Committed to “kozo”
Ichibei Iwano is the 9th generation in a line of ”Echizen washi” craftsman working in the Echizen region. ”Echizen washi” is made from materials such as ”ganpi” (a species of flowering plant), ”mitsumata” (a species of birch), ”kozo” (paper mulberry) and hemp. Each of these plants has long fibers and can be made into flexible and tough paper. So ”Echizen washi” was manufactured in large quantities for use as ”hoshoshi” (thick Japanese paper for ceremonial use) in early times. Today, it is used in Japanese-style paintings and woodblock prints among others.
There are many different methods for processing ”Echizen washi”, including mixing it with various materials, but Ichibei Iwano has continued to use only ”kozo”. In the past, ”kozo” could be collected near Kuzuryu Dam, it ’s availability declined, and Iwano now uses Nasu-kozo from Ibaraki. In order to make the most of the characteristics of the materials used, no chemicals are used, including bleaching agents, except for the soda material used to boil ”kozo”.
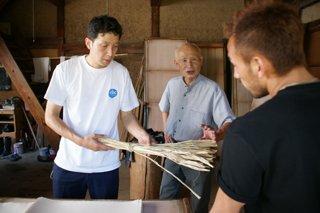
Experiencing paper making
The process for making ”washi” starts with removing the bark from dried ”kozo”. The white bark is boiled in a large bowl, and discolored parts and dirt are removed by hand, one by one. Then it is beaten to make the fibers fiber before being put into a ”sukifune” (wooden tub for paper making) filled with water. By that point, fibers disperse in the ”sukifune”. A tool called ”suketa” is used to scoop the fibers, and shaken back and forth to smooth the fibers. This process of making paper requires a great deal of experience, skill and care to ensure the thickness is uniform.
Nakata was allowed to try making paper himself.
After only about three scoops, clumps began to form on the ”suketa”.
Nakata asked for advice, and with a smile on his face, Iwano told him the only advice was to become accustomed to the process. Apparently, little ripples in the water was causing wrinkles and clumps to form, preventing him from being able to create beautiful, uniform paper.
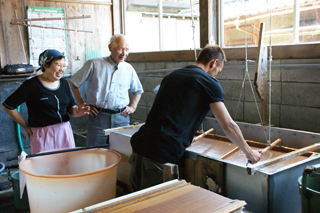
Strong and beautiful ”washi”
The paper is then layered, and squeezed to remove excess water, then each individual sheet is placed on a board to dry. Using both hands, Iwano pulls off a sheet of ”washi” that has just been completed.
He told Nakata to tug on the paper without pressing on it with his fingernails. Nakata pulled with all his strength, but the paper showed no sign of tearing.
“Even some strong like Nakata-san cannot tear it. Even a sumo wrestler wouldn’t be able to tear it,” Iwano told us.
Some of the woodblock artists who use Iwano’s paper may apply color 200 to 300 times in order to complete a picture. This means the paper must be tough. Iwano’s paper is highly regarded for its ability to bring out great color, and is popular with many artists. High quality ”Echizen washi” is essential to complete works of calligraphy, Ukiyo-e, and Japanese style paintings.
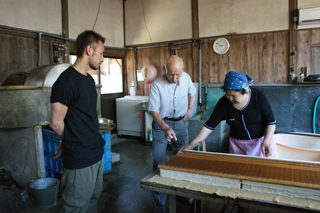