Iwate Prefecture is Japan’s top producer of charcoal, accounting for approximately 30% of the nation’s total output. As a producer, judge at charcoal evaluation competitions, and one of only 25 prefecturally certified charcoal makers (Charcoal Masters), Tanichi Tsukasa, the kiln master at Tanichi Forestry, plays a pivotal role in supporting Iwate’s charcoal industry. While mentoring the next generation, he is dedicated to crafting charcoal that is easy to light and burns well.
Iwate charcoal is renowned for its top-notch quality and quantity.
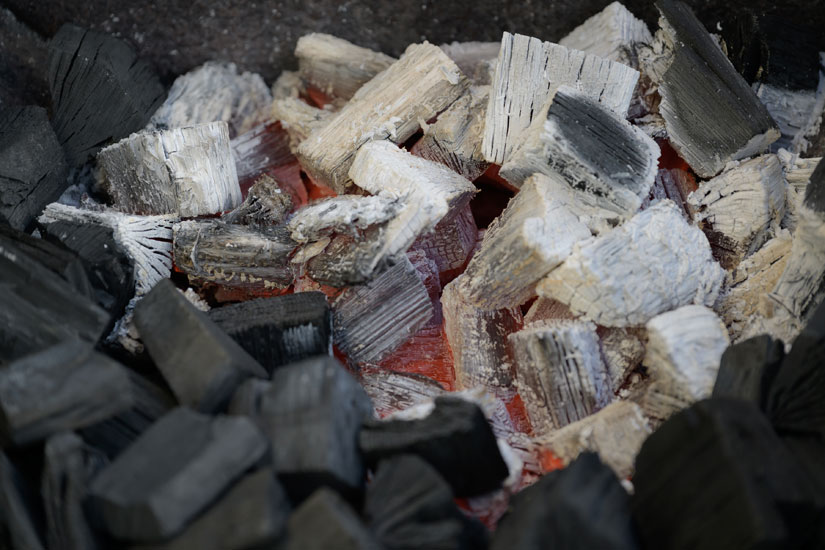
Charcoal is made by heating wood in an oxygen-free or low-oxygen environment to remove oxygen, hydrogen, and impurities, leaving only carbon. It has the characteristic of producing little smoke or odor when burned and has been used as fuel since ancient times. The history of charcoal in Iwate dates back to around 1,100 years ago, as evidenced by excavations at the Hiraizumi archaeological site. Since then, it has been produced using abundant forest resources, and production and shipments increased significantly in 1891 with the opening of the Tohoku Line, targeting the Tokyo market. In 1905, the prefecture encouraged charcoal production and introduced new technologies as part of relief measures following a severe crop failure, leading to Iwate achieving the title of “Japan’s top charcoal producer” in 1912. Subsequently, to ensure a stable supply of high-quality charcoal, the Iwate Prefecture Charcoal Association led research into kilns and techniques, resulting in the development of the current “Iwate Large-Scale Kiln.” These efforts led to the registration of the “Geographical Indication (GI) Protection System” in 2018. As a result, the name “Iwate Charcoal” is now protected, and only charcoal produced in kilns within the prefecture using local wood and with a refinement rate of 8% or less can be shipped as “Iwate Charcoal.” Incidentally, the refinement rate is a numerical value representing the electrical resistance of charcoal, with lower values indicating higher carbon purity and thus better quality charcoal.
Popular in restaurants and camping
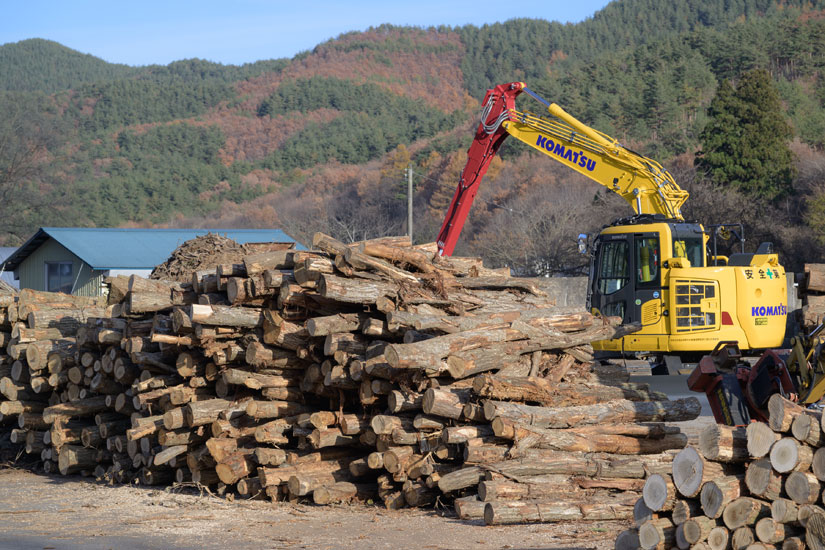
Wood charcoal is primarily divided into two types: white charcoal, which is carbonized at temperatures above 800°C, and black charcoal, which is carbonized at temperatures between 400°C and 700°C. The former is difficult to ignite but burns slowly and allows for easy heat adjustment, making it ideal for use in restaurants. “Bincho-tan,” a type of white charcoal, is a well-known example. The latter is easier to ignite and produces intense heat, and Iwate charcoal falls into this category. Iwate Prefecture, which boasts the largest area in Honshu and is approximately 77% forested, primarily produces charcoal using oak trees aged 20–25 years. The abundance of oak trees and their hardness compared to other woods make them ideal for producing charcoal with excellent heat retention.
Among black charcoal, Iwate charcoal has many advantages, such as being easy to ignite, having good heat retention, producing little smoke or odor, and being less prone to cracking. The ease of ignition is due to the presence of bark. This is a major characteristic of Iwate charcoal, and some restaurants that use binchōtan use it as a substitute for ignition aids. Additionally, the fact that the bark is prevented from peeling off during the manual cutting of the logs is another key point. If the bark peels off, air enters, making the charcoal prone to cracking. Furthermore, the “refining” process, which involves burning at high temperatures, is carefully performed to burn impurities that cause smoke, odor, and cracking. The key here is to burn at temperatures of up to approximately 800 degrees Celsius to increase the “carbonization degree.” This results in charcoal that produces little smoke or odor and is less prone to cracking.
Iwate charcoal is popular for camping and barbecuing, and is especially valued for camping because it burns well and does not require large quantities. On the other hand, as mentioned earlier, production volumes are high, thanks to the “Iwate Large Kiln” developed by the Iwate Charcoal Association. The height and shape of the kiln have been carefully designed to facilitate the rotation of the fire and enable the production of large quantities of high-quality charcoal at one time.
The charcoal-making technique that won the Prime Minister’s Award
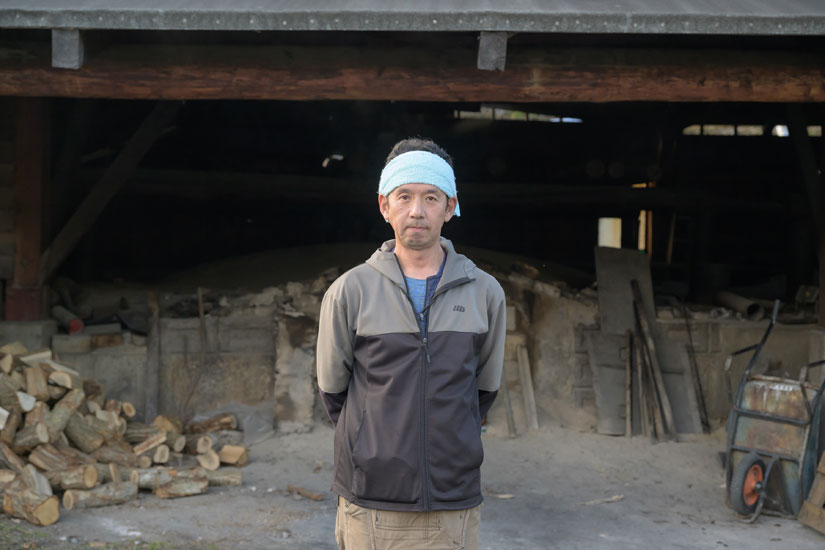
Iwate charcoal production is centered in the northern part of the prefecture, with Kuji City’s Yamagata Town being the most representative area. Approximately 80% of the town’s land is forested. The long winter, which is cold and snowy, results in an extended off-season for agriculture, during which many farmers earn income through charcoal production. Additionally, the abundance of soil suitable for charcoal kilns is believed to be a key factor in the thriving charcoal industry.
Tanichi Forestry, established in this area in 1916, has been producing charcoal using local wood since its founding. The third-generation kiln master, Tanichi Tsukasa, has won numerous awards at the Iwate Prefecture Charcoal Competition and, in 2018, became the first charcoal producer to receive the Prime Minister’s Award at the Ministry of Agriculture, Forestry and Fisheries Festival.
“I’ve been making charcoal for 20 years, but I’ve always wanted to create black charcoal that is similar to binchōtan,” says Tanichi. As mentioned earlier, white charcoal binchōtan has better heat retention than black charcoal. Therefore, he aims to create charcoal that retains the ‘ease of ignition’ and ‘strong heat’ of black charcoal while achieving heat retention and heat intensity closer to binchōtan.
The key is to dry the charcoal slowly through ‘pre-burning.’
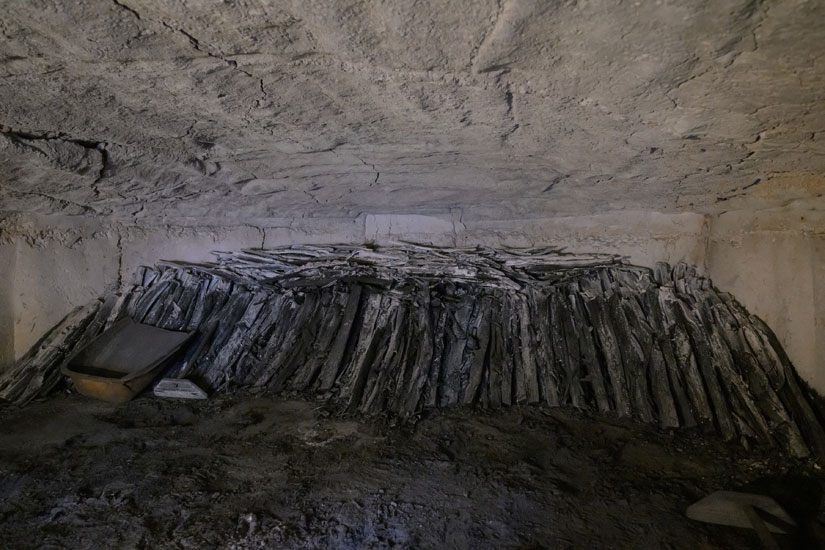
At Tanichi Forestry, like other charcoal producers in the prefecture, we cut oak logs into specified lengths and thicknesses, load them into kilns, pre-dry them, ignite them, and then regulate the oxygen levels inside the kiln to carbonize the wood into charcoal. The duration of each process has a general guideline, but adjustments are necessary depending on the moisture content of the logs, the temperature and humidity during production, and the combustion conditions. Timing is crucial, and this relies heavily on the experience and intuition of the producer. This ultimately determines the quality of the finished charcoal.
The step that Tanichi values most is the “pre-burning.” This involves burning firewood near the entrance of the kiln to raise the temperature and dry the oak logs. The key is to burn the firewood slowly to prevent the moisture from escaping too quickly, resulting in charcoal that is dense, hard, and less prone to shrinkage, with excellent heat retention and resistance to crumbling.
Understanding the unique characteristics of each kiln and mastering their use
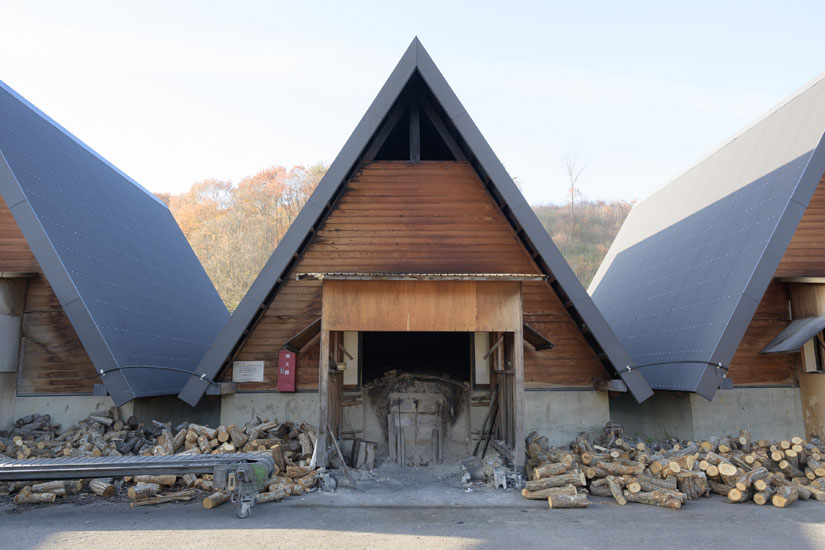
Mr. Tanichi has also developed his own methods for setting up and stacking oak logs in the kiln, as well as timing the extinguishing process. These innovations have led to awards at competitions and other events. Due to his numerous awards at the Iwate Prefecture Charcoal Competition, he eventually transitioned from participant to judge, and in 2018, he was certified as an Iwate Prefecture Charcoal Master.
To become a Charcoal Master, one must master not only charcoal production but also kiln construction techniques. “Even if you build kilns the same way, each one has its own quirks. We have 12 kilns at our company, so we take notes every time we make charcoal and use them as a reference for how to work and which kiln to choose,” explains Tanichi. Some kilns are even designated for use when making charcoal for competitions.
The finished charcoal is cut to the standard length and packed in special frames so that there are no gaps. All of this is done by dedicated staff. The skill and speed with which they arrange the charcoal without hesitation is a testament to their expertise. Additionally, the company ships charcoal under its own brand, “KUROSUMI,” in 3kg and 6kg bags, alongside its “Iwate-kiritan” charcoal.
For the future of the traditional charcoal-making industry in the region.
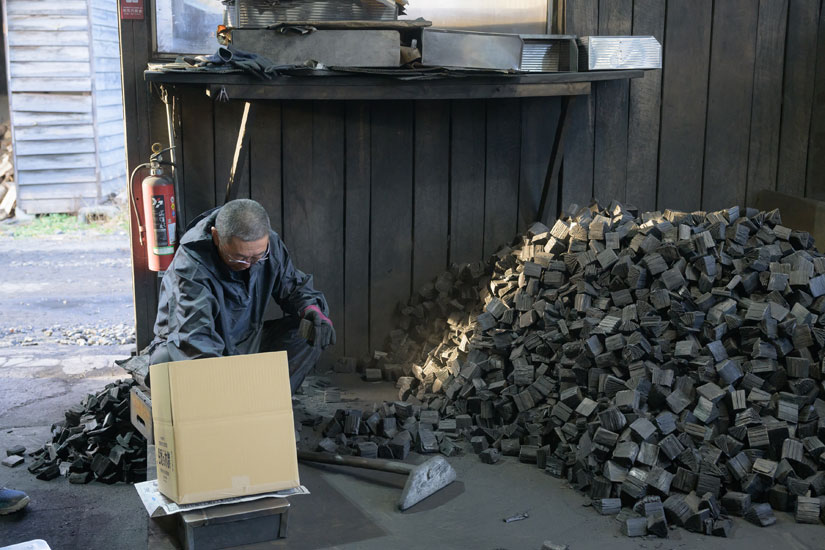
Mr. Tanichi is currently focusing his efforts on mentoring younger generations, eager to pass on his skills and knowledge. Despite the high demand for Iwate charcoal, approximately 80% of the charcoal sold domestically is imported due to its low price. However, the number of producers in the prefecture is declining due to aging, and supply is unable to keep up with demand. Mr. Tanichi hopes to train young producers and increase production.
He is also working on producing charcoal for uses other than fuel.
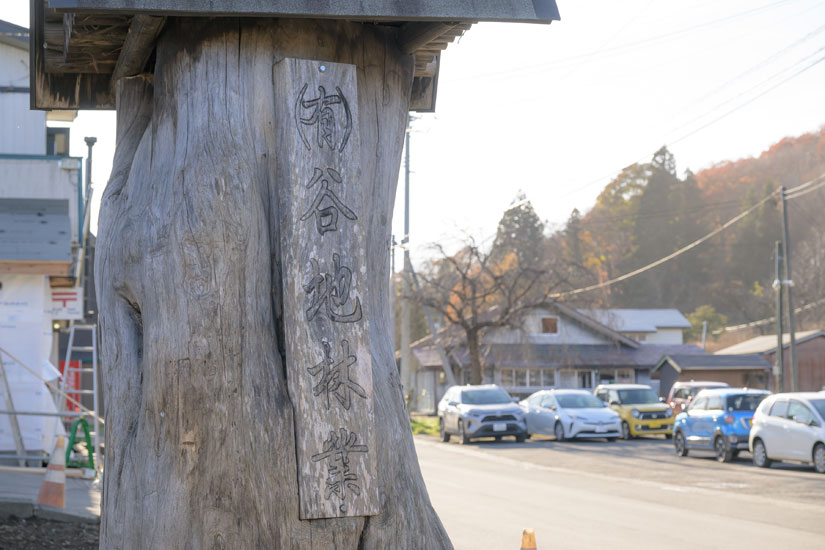
The company also plans to produce charcoal for uses other than fuel in the future. Charcoal has countless tiny pores, which absorb impurities and harmful substances and provide a habitat for microorganisms, making it useful for purifying water and air and improving soil quality. Additionally, its ability to absorb and release substances allows it to regulate humidity. Tanichi Forestry aims to leverage these properties of charcoal to produce charcoal for humidity control, deodorization, and soil improvement in collaboration with agriculture. This initiative also seeks to effectively utilize “unused materials” such as branches and leaves that have been left in forests and considered a challenge. As a traditional local industry and a business the company has been involved in for many years, Tanichi is dedicated to making the charcoal-making business sustainable, and continues to approach “charcoal production” with sincerity every day.