Making “bonsho” bells for temples
The term “bonsho” may not be familiar as most refer to them as “the big bell at Buddhist temples”.
Many temple bells were confiscated by the government for metal during WW2, and many temples still have not been able to replace them to this day. We visited “Watanabe Bonsho”, a company that makes “bonsho” bells for temples.
We interviewed Koho Sugae. On the day of the interview, he was making a small bell as we spoke with him.
Sugae was born in Domachi in Yamagata city, known as the town of metal casting. After training under his father and metal caster, Ichiro Watanabe, he won an award in the Japan Traditional Kogei – Art Crafts Exhibition in 1980. That was followed by various awards in other exhibitions. He was also certified as a Traditional Art Craftsman and is still actively making ”bonsho”.
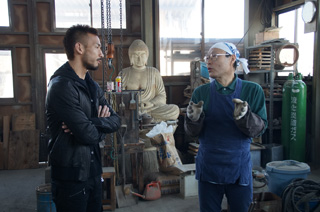
The sound grows
Although one may believe there to be some rules for the “bonsho” bells according to various Buddhist sects, no such rules exist.
“Of course, if you observe past examples, you can find some guidelines for size and proportions. For example, the typical height to diameter ratio is about 1.4, but there aren’t any explicit rules, and you are free to design on your own.”
Sugae told us that the designer’s thinking is reflected in the design of the bell. Sugae studied acoustics in pursuit of “good sound”. Basically, the sound of the bell resonates at a right angle.
So, if your bell is going to be rung in a flat area, you think about how it sounds from the side of the bell. But if you are making a bell for a temple on top of a hill, you think about how it sounds below the hill.
It is his policy that he will not make a bell that people will “hurt the ears” if people are standing close to the bell when the bell is rung. He also told us that sometimes the bell sounds better several years after completion. “The sound gets broken in” he described.
It’s as if these bells are alive. I still don’t understand why but such things happen.”
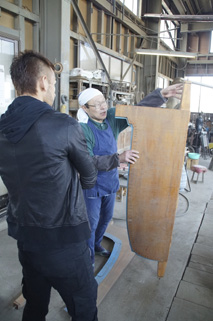
Feeling a reluctance to part
Sugae describes ”bonsho” as being alive, but there is a difficulty in bell making using a tin and copper alloy that cannot be explained with words.
”It’s fine if it goes well, but there some cases where you fail.”
The manufacturing process begins when you get the order. He draws a plan and a wooden mockup is made according to the plan. Then, he makes a mold of the core and an outer mold using sand, melt the bronze and tin, then pour it into the mold. After the metal has cooled, the mold is broken and the bell is taken out.
Yamagata is famous for its cast metal products, and accounted for a large share of the tea ceremony kettles at one time. Many people were designated as Human National Treasures, and that tradition still breathes in this city.
Most of the materials are bronze. Green rust (verdigris) on bronze is the color of the bell that we usually think of. But bronze is heavy. We were handed a bronze billet, but it was much heavier than it looked. To make a 150 kg bell, 200 kg of bronze is needed. Sometimes the bell is larger and heavier, and then it becomes impossible to work alone. There are cases when over 1 ton of bronze is needed. Even when the bell is taken out of the mold, additional steps are involved, like polishing. The bell can only then be delivered to temples or shrines.
“There are a lot of steps and time involved before a bell is complete, so sometimes, I’m reluctant to part with the bell.“ Sugae told us. Perhaps the feeling is similar to when your child is getting married and leaving home. But that child will “grow”, and produce an even better sound. As we listened to him talk, we saw a small bell coming to life in his hands.
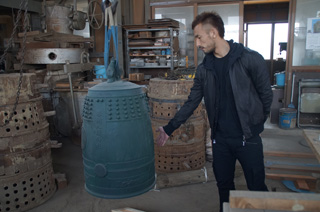
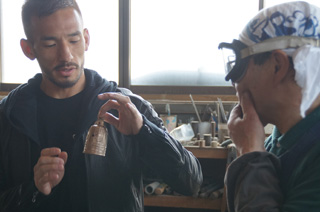