To know nothing about “katana”
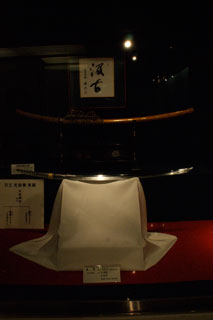
You rarely see a Japanese sword in everyday life. They are intimidating when you actually see them. Today, Nakata visited swordsmith Akitsugu Amata, holder of the title of Important Intangible Cultural Property, his studio and “Token Densho-kan” museum (within Carrion Culture Center.) Kanesada Amata, Amata’s younger brother and his apprentice gave us a tour. His head wrapped in “tenugui” cloth, he was the perfect image of a swordsmith. First he told us the basics of Japanese swords as we observed the display. Nakata asks a simple question, “Why do the curves differ from sword to sword?” “Yes, the blades curving upward when displayed are ’katana’ swords and the ones with the blades curving downward are called ’tachi.’ The difference is whether you hang the sword on your waist and attack the enemy from a standing position or if you are on a horse and attack the enemy.”. The swords differ in shapes, sizes, usage and names. The shapes also differ depending on style or school the user belongs to.
Forging the steel
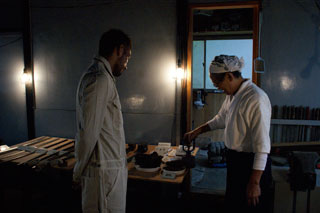
Next at the studio, Akitsugu Amata joins us and he explains to us about the unique Japanese tradition. At this studio, the sword is made from ironmaking. ”We used to collect iron sand with a bucket.” They would put the iron sand in a brick making furnace and make ”tamahagane.” steel. Then they would heat the ”tamahagane” and forge it. The scene we often imagine of swordsmiths pounding on iron is done at this stage. Nakata tries forging the metal. It is hot sweaty labor with blaze of the furnace close by, the iron repeatedly heated in the fire and stroked over and over again.
Make it or break it
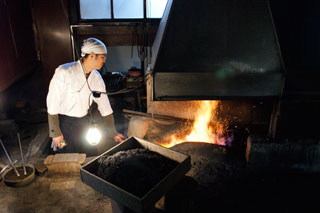
Nakata was only able to observe up to this process, but the actual process continues to further forging, shaping and polishing. The sword is straight during the whole process until one point. “The most difficult step is the Yakiire’ process when we curve the sword. It takes one month to fully forge a sword, and the sword may break in a moment when we apply ’yaki ire.’ It is literally, a make-it-or-break-it moment. The Japanese expression for make it or break it is “Noruka Soruka’ noruka soruka’ (whether it will be straight or be curved)” came from this process,” says Kanesada Amata. At the end of the tour, Nakata was invited to their room to hold an actual sword. Nakata sat on “tatami” in “seiza” style and looked very serious. There was a tense atmosphere in the air.