When you hear the word “wooden bucket,” you probably think of a round shape, such as an Ohitsu or a Sushi bucket. However, the wooden buckets produced by Shuji Nakagawa, the third generation owner of Nakagawa Wooden Crafts, are quite different. What is the background behind the fusion of traditional Japanese craftsmanship and artistry, including his signature work, the champagne cooler?
Champagne cooler that transcends “structural limits” created in a workshop near Lake Biwa
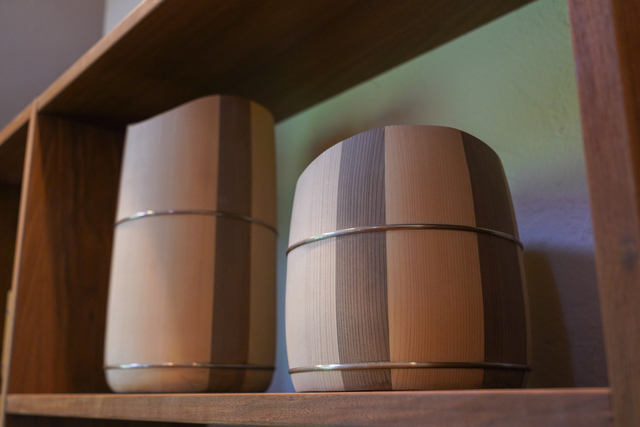
Lake Biwa is nearby, and the Hira mountain range runs along the western shore of Lake Biwa. The Hira Mountains, which run along the western shore of Lake Biwa, and the “Nakagawa Wood Crafts Hira Workshop Kusaniwa ” is located in Hira, Shiga Prefecture, surrounded by the nature of the area.
The first thing Shuji Nakagawa showed us at the workshop was the champagne cooler ” konoha.
Rare woods such as Koya Maki and Bishu Hinoki, which are more than 200 years old, are used to make this cooler, which has a beautiful white wood appearance. They are also said to be suitable for storing ice because they are water-resistant, suitable for keeping cool, and resistant to condensation. It is also lightweight and easy to carry, making it very practical.
The most eye-catching feature is its streamlined form, which is pointed at both ends. It is a form that fits easily in Japanese-style spaces, on tables, or in outdoor settings such as glamping. It looks cool not only with champagne, but also with wine or sake.
So, how did Mr. Nakagawa, a wooden bucket craftsman, come up with the idea of creating this champagne cooler?
Sharper. Repeated requests
It was 2010. Mr. Masatoshi Imai, president of the Kyoto-based planning company “Link Up,” asked Mr. Nakagawa to create an unprecedented wooden bucket that could be sold overseas.
The idea was not to make a champagne cooler from the start, but rather to create a “wine cooler” as he searched for a way to use wooden vats that would be suitable for overseas markets. Mr. Nakagawa proposed a small-sized wine cooler, but did not receive a GO signal.
In fact, Nakata had seen this prototype tub. Nakada, who had lived abroad for a long time, requested “a sharper design. If the design remained the same as the conventional tub, it would stand out in a foreign living space. If we could create something that fits European lifestyles by using the technology of making tubs, it would bring new possibilities to traditional Japanese craftsmanship. This was the idea behind the project.
The prototype took two years to complete. Convinced of further evolution after overcoming obstacles
However, it was extremely difficult to achieve this “sharp design.
Wooden vats are made by cutting hegi-ita, which is made by splitting raw wood along the fibers of the tree, and then shaving it using a knife called a “sen,” as well as 300 different types of knives, and tightening it with a metal ring called a “taga. The wooden buckets with pointed ends were so damaged that the tag bit into the curved part of the wooden bucket.
The prototypes were made over 10 times, and two years had passed between them. He says that the thought of ” structural limitations ” crossed his mind, but in his groping in the dark, he came up with the idea of rounding off the part where the tag enters and warping the topmost part to make it sharp and pointed. This was the key to the breakthrough. The konoha was finally completed and caught the eye of a major champagne maker, which led to its international debut as a champagne cooler. That was more than 10 years ago, and it is still a popular product with a string of orders from Japan and abroad.
Nakagawa’s discovery through the production of konoha was that the technology of the tub is still evolving.
At the beginning of his life as a craftsman, he did not see the “world.
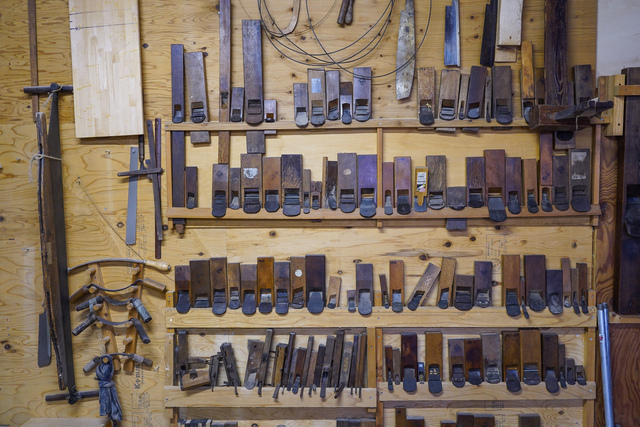
Mr. Nakagawa is the third generation of Nakagawa Wood Crafts. He was born and raised in the workshop that his grandfather , Kameichi Nakagawa, established on Shirakawa Street in Kyoto City. The workshop is now called “Nakagawa Wood Crafts Kyoto Workshop” and is run by Kiyotsugu Nakagawa’s father, the second generation.
After graduating from university, Mr. Nakagawa studied under Mr. Kiyotsugu. Mr. Nakagawa studied under Mr. Kiyotsugu after graduating from university, and his wooden buckets, called “the best bucket craftsmen in Kyoto,” were used by long-established restaurants and ryokans. At the same time, Mr. Seiji was also energetic in the production of craft works, and established the ” masa-matching ” technique, in which the wood is perfectly aligned by taking advantage of its characteristic grain expansion and contraction. In recognition of these efforts, Seiji was designated a Living National Treasure in 2001.
Two years later, Mr. Nakagawa left Kyoto. He was engaged as a craftsman in Mr. Seiji’s workshop, but he chose to start his own business, believing that he could not avoid having his works recognized in the world under the name of Seiji Nakagawa if he created them in his father’s workshop, which had become a living national treasure. He then set up “Nakagawa Wood Crafts Hira Studio” in the Hira region of Shiga Prefecture, a place rich in nature that he had been visiting for mountain climbing since his college days. When he first started out on his own, he made traditional products such as ohitsu (rice casserole dish) and sushi tubs, just as he had done during his apprenticeship.
The world of tubs had shrunk.
At that time, Mr. Nakagawa saw that “the world of Oke was shrinking rapidly.
In the past, tub makers made all kinds of daily utensils, from cradles to rice pails, sushi tubs, bathtubs, hand tubs, and even coffins. However, as lifestyles changed, the number of tubs sold declined, and by the time Mr. Nakagawa became independent, there were only 3 tub makers left in Kyoto, compared to the 250 or so that existed under his grandfather Kameichi.
When I started my own business, I thought it would be enough to support my family with a small workshop,” he said.
Accepting Change and Expanding Sales Channels
However, it was the creation of the aforementioned champagne cooler “konoha” that brought about a turning point for Mr. Nakagawa.
When I was making tubs with only “Japan” in mind, I thought there was no way to change the 700-year-old tub making method, and I did not feel the need to do so. However, when they succeeded in boldly changing the shape of the wooden tubs, there was room for design, and sales channels expanded to the world. Mr. Nakagawa recalls.
He is now working with craftspeople in tune with the times and culture, embracing change and creating products that people of that era will want to use. He believes that this is the key to opening up the possibilities of craftsmanship and preserving traditional techniques.
Evolving into the “wooden buckets” that amaze the world
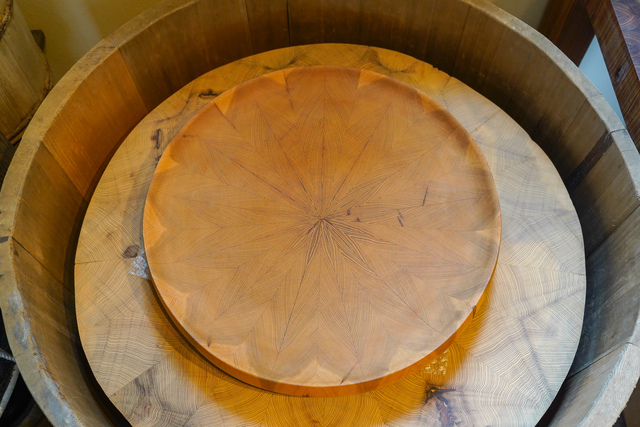
Today, Mr. Nakagawa’s creativity continues to evolve and is highly acclaimed both in Japan and abroad.
Superb technique of matching 30 boards with the grain of the wood
The Loewe Craft Prize was sponsored by the Loewe Foundation of Loewe, a long-established Spanish brand famous for its leather goods, and Loewe’s creative director, Jonathan Anderson. This groundbreaking prize was launched in 2017 based on the recognition that crafts occupy an important place in contemporary art. In this memorable first edition, Nakagawa’s entry ” Big Trays of parquetry ” was selected as one of the 26 finalists out of more than 3,900 entries from 75 countries.
At first glance, the round tray in the exhibit does not appear to have any joints, but it is made of 30 boards cut, milled, and assembled from Japanese cedar. This is the moment when the ” masa-joining” technique inherited from his father, Seiji, was recognized around the world.
KI-OKE” in the collections of museums in London and Paris
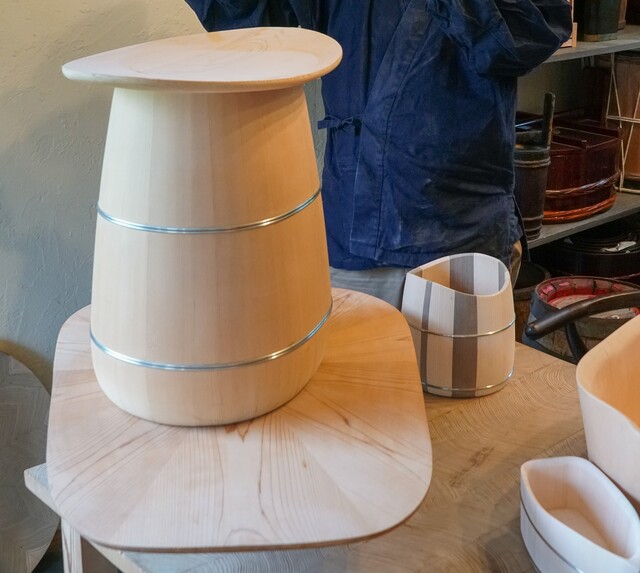
The ” KI-OKE Stool,” created by Mr. Nakagawa in collaboration with a Danish designer, was selected for the permanent collections of the Victoria & Albert Museum (V& A) in London in 2015 and the Musée des Arts Decoratifs in Paris in 2016. Both are prestigious world-class museums specializing in decoration and design.
In the past, it was difficult to bring wooden vats to Europe. This was because the drying air caused the wooden panels to shrink, and the gaskets were dislodged. Now, however, technology has been established to adjust the moisture content of the wood according to the humidity of the land where the vats are brought, allowing Japanese “KI-OKE” to spread its wings around the world.
Opening New Doors
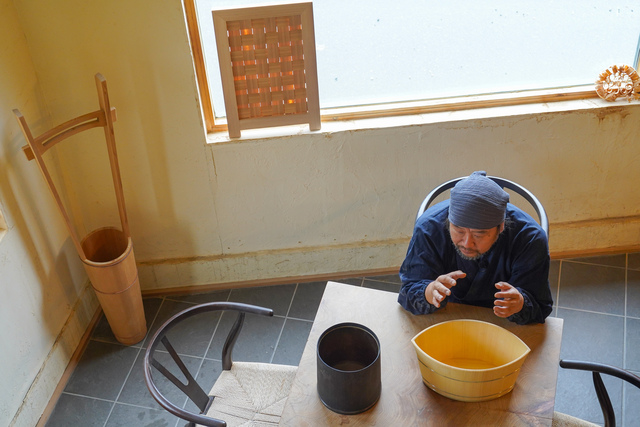
In the two-story workshop, young craftsmen are busily at work.
Mr. Nakagawa used to think that he could support his family, but now he focuses on training his craftsmen. While passing on the techniques of wooden bucket making, he is also incorporating the ideas of young craftsmen in the production of his new brand, ” Shiki, ” which will be launched in 2020.
As the name suggests, “Shiki” is a brand of tableware made of wood from Shiga Prefecture. By creating everyday items such as cups and plates for young people, we hope that they will develop a sense of design that fits the lifestyle of the times. It is with this in mind that he watches over his apprentices.
The next step is to shine a light on the craftsmen.
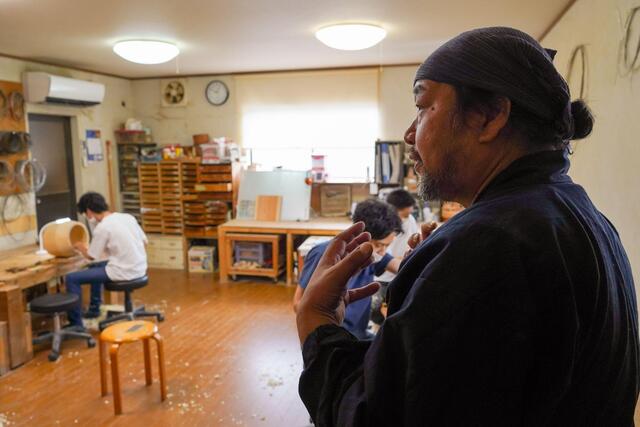
Nakagawa is involved in collaborations with craftspeople from other fields and industries, but he would like to shine a light on Japanese craftspeople in the future. This is because, after traveling abroad, he realized that there are many artisans in Japan who have not yet seen the light of day, but who have the potential to become world-class craftspeople.
When traditional techniques and design are fused together, craftspeople can spread their wings to the world. He wants to create opportunities for those involved in crafts to have the same experience that opened his own eyes in the past.
He believes that this will expand the possibilities of Japanese crafts and pass the baton to the next generation of craftspeople.