Leading Pottery of Akita
Naraoka-yaki dates back 150 years. With different theories emerging as more studies are conducted, the most dominant theory is that it was made by Soma potters under order from local noble, Kiyoharu Komatsu in 1863. It is the oldest pottery still remaining in Akita. It’s characteristic lies in its glazed blue color, which is rare in Japan. The clay of this region is in fact not adequate for pottery. Therefore, the clay had to be amended, as it was not as easy to get clay from other regions as it is today. Unfortunately, with the development of transportation networks, the pottery’s value plunged, resulting in the decrease of potters creating Naraoka-yaki. Naraoka Tosono is a company that preserves this old art form.
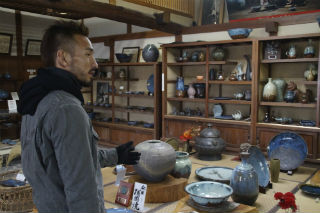
Observing the Lighting of a Potter’s Kiln for the First Time
Through our travels, we’ve had the opportunity to visit many potters, but not once had we observed the ”lighting” of the kiln using actual logs. We understand that the kiln is only lit about once or twice a year. It is no wonder we hadn’t been rewarded with perfect timing until now. Our interview coincided with the first day of the lighting the kiln, which is ordinarily done over a 3-day period. The first day is said to be the most difficult. We observed the first ”grilling” process which raises the temperature inside the kiln. Although equipment such as thermometers are used, nothing can surpass the value of data collected from the past, and instinct. Logs are placed in the furnace as the rise in temperature is monitored.
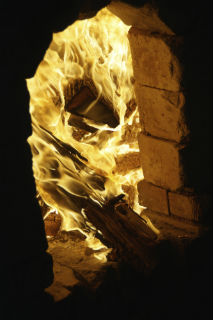
Beauty Relying on Chance
We helped out by placing logs in the furnace. We were completely taken by surprise with the heat. The temperature inside the kiln reaches 1200℃, so the heat is extreme. Imagining and actually feeling this kind heat is a completely different matter. You have to get closer to the kiln in order to raise the temperature in the corners. This was definitely quite an ordeal. You have to be physically fit for the task. Komatsu says, ”You cannot control how the flames move, making the results unpredictable. Only 60% of the outcome is predictable.” Yet the reason they still use the kiln is, ”Because you cannot foresee the outcome. Pieces full of character and beauty are created. ”Factors that can be controlled through manpower and machines are precisely executed. The rest is left in the hands of chance, to fuse coincidence with beauty.
