Takato Town, Ina City, Nagano Prefecture, overlooking the ruins of Takato Castle, one of the three most famous cherry blossom viewing spots in Japan. In this small town, there is a craftsman who makes frying pans that attract many customers from all over Japan. He is Takashi Kawarazaki, who moved from his birthplace in Tokyo to Takato Town and set up his own workshop.
Work that confronts oneself
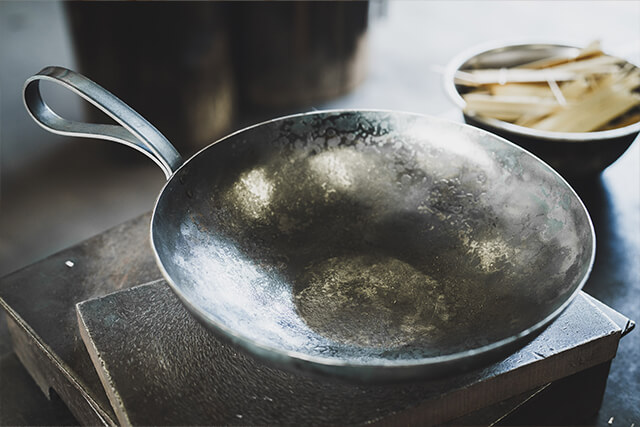
Mr. Kawarazaki’s motivation for becoming a blacksmith was simple. While working at a department store in Tokyo, he grew tired of the crowds in the city and of dealing with customers at work. Then, why not do manufacturing?” He then visited various craft studios. He then toured various craft studios and pondered what he wanted to do. As a result, Mr. Kawarazaki became interested in forging, which involves striking heated iron to create products. After finding what he wanted to do, he quit his job at the age of 35 with his “can-do” spirit. He moved to Nagano Prefecture to attend a technical college, and after graduation studied under a blacksmith in Tomi City, Nagano Prefecture.
Not a work of art, but a tool for daily life.
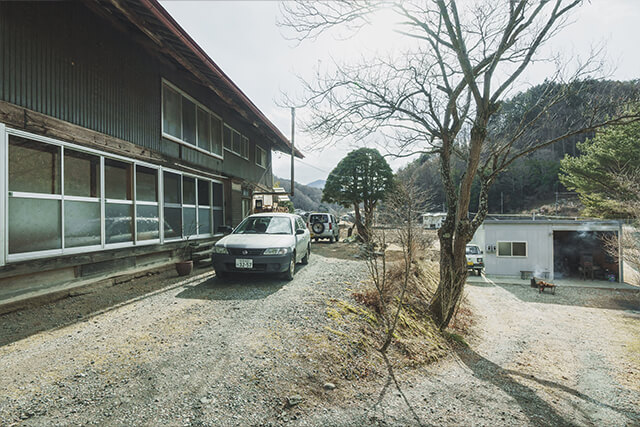
In 2002, he opened his own workshop in Takato-machi, Ina City. Of course, it was not all smooth sailing for him immediately after he opened his workshop. There were times when he could hardly call it work. However, he thought, “Let’s keep going until I reach 40 years of age, and then we can see what happens next. As mentioned above, Mr. Kawarazaki himself did not set out to become a blacksmith for any great reason, and he does not think of what he makes as a work of art, but rather as a tool for daily life. That is why he thinks that his work is more like a tool for daily life, rather than a work of art. If it doesn’t meet the needs of the world, I will update it to meet them. If it doesn’t meet the needs of the world, let’s update it to meet the needs of the world. This attitude had a great influence on his encounter with the famous ceramic artist Noriyuki Yamamoto, who has published books and photo collections, which led to the introduction of Mr. Kawarazaki’s works to the world. When he first greeted Kawarazaki with the words, “I will make anything out of iron if you ask me to. Yamamoto was amused by this and exhibited his work in his studio, giving me the opportunity to see it. This attitude of listening to the voice of the consumer and applying it to manufacturing, like that of a manufacturer, has gained widespread sympathy.
Time and effort are what craftsmen’s handiwork should be about
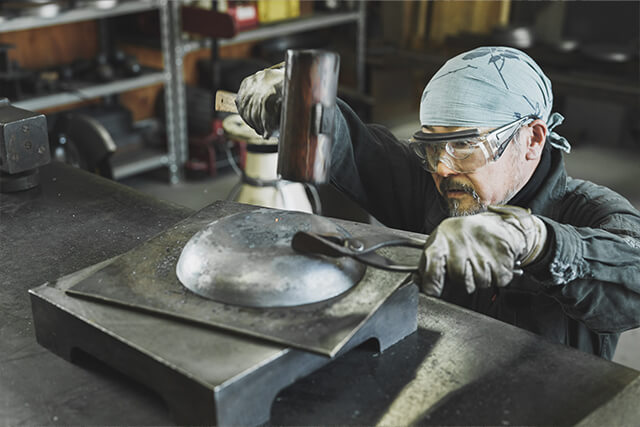
That said, Mr. Kawarazaki’s works cannot be mass-produced like industrial products sold in mass merchandising stores. Unlike cold forging used in metal product factories, Kawarazaki’s works are made using hot forging, in which the metal is heated one by one. Although it is not suitable for mass production because of the time and labor required, it can be formed into complex shapes, and can be finished to the shape that is envisioned. Of course, he does not have a fixed concept of what his work should look like. However, he believes that this is the proper handiwork of a craftsman, and he has always been dedicated to it, no matter what time of day it is.
A wok I made by chance opens up new possibilities
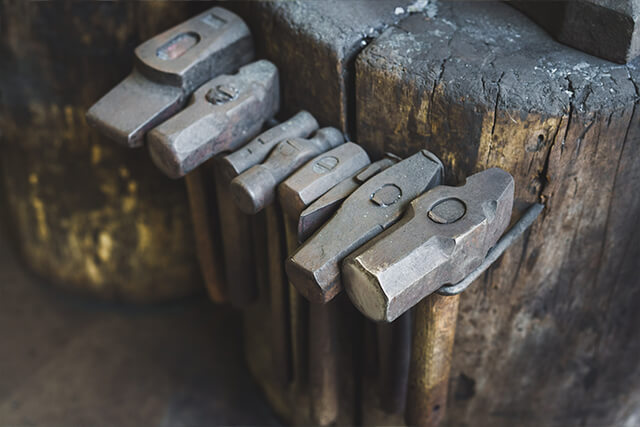
Listening to consumers and careful craftsmanship are two ideas that coexist. The coexistence of these two ideas is one of Mr. Kawarazaki’s strengths. The story of the birth of the first hit “wok” is a perfect example of this. One day, his wife asked for a wok, and Mr. Kawarazaki went to a department store to look for one, but after walking around for a long time, he could not find the ideal one. Then, he decided to make a wok, so he listened to his wife’s request and produced it. The result is a handmade product that is lightweight, conducts heat well, and can be wielded by people of any height without discomfort. The wife’s reaction to the product was positive. This led to the sale of the product as an actual product, which received an unexpectedly strong response. The spirit of making everything from Japanese nails to staircases, as long as there is a request, is expanding the scope of his work and creating the possibility of further hit products.
The Value of “Takashi Kawarazaki’s Frying Pan
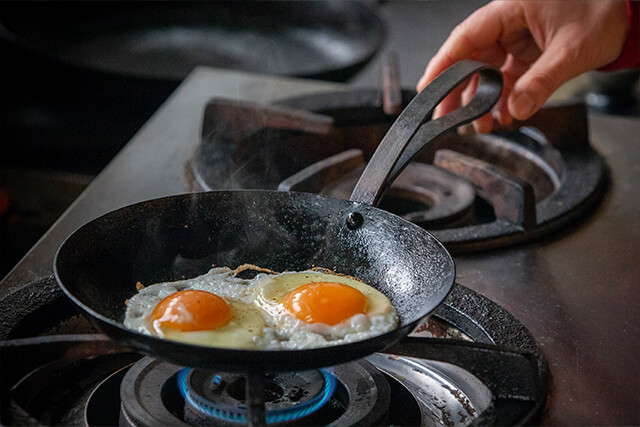
The result is a frying pan that is now hard to find. Like the wok, the frying pan was created in response to consumer feedback, but since it was first sold to a well-known lifestyle store in Tokyo, it has quickly gained popularity due to its functionality and warm texture, which is only possible with hand-forged products. Furthermore, the use of the product in a video distributed by a popular camping-related YouTube star led to the acquisition of users such as young people and men, who were not previously the purchasing base for the product. Demand for the product has grown even more, and now customers wait more than a year from the time of order to the time they receive the product.
The Arrival Point and the Road Ahead
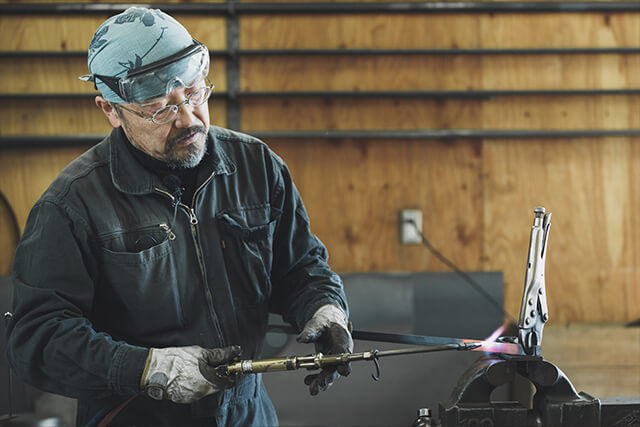
Even today, when the company is attracting a large number of customers from all over Japan, what it does remains exactly the same as when it first opened its workshop. He heats an iron plate as he always does, and then he forms it by pounding it with a wooden mallet as he always does. The only thing that has changed a little is that he now has eyes. Because you can’t take measurements during the forging process, when I started as a craftsman, it was difficult to make the same thing all the same size, even if I was making the same thing in the same process.
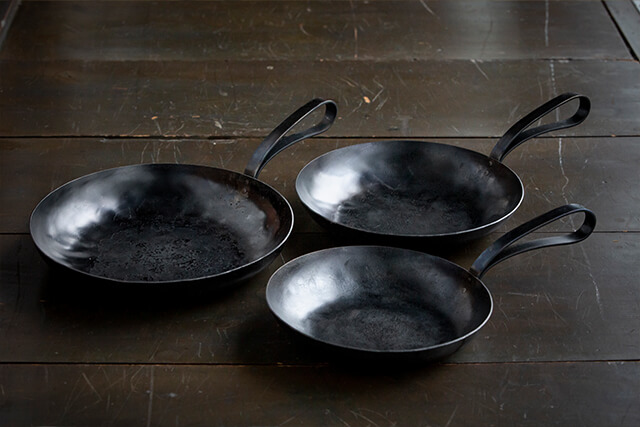
However, as I made more and more pieces, I began to be able to make the same shape without having to think about it. And now that he can sell as many as he makes, he feels that he has reached the point where he can produce as many as he can. I am producing as much as I can, so I can’t make any more. Therefore, it is impossible to increase his income any further, and he does not want to do so much more. I want to continue the same blacksmithing business I started because I love it, even 10 years from now. With this wish, Mr. Kawarazaki continues to hammer iron today.