Walnuts” are indescribable for their gentle color and warmth when held in the hand. They have a delicious flavor and are good for beauty. Just their presence alone is enough to make one’s heart warm. Glass Studio Orange” produces glass that embodies the charm of walnuts. We asked them about the secret to their warm and inviting creations.
A glass studio nestled in the quaint scenery of an inn town
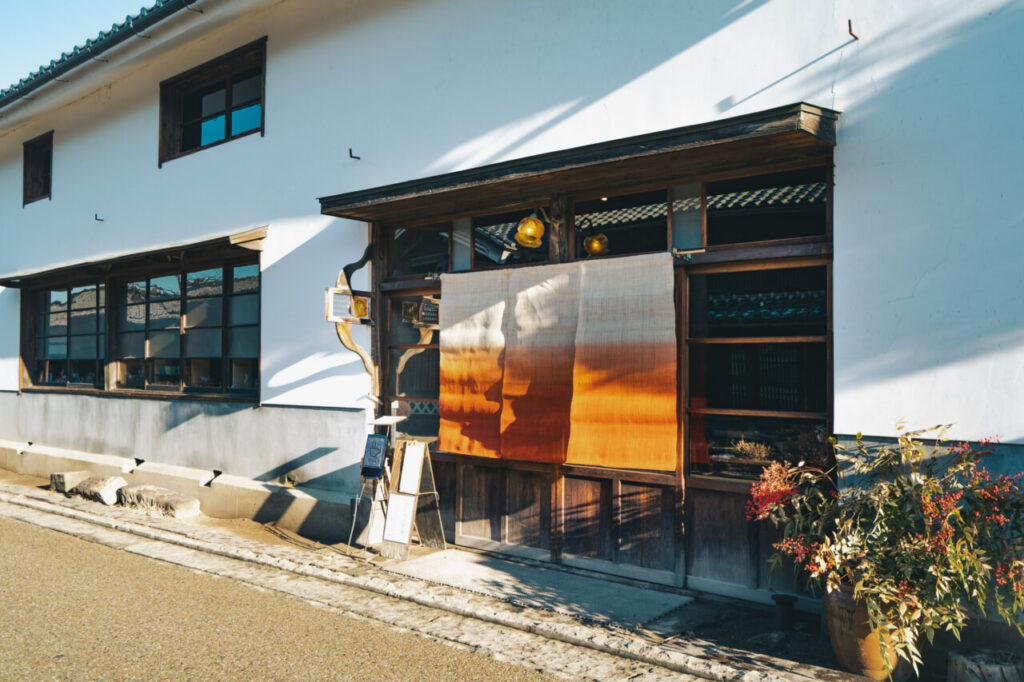
Tomi City is located in the eastern part of Nagano Prefecture. This small city with a population of about 30,000 people boasts the largest production of walnuts in Japan. It is walnuts. Currently, 99% of the walnuts distributed in Japan are from foreign countries, so domestically produced walnuts are extremely valuable and expensive. The market distribution volume has decreased due to price competition with walnuts imported from overseas. However, the city of Tomi City is proud to be the largest producer of walnuts in Japan, and is working hard to expand production and further brand the walnuts produced in Tomi City. In this town, there is a glass studio that uses walnuts, a local specialty, to make products unique to the city of Tomi, called “Glass Studio Orange,” which opened in the city in 1999. The head of the studio, Masaki Teranishi, is from Maruko Town (now Ueda City), a neighboring city of Tomi City.
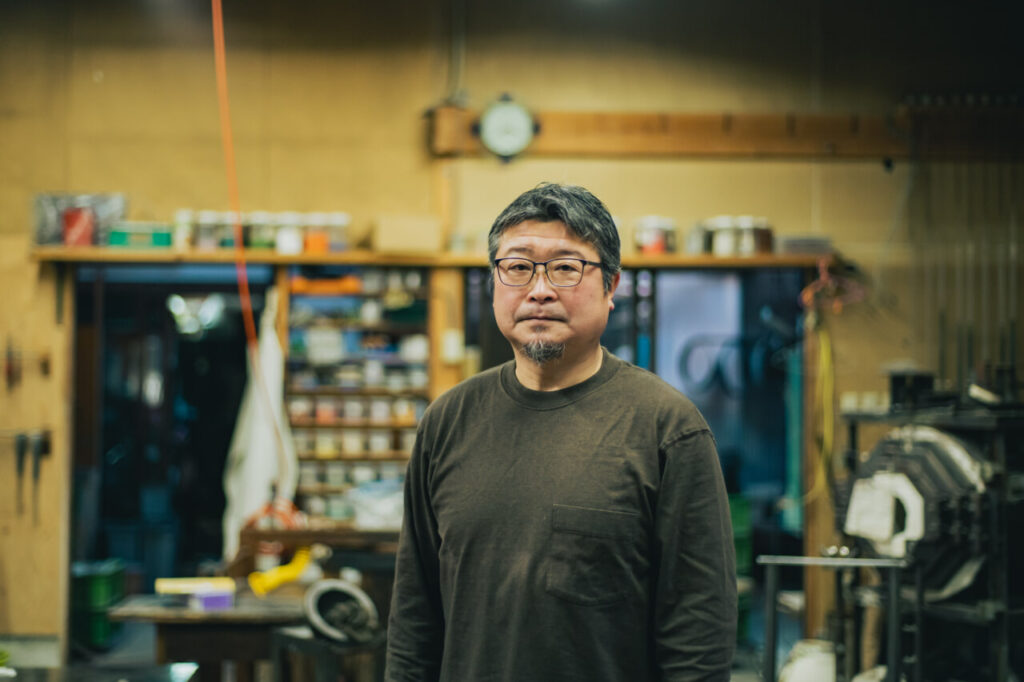
Mr. Teranishi has always loved making things. Since he was a high school student, he has tried his hand at making various kinds of things, including pottery. Among them, glass was the one that interested him the most. The more he learned about the process of making glass, the more interesting it became, and the more he learned, the more he wanted to pursue this career.
Mr. Teranishi learned glass-making techniques by assisting glass artists in their studios. He chose a glass manufacturing company in Yokohama, Kanagawa Prefecture, as his place of employment. He was so absorbed in glass that it was a natural progression for him to leave his job, return to his hometown, and set up his own studio. More than 20 years after opening the kiln, he says with a laugh, “I still feel the same way I did then, and I find myself continuing to make glass without stopping. He says with a laugh.
Unnojuku, where Teranishi’s studio is located, once prospered as a post town on the Kitakuni Highway, and even today, the landscape is an important preservation area for groups of traditional buildings, with water running through the center of the road and beautiful houses lined up on both sides with lattice doors.
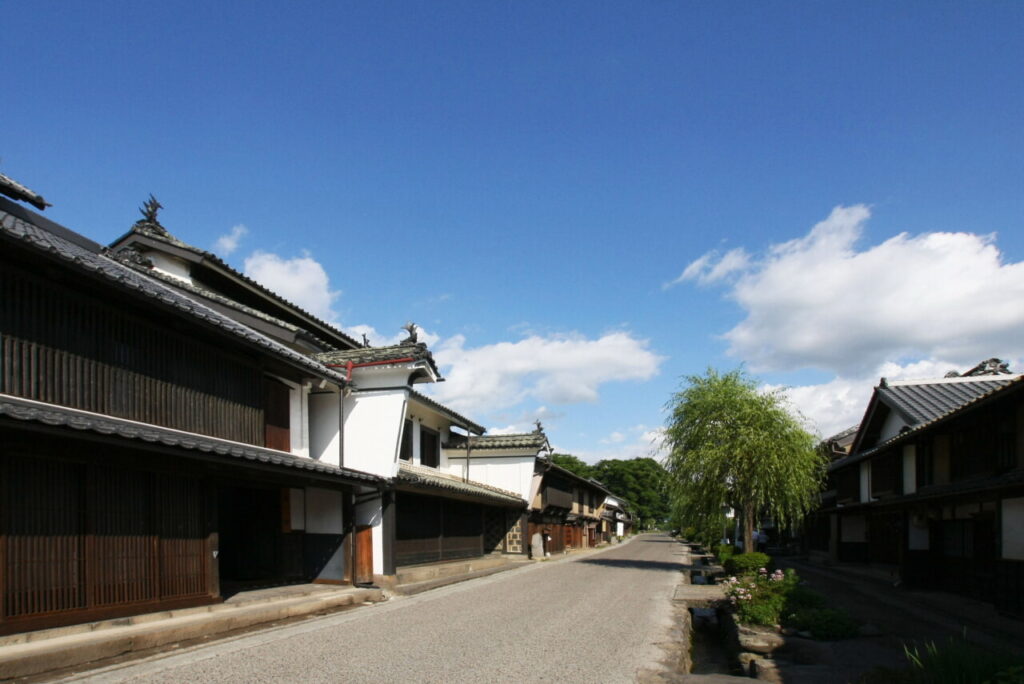
Orange is a renovated workshop in a row-house gate that blends in with this atmospheric scenery. A gallery and café have been added so that visitors can pick up the products and even purchase them here. The warmth of the shop name comes from the color of the flames inside the kiln where the glass is heated, and is also meant to symbolize the hope that the glass will continue to be used for generations to come.
Walnut glass is a pale, beautiful natural color
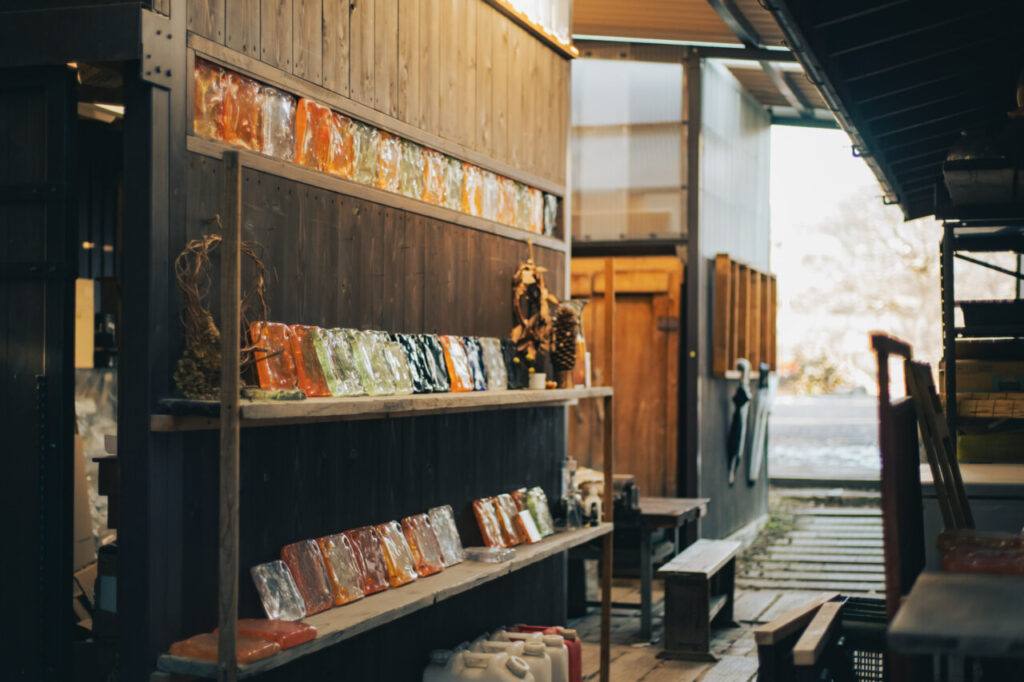
As mentioned above, Walnut Glass®, made from walnuts, a local specialty, is a registered trademark of this studio. By mixing the ashes of burned walnut shells with sand, the raw material for the glass, a unique light greenish color is produced. The greenish color is not too strong, but rather a gentle hue, a color that can only be expressed by natural materials.
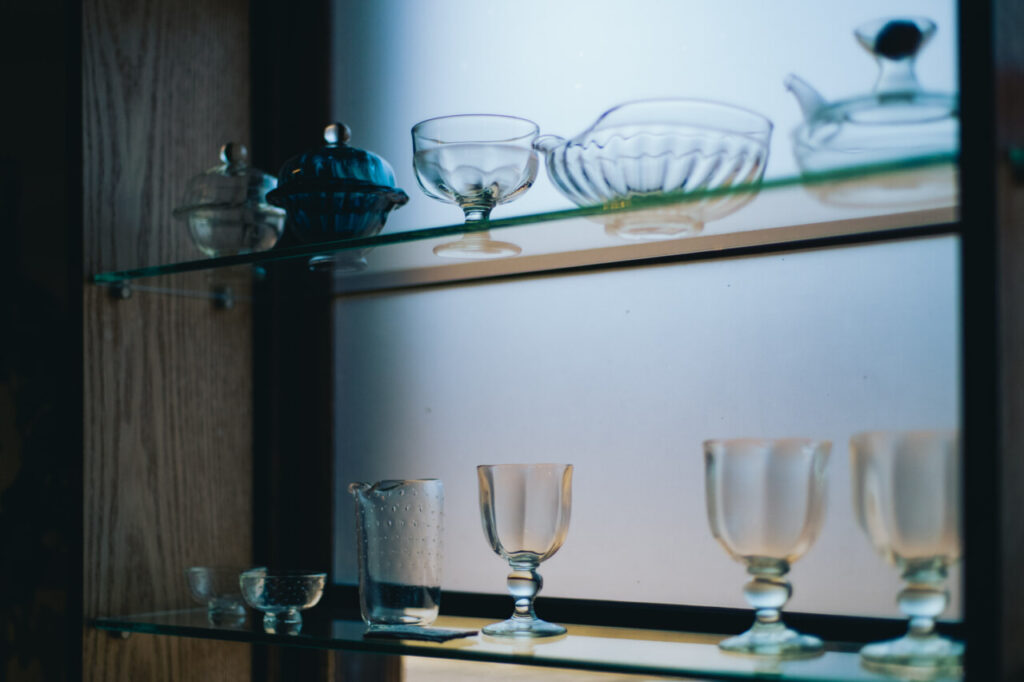
However, walnut glass cannot be mass-produced due to its limited materials, and only a small percentage of the glass products made at the studio are produced. In order to run a glass studio, one must not only produce tableware such as vessels and glasses, but also zodiac signs, glasswork, and other products that meet the wishes of the customers to whom they deliver.
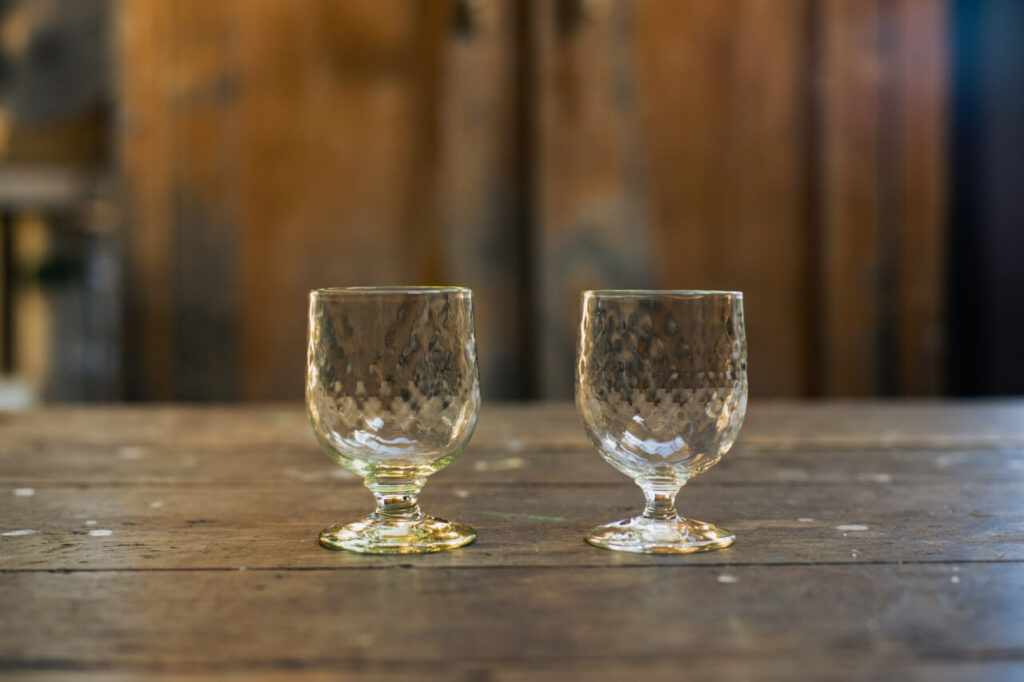
Of course, he has his own ideal style from his long career as a craftsman, but his motto is to create the most suitable form for the scene of use, from delicate and sharp to chunky and warm, and even ornaments intended to be displayed, and within that category, he adds his “character I will add “character” within that category. If I could, I would make only walnut glass, transparent glass, and tableware. We are like a manufacturer, so we make whatever our clients want. Teranishi says. A handmade order process chart using a calendar hung in the workshop was filled with the status of orders.
Updates that continue even after nearly 20 years
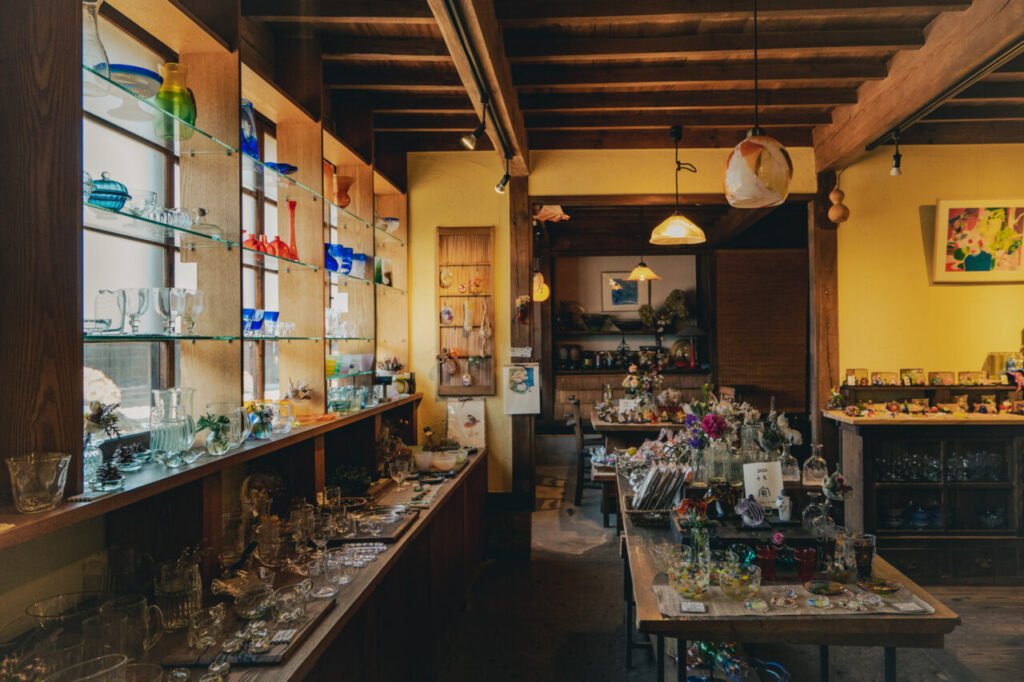
Teranishi’s workshop is also home to a gallery, so everything from production to purchase is done under his own watchful eye. This allows him to listen to the reactions of buyers, see how they react to his products, and use the discoveries to update and improve his products. In addition, over the years, we have gained a better understanding of production. In particular, if the size is wrong, it takes a lot of time and effort to correct it, so it can be said that setup is vital in glass production. Gradually, he became able to think logically about the process. The accumulation of such efforts has raised the technical system, and now adjustments through secondary processing are almost no longer necessary.
From “Interesting” to “Rewarding” and “Life’s Purpose
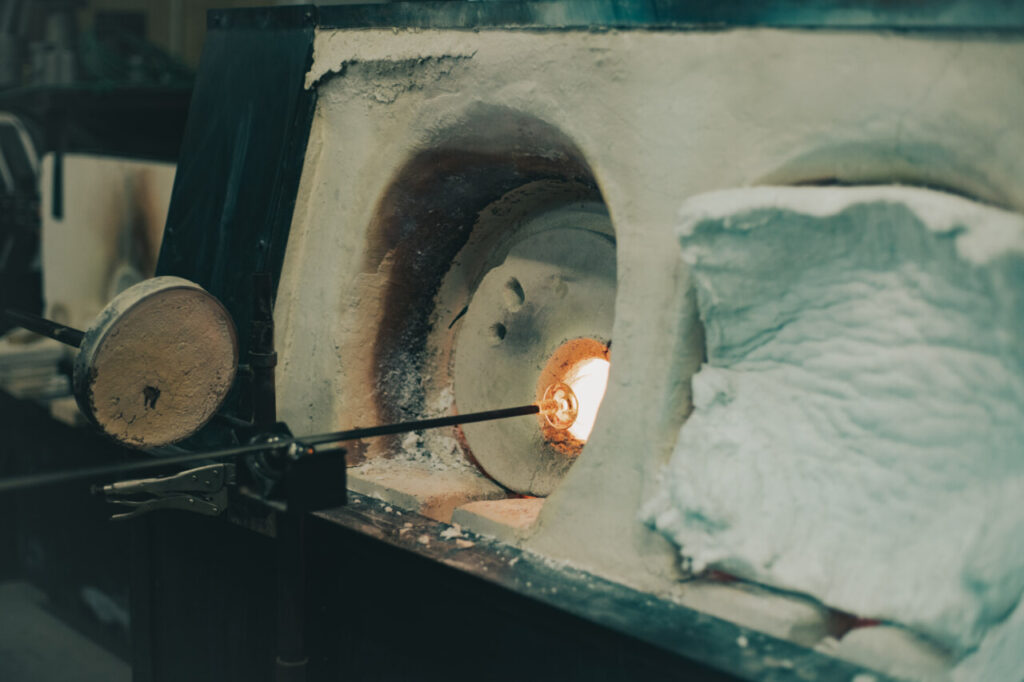
Incidentally, Mr. Teranishi’s studio mainly makes glass using the air-blown method. Although he does use some casting techniques, such as stretching heated glass, he basically uses the air-blown method. The reason why Mr. Teranishi insists on air-blowing is purely because it is an interesting process. The dynamism of the work, which is completed in a matter of seconds, and the satisfaction he gets from each step of the process, make it the perfect style for him.
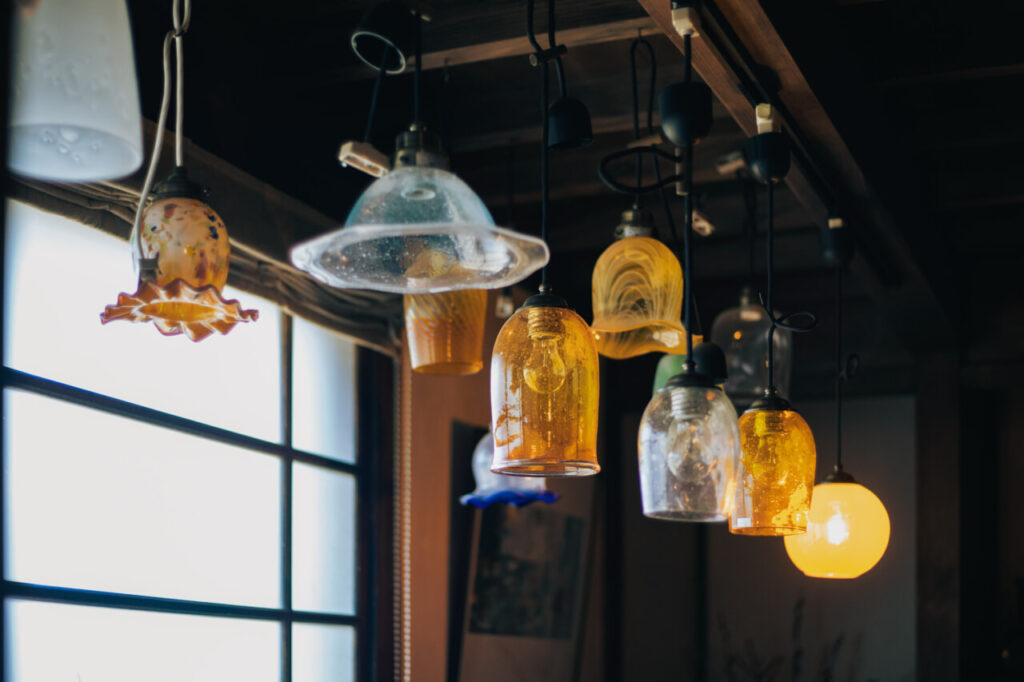
It has been about 20 years since he set up his workshop, but he says that even so, he has never made exactly the same piece of work. That is the beauty of handmade work, and sometimes he is able to create something that is far beyond his imagination and that he is proud of, which makes it worthwhile and makes him want to keep doing it. For Mr. Teranishi, this job has become a way of life. As the name of the company suggests, he is working hard every day to ensure that the workshop will continue to exist for generations to come.