Tobo-kamahachi is located in a mountain forest at the foot of Mount Kaikomagatake, the northernmost peak of the Southern Alps. Mutsumi Ohashi, a potter, kneads clay, chops wood, and fires a traditional “makigama” (firewood kiln) to create his works. What is the charm of pottery that changes its appearance and texture by “firing”?
Anagama,” a kiln that has been handed down from generation to generation
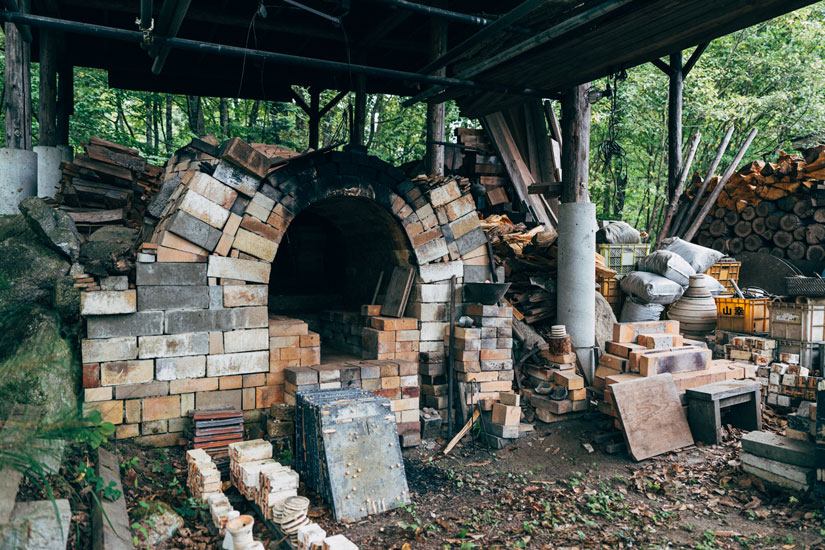
In Mukawa-cho, Hokuto City, Yamanashi Prefecture, surrounded by nature with a view of the Southern Alps, red pine trees used for wood-fired kilns grow in abundance. Mr. Ohashi, a potter, uses a type of wood-fired kiln called anagama. The anagama has a single chamber for firing pottery, whereas the noborigama has multiple chambers that gradually rise in height. Anagama kilns have a longer history than climbing kilns, which were developed for more efficient mass production. Today, gas kilns and electric kilns, which are superior in terms of operation and temperature control, are widely used, but Mr. Ohashi was attracted to anagama because of the “firewood.
The Unexpected World of Ceramic Art
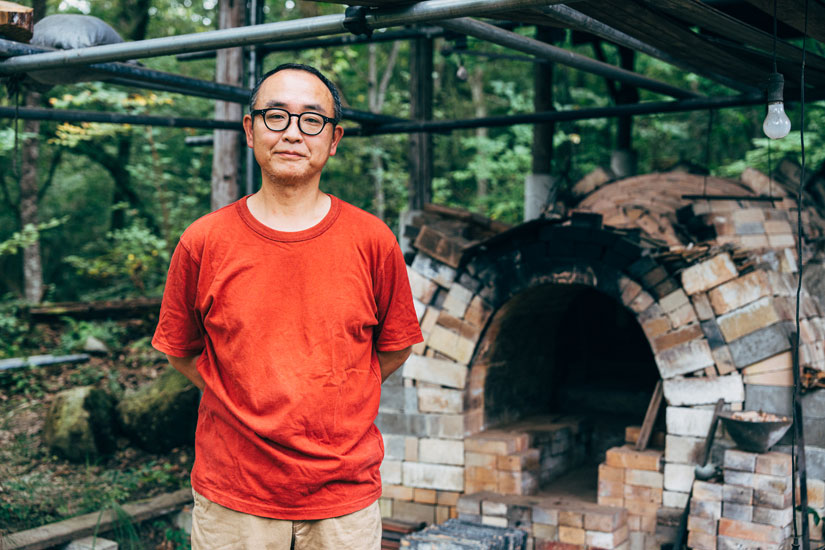
After moving from Sendai to Tokyo to attend university, Mr. Ohashi joined a club called the “Yakimono Ceramic Art Society. He says, “I was never interested in ceramics,” but his image of ceramics was overturned when he visited a ceramic artist working near the university. Although it was an artistic activity, the majority of the work was actually physical labor, such as chopping wood and chopping firewood with an axe. As he helped with the work himself, he recalls, “The simplicity of the work became interesting. Before he had the desire to create works of art, he decided that he wanted to chop wood and build a wood-fired kiln, which led him to begin pottery making in earnest.
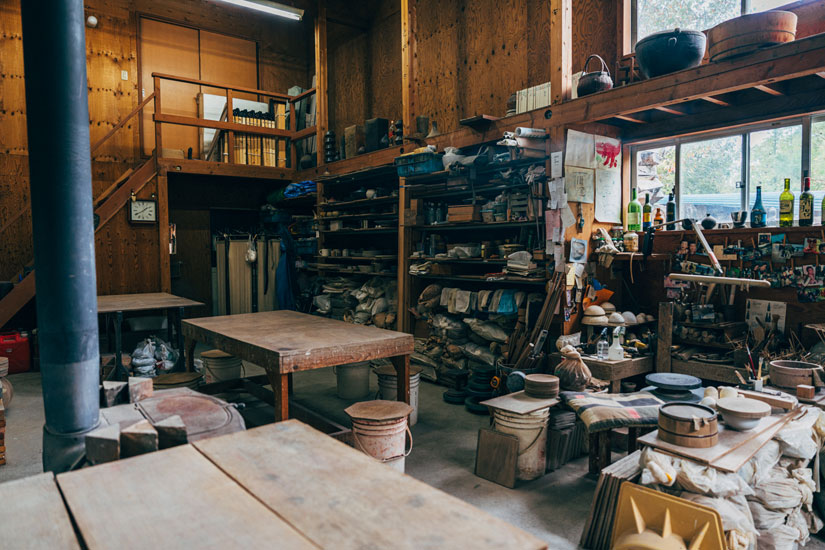
Charm of the Anagama Kiln Facing the Flame
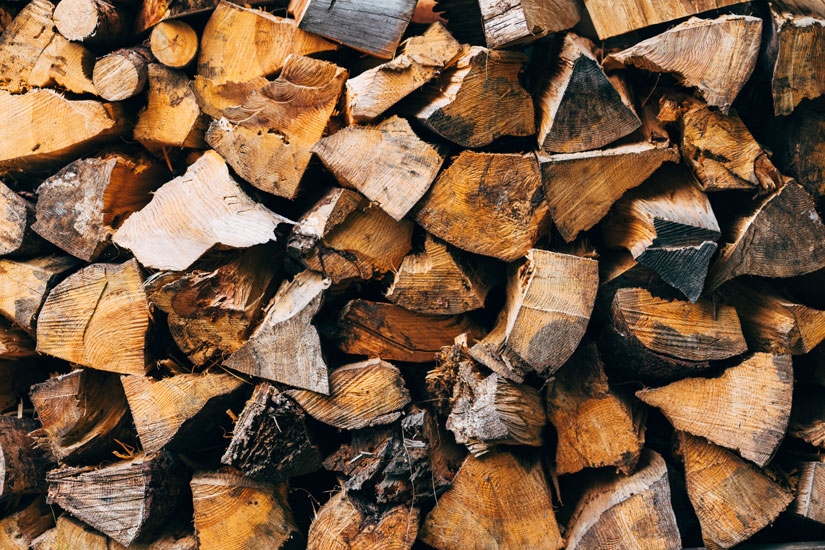
It takes about four days to fire the anagama kiln. During this time, he and his wife, whom he met at a pottery-making workshop at the university, take naps at their home adjacent to the kiln and work together. In a typical wood-fired kiln, the temperature is raised from 1,230 to 1,280 degrees Celsius, but Mr. Ohashi keeps the temperature at about 1,180 degrees Celsius. Mr. Ohashi’s clay cannot withstand higher temperatures and will melt or break. Compared to climbing kilns, which use heat more efficiently, anagama kilns are said to be more difficult to control temperatures, but Mr. Ohashi says, “I can get a more realistic idea of the chemistry of the clay. In the anagama kiln, ashes fly off and adhere to the vessels, melting together and giving them a rugged, rock-like texture. The individuality of each vessel is also affected by the way the wood is packed and arranged.
The inability to uniformly adjust the temperature and flame makes for an interesting and unpredictable expression. Every time I burn the wood, I have new questions and ideas about what to do next,” he says.
The expression of pottery produced by anagama kilns
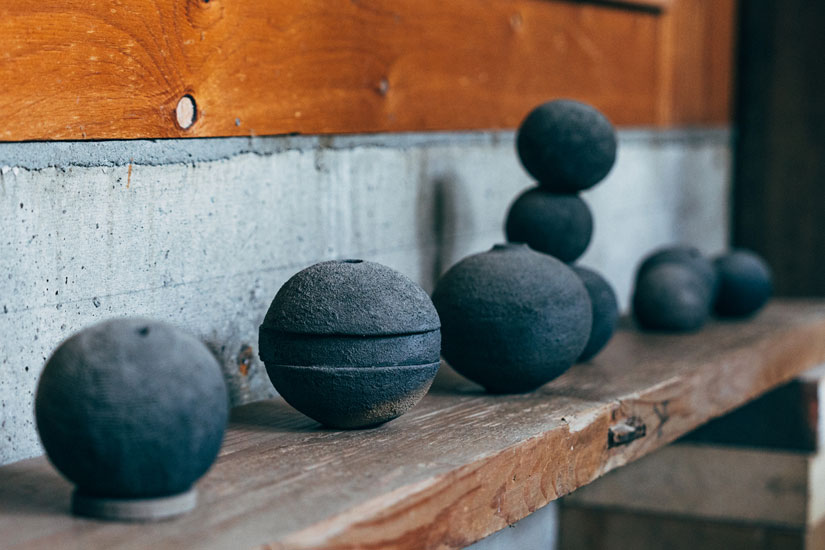
Ohashi’s works fired in the anagama kiln include tableware, sake cups, vases for single flowers, and many other items. Ohashi’s creations, which are “easy to use in daily life rather than highly artistic,” are increasingly being sold at restaurants in Hokuto City, and are gradually gaining recognition through word of mouth among chefs and customers. His works are sold to the general public through galleries and online stores, and recently, inquiries from social networking sites have been increasing.
Most ceramic works are glazed with “yuyaku,” a glaze that gives the surface a glassy sheen, but Ohashi’s signature technique, yakishime, does not use glaze in order to bring out the natural color and texture of the clay. In contrast, some pieces use “ash glaze,” a glaze made by refining the ash produced during the yakishime process, which produces unique colors ranging from brown to gray, depending on the state of the naturally occurring ash. The fun part is that the clay changes its texture to look like stone or rock during the firing process.
Introduction of kerosene kilns
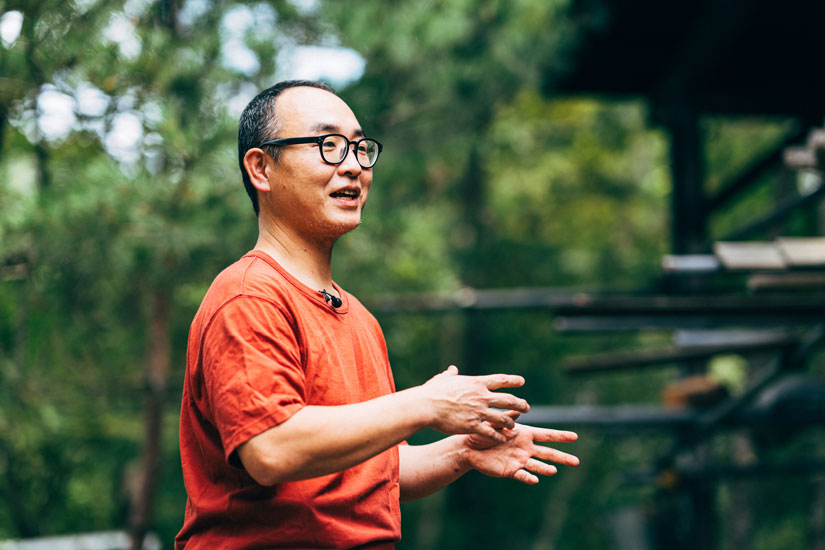
In addition to the anagama kiln, which is fired two or three times a year, a new “kerosene kiln” was introduced around 2022. He says that he decided to try a kerosene kiln, which he had never experienced before, while his exhibitions were not going as well as he had hoped due to the new Corona. Ohashi’s quest, which until then had been based on his repeated inventive attempts to change clay and firing methods in a wood-fired kiln, entered a new phase with the change of kilns.
Compared to gas or electric kilns, kerosene kilns are said to be inferior in terms of firing uniformity. To take advantage of this point, he has devised a kiln that is arranged in the same way as an anagama, so that the finished product is unevenly distributed depending on the temperature difference and the way the flame flows. Because the charcoal does not explode, the kerosene kiln, unlike the anagama kiln, produces a matte finish. The differences that show up in each kiln give each piece its own character,” he says. Ohashi, who tried using a kerosene kiln by hand, says that he realized once again the difference in the finished product that results from changing kilns.
Continue to discover new
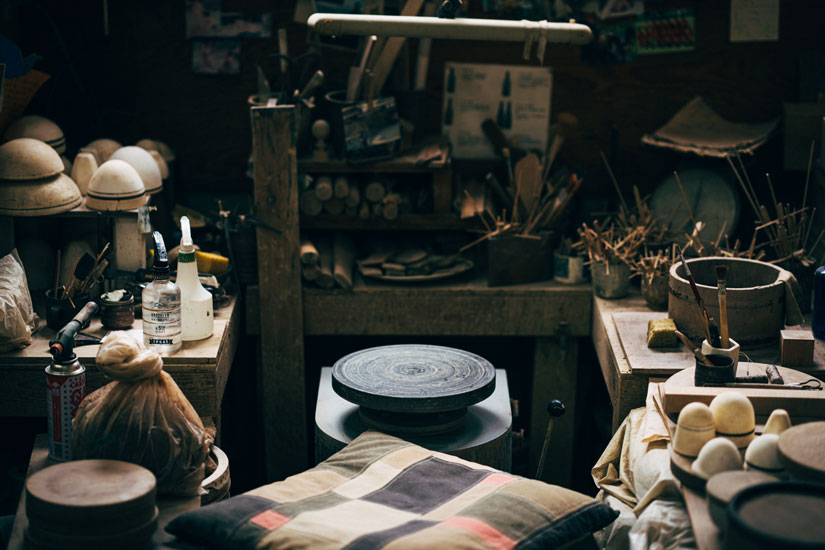
When I am immersed in the production process, my vision inevitably narrows, and the distribution of clay and the contours of the work tend to be more to my liking,” he says. In such cases, he refers to the reactions of customers when they see his work. He says that the feedback, which comes from a different perspective than that of the creator, encourages him to broaden the scope of his work. Through regularly exhibiting at craft fairs that attract many visitors, such as the “Daigahara Shukuichi” held in Hokuto City’s Hakushu Town, he has come to be able to discern what sells and what doesn’t. “I have been a potter for more than 20 years, but I have never been able to sell my work. Even after more than 20 years as a potter, he says, “I try not to limit my tastes too much and make different discoveries. I listen to customers’ feedback and make use of it. Repeating such a process is what makes it worthwhile,” says Ohashi.
Make a vessel “the way you want it”.
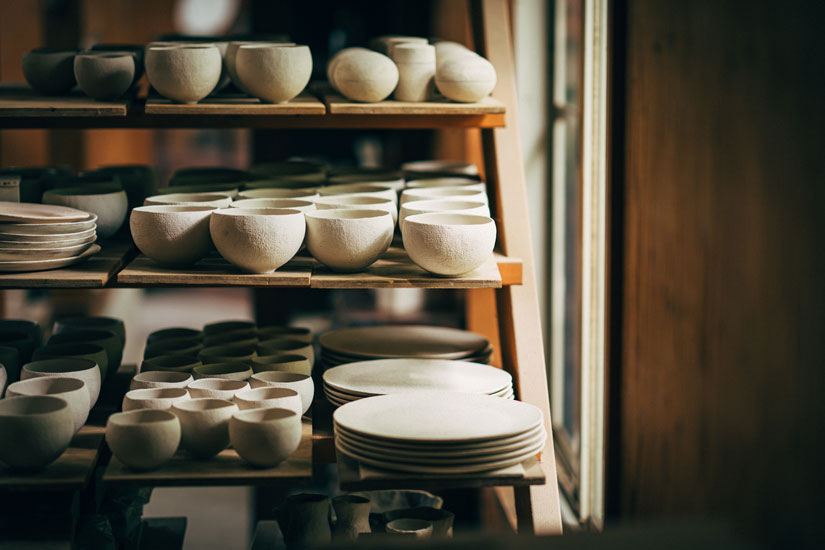
Mr. Ohashi says that the more he continues to create, the more questions arise from all perspectives. Currently, he focuses on “clay” and “firing. He says, “Even if you use the same clay, depending on how you fire it, the original flavor of the clay and the color of the firing will change. That is what I want to pursue. While Yamanashi Prefecture is rich in firewood resources, not much clay is mined there.
Continuous trial and error, and beyond
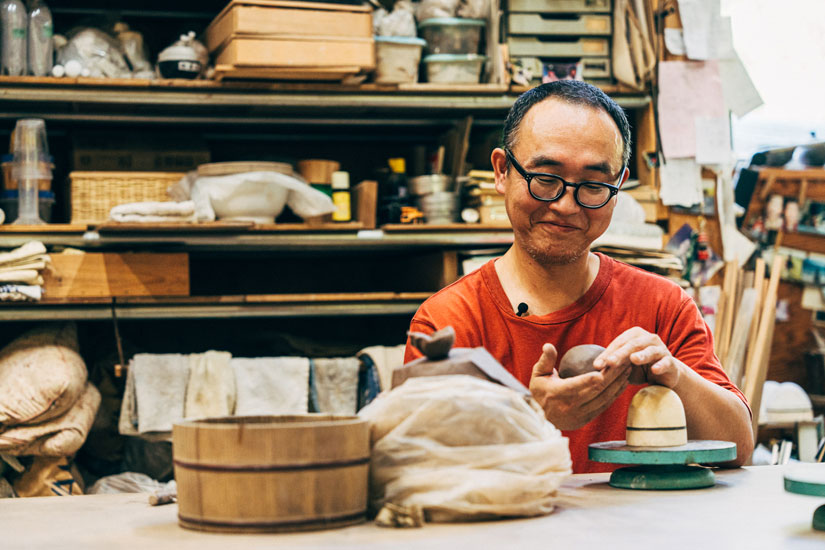
If I had to face all the questions that arise one after another, it would probably take me 10 or 20 years,” smiles Ohashi. While he is passionate about anagama, he is always thinking about the possibilities of expression in pottery.
Clay becomes harder and tighter when it is fired, and is reborn in a different form,” he says. Rather than wanting to tell someone about the process, I want to know about it myself.
The expression of pottery changes depending on the kiln and firing method. We can’t take our eyes off of Mr. Ohashi’s new creations, which are the result of his insatiable quest.