The Name “Edo Komon” was only established 60 years ago?!
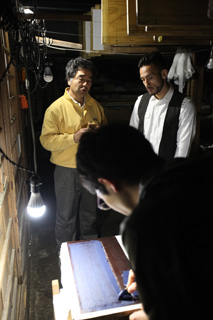
As peace prevailed during the Edo period, the feudal lords all started to compete with lavish kimonos. In despair, the Edo Shogunate issued a new regulation, banning samurai from wearing luxurious attire. In reaction, the feudal lords came up with kimonos that looked plain from afar, hiding the designs by making them small and inconspicuous. As a result, dyeing skills developed, resulting in what is now called the Edo komon.
The style of Edo komon as such has a long history, but the name ”Edo komon” has only been around for about 60 years. When Yasusuke Komiya was designated Important Intangible Cultural Asset holder, the word ”Edo komon” was used to differentiate it from other forms of komon-dyeing. We visited his sons, Yasutaka Komiya and Yasumasa Komiya. Yasutaka Komiya was also designated Important Intangible Cultural Asset holder in 1978.
Edo komon is possible because of division of labor
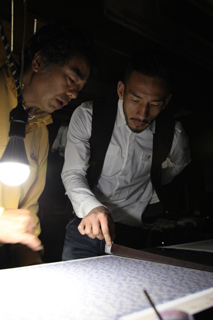
Edo komon is stencil dyeing. The stencils that are used are ”Ise” and dyeing skills require much experience. Yasumasa told us, ”Our mission is to preserve the technique, not the work.”
The workshop is pitch black. The reason the windows are closed and light blocked out, is to control the temperature so as not to affect the stencils and glue. White cloth is attached to a board 7.2 meters long, a stencil is placed upon it, then the glue is applied. This process is repeated dozens of times until the design is applied on the entire roll. It is dried, dyed and steamed for the color to stabilize, then everything is washed off. Finally this chic and stylish roll of kimono fabric is complete.
”It is a traditional technique, but if we find a better way, we’ll try it out.” True to these words, a boiler is used for steaming. At the same time, there is no substitute for the glue they use, which is made of rice bran. Now, as flour mills who produce this vanish, they face a critical situation.
Yasumasa mentioned that the making of Edo komon requires many processes, and the process is divided. It is important for not only his techniques to remain, but the materials and the tools as well, in order for the traditional ”kimono” to be preserved. The ”washi” for the stencils, the knife to cut the stencils, the silkworms that create the rolls of ”kimono” fabric, all of these things make Edo komon possible.
Using New Stencils
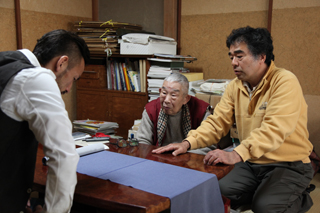
The motto of the Komiya household is that the stencils will be preserved. This does not mean that they are going to store old stencils to be reused over and over. On the contrary, they always use new stencils. Yasutaka told us that his father, Yasusuke Komiya once said, ” If you keep using the existing stencils repeatedly, the stencil makers cannot make a living. So you need to place new orders for the stencil makers to thrive. That is how skills develop.”
Without stencil makers, Edo komon would not be able to make any advances. That is why new stencils are used even for traditional motifs.
”We cannot let the stencils die out. They are the basics of Edo komon, the fundamentals.”
To succeed tradition means to consider how stencils can survive ”in the present modern world.” Understanding the past and being particular about the present. That will lead to the future. The traditional method will be handed down by continuing to create, protecting the many skills that relate to the creation of Edo komon.