Conveying Boso uchiwa to the present
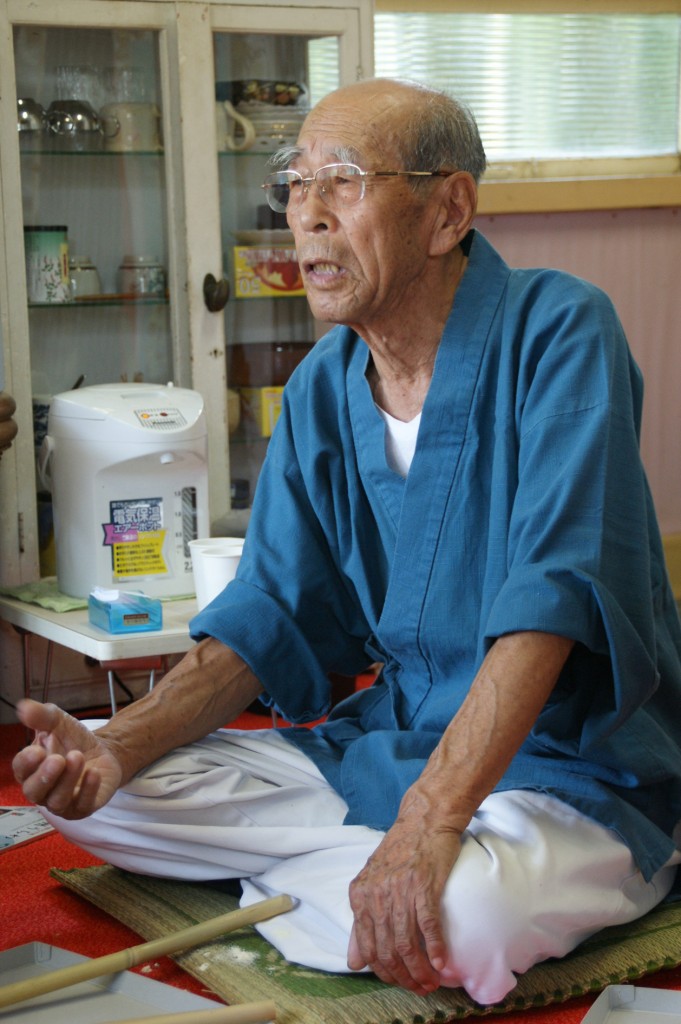
Marugame uchiwa of Kagawa, Kyo uchiwa of Kyoto, and Boshu uchiwa of Chiba. These are the ”Three Great Uchiwa” of Japan.
We visited the workshop of Masao Uyama, a traditional ”kogei” artist of Boshu uchiwa.
Seeing the many uchiwa in the workshop, Nakata asked a question.
”Are there differences in uchiwa depending on where they are made?”
”Marugame uchiwa has a flat handle. There are also only 8 processes. Boshu uchiwa has a round handle and involves 21 processes.”
”How about Kyo uchiwa?”
”With Kyo uchiwa, you align the frame and paste the paper, and the pattern is added later by inserting it in between.”
”So, each type has a different handle?”
The bamboo used for Boshu uchiwa is the native Simon bamboo, especially the Daimyo bamboo.
He tries to use straight bamboo which wasn’t affected by a lot of wind, but there has been a dramatic decrease in the number of craftsmen who can select or cut bamboo. Currently, Uyama is the only person who can do that.
There are currently only 20 to 30 craftsmen who can make uchiwa by hand.
And Uyama, who is over 80 years old, is the only craftsman who can do all of the processes himself.
The difficulty of splitting bamboo
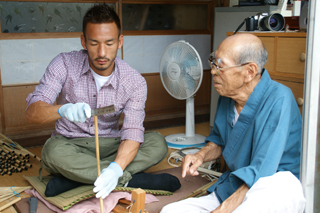
It is beautiful to watch Uyama make the uchiwa.
Leaving the handle, he splits the rest of the bamboo into 48 to 64 equal parts.
The split bamboo becomes the frame. These are woven with string, creating a beautiful lattice ”window”.
It seems like a simple task, but when you actually try it, it is very difficult.
A bamboo is split into 8, then 16, and then each piece is split into 4. Nakata was only able to split into 16 pieces.
In order to shred further, a blade is used to cut the 2 mm bamboo strip, and it is difficult to place the blade precisely in the center.
”When splitting the frame, some are thick and others thin. They aren’t even. The human eye sees differently on the right and left, so depending on which eye you use, the thickness turns out differently.” Nakata said.
”Your eyes become irritated. It looks easy, but it’s hard. Isn’t that true about everything?”
According to Uyama, it takes at least a year to be able to split the bamboo properly.
Once the bamboo is split, the frame is spread out into the shape of a fan, roasted over coal, then the fabric is applied.
The fabric is made of either washi or cloth. You can bring your own fabric to be used. When using cloth, cotton or silk is recommended.
The pleasant feel of handmade Boshu uchiwa

”After the ships were destroyed by the earthquake, a lot of their flags were collected. We couldn’t just throw them away, so we discussed ways for them to be used. It might be a good idea to make them into uchiwa.”
Taking a look at the uchiwa he completed, Nakata looked delighted and said ”Isn’t this beautiful?”
It takes much more time and effort to make the uchiwa than expected.
That definitely enhances our appreciation for these handmade items.