Shirataka Tsumugi, a tradition of Shirataka Machi
As we entered the workshop, we saw people adjusting what looked like a press machine. We said hello and asked them what they were. We were told that they were machines that they used to dye thread. We were at Komatsu Orimono Kobo, one of the workshops that manufacture Shirakata Tsumugi, a type of Oitama Tsumugi textile that is designated as an Intangible Cultural Asset by the government.
History and Characteristics of Shirataka Tsumugi
The history of Shirataka Tsumugi begins in the Edo period. It is one of the textiles that flourished in Yamagata as the result of the promotion of textile manufacturing, and the production of their raw materials by the Yonezawa clan. THis is the same as the ”Nagai Kasuri” which we also visited on this trip to Yamagata.
After a period when ”Yoneryu” Kasuri was manufactured, skilled workers from Tochigi Prefecture were invited along with the technique called “Itajime”, and a unique textile came to be produced here. The machines that looked like press machines were the machines for the “itajime” method. Shirataka Tsumugi is characterized by the detailed patterns compared to other “kasuri” products in other areas. The “shibo”, or the unique texture of a kind of crease on the textile, is also one of its feature. What gives these characteristics to the Sirataka Tsumugi is the technique called “itajime”. Shirataka Tsumugi flourished in the Meiji era, but there are now only two workshops that continue to make this product. The skills for “itamjime” only survive in these workshops .
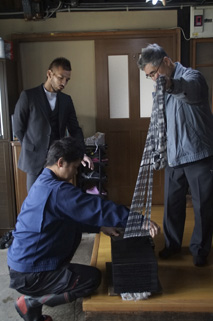
Itajime requires fine skills
Norio Komatsu and his son Hiroyuki were at our interview session.
“Itajime” is a skill where threads are placed between two boards where patterns are sculpted and dyed. What surprised Nakata was the fact that there were patterns sculpted on each board, and the boards have to be combined properly according to the desired pattern.
Normally 30 to 50 boards are used, but the tension of the strings have to all be uniform when the boards are wrapped, or the patterns don’t appear properly when made into a piece of cloth. So utmost care must be given.
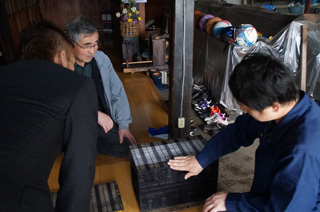
Technology of the machine and the finesse of nature
After the strings are wrapped around the boards, they are tightly pressed together by the press machines. Then the dyes are poured over them and the fabric is dyed. This process is called “bukkake zome”, and the dye is poured repeatedly for over an hour. When that’s complete, the entire process is finally done. Nakata asked him why this process is almost extinct, Mr., Komatsu answered “if the boards get too dry, they can crack and warp. It takes a lot of work to take care of the boards and maybe that’s why people quit using this method.”
The wood used in the boards is natural wood. That makes it difficult to control. But the flexibility of natural wood is not found in artificial materials, and only the natural material can express the finesse of the art. Komatsu also stated “PCs have broadened our horizons in terms of the patterns we can challenge. I want to challenge many new patterns.” The patterns made possible by machines expressed by the flexibility of natural wood. That’s how tradition restarts itself.
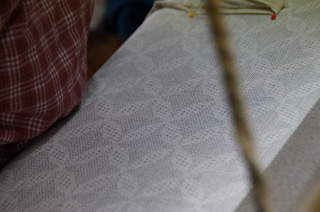
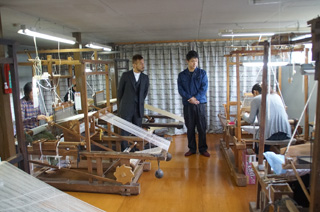