Karamushi fabric is cool like hemp
”Karamushi weaving” is a designated Important Intangible Cultural Property. of FUkushima. The fiber is taken out of out of ramie or ”Karamushi”, a perennial plant of the urticaceae family, spun into yarn, and women to make fabric. At first glance, it looks like hemp cloth, but it is firmer than hemp. It is versatile and can be used for small accessories to fabric for kimono.
While Miyako or Ishigaki are famous for high quality fabric using ramie, Showa is the only region on the mainland of Honshu where ramie is grown. We were told that it has been passed down from generation to generation under strict quality management for about 600 years.
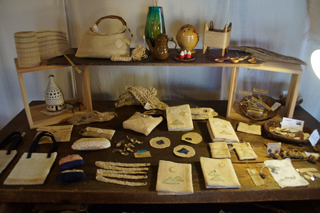
The appeal of Karamushi weaving
We visited a workshop in Showa village and spoke to Tamaki Saito, a Karamushi weaver. Saito is not a native of Showa village. In fact, the village government recruits four trainees every year to relocate to Showa village and learn about Karamushi weaving. Saito came to Showa village as one of those recruits. She remembers being impressed with the snow covered scenery when she first arrived.
”What made you want to try Karamushi weaving?” Nakata asked, to which she laughing answered ”Actually, I didn’t have any particular reason.”
”I can grow the ramie, spin it, and weave it. I can create it with my own hands from start to finish. That had the greatest appeal. It made me want to try it out. And Karamushi has been passed on from generation to generation, and is ingrained in the local lifestyle. I am very enchanted with Karamushi weaving and life in this village now.”
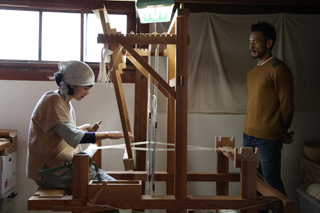
Spinning takes the most time
Saito is involved in the entire process from start to finish. She grows the plants, harvests it, spins yarn and weaves. Of all the different steps, what is most time consuming, more than sitting in front of the loom, is spinning the yarn.
We observed the spinning process. Dried ramie fibers are soaked in water to soften, then split one by one using a nail, and are twisted by hand to connect them together.
”The thickness of the thread that is used for kimonos is different from that used for small accessories. It is difficult to make thin thread. It takes a lot of time.” Each technique was taught by the elderly women in the village.
Carrying on the tradition of Karamushi weaving
Even now, Showa village recruits Karamushi weaving trainees every year. They are out in the fields from spring to fall, and also spinning yarn. In the winter, they weave Karamushi fabric using the yarn. Among the trainees, there are many who remain in Showa village and continue making Karamushi fabric. The tradition that is alive in the local region continues to attract people to the area.
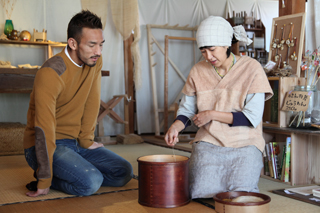