing and weaving contents across Japan, including the Minister of Education Award. Nagaoka took us to the workshop where they were in the middle of the weaving process.
As explained, the “kasuri” skill is used for Nagai Tsumugi. “Kasuri” is a method where threads are dyed in advance, and patterns are woven onto the textile. Various patterns are generated by the combination of warp and weft . With Nagai Tsumugi, the “kasuri” dyed threats are used in weft and called the “yoko kasuri” (horizontal “kasuri”). We were shown how the threads were woven. It was a quite complex process.
This is called ”ayaori” he told us as he showed us a fabric. ”ayaori” creates a different pattern in the foundation, by adjusting the vertical threads. The threads cross at an angle, creating a pattern called ”shamonsen”, which brings out a totally different charm. There are many variations of ”Kasuri”, each with its unique feature, and how these are used can add dimension and character to the finished product.
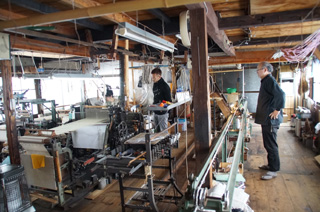
Adding color using ”surikomi zome”
There is a method used for “kasuri” called “surikomi zome” where dye is rubbed into the threads with a bamboo spatula. This method increases the variation in color and patterns. “Surikomi zome” became popular after WW2, but it made it possible to create patterns on light colored thread, enabling the manufacturing of bright colored textiles which became popular after the war.
”Surikomi” is also often used in “Yuuki Tsumugi”. There was an old hand weaving machine in Nagaoka’s workshop. “Yuki Tsumugi is still made with this machine.” he said, and allowed Nakata to use the machine. With a loom, the warp is hung from the loom, and the weft is woven into the warp. Normally, all of the weft is hung on the machine, but with this loom, the craftsmen supports the front part with his hip to hang the threads, so he becomes a part of the machine. “This is really difficult! You need to develop your intuition, and it also requires a lot of effort.“ Like Nakata said, it required high proficiency on the part of the operator. “Nagai Kasuri” has a natural texture that makes you feel the simple and natural warmth. It is a tradition that continues from the Edo period that should be actually worn, not just looked at.
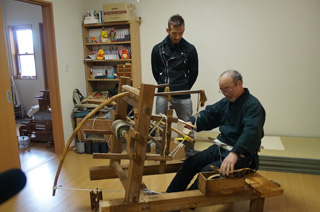
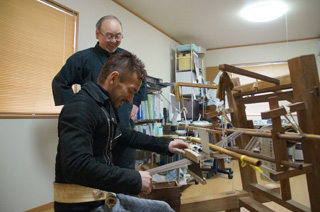