The pride of Amami Oshima
Most think of Amami-Oshima when they hear the world Oshima associated with Kagoshima. It is the fifth largest remote island in Japan and was registered as a World Natural Heritage in 2021. A 30-minute drive from Amami airport, the atelier for Kanai Kougei is located at the tip of the island with a clear blue ocean and tropical plants. Kanai Kougei still continues to use traditional methods to dye the textile naturally, a method that is exclusive to this island.
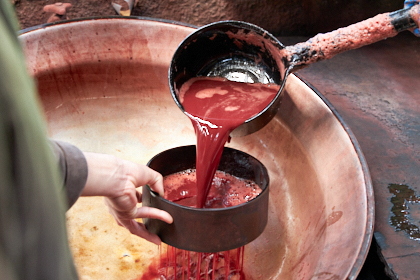
Characteristics of Oshima Tsumugi which is popular as kimono
Oshima-tsumugi is one of the world’s top 3 textiles, alongside the French Gobelin’s tapestry and Persian rugs from Turkey.
It take anywhere from 6 months to more than 1 year to create one sheet of Oshima-tsumugi which requires 30-40 steps.
Characteristics of Oshima-tsumugi include the beautiful shine which results from the careful handwork of the craftsperson and the lightweight warmth that is also wrinkle resistant. Made durable to last 150 to even 200 years, many pieces are worn by three generations.
“Oshima-tsumugi has a history of about 1300 years, and is a staple craft of Amami characterized by a division of labor. I left Amami, but came back to take over the atelier when I was 25. I enjoy the interaction with both the locals and transplants, thinking of ways to carry on this tradition.” (Yukihito Kanai)
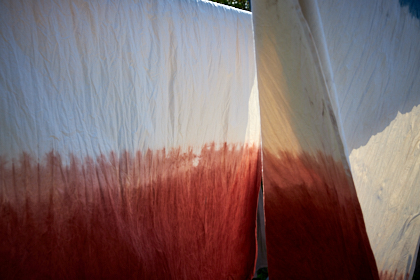
Using a plant that is local to Amami, the tannin reacts with the iron in the dirt, bringing out a dark black. Although the plant is seen around the country, the breed in Amami has a particularly dark color.
“Many think of the shiny black silk kimono representative of Oshima-tsumugi, but how many times do you have to repeat the dyeing process to achieve the black color?” (Nakata)
“It takes 80 to 100 times. It’s soaked in the dye, then allowed to have a chemical reaction in the dirt, hung dry, then washed. This process is repeated over and over again. It takes about a week when the weather is good.” (Mr. Kanai)
The dirt contains a lot of iron that seeped out from 150 year old soil layers, bringing out a black color that is exclusive to this area.
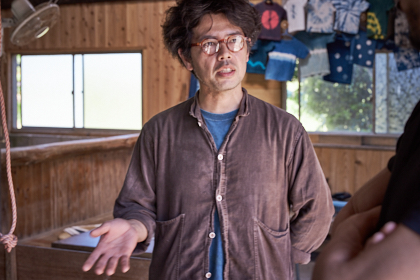
Fusion of traditional “Oshima Tsumugi” and modernity
While it is a craft that is rooted in local nature, only 4 or 5 ateliers remain from the more than 100 that used to thrive on the island. In the adjacent gallery, tapestry, scarves, t-shirts, dresses, and other items dyed in dirt are displayed and sold. Known for fusing traditional and modern techniques, Kanai Kougei is often approached by brands interested in collaborative efforts. The beauty of Japan is supported by skilled craftspeople who are committed to their craft, and the intuition of the young is helping to unearth the potential that Japan has to offer.
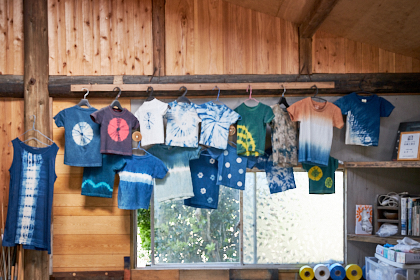
![]() |
Most think of Amami-Oshima when they hear the world Oshima associated with Kagoshima. It is the fifth largest remote island in Japan and was registered as a World Natural Heritage in 2021. A 30-minute drive from Amami airport, the atelier for Kanai Kougei is located at the tip of the island with a clear blue ocean and tropical plants. Kanai Kougei still continues to use traditional methods to dye the textile naturally, a method that is exclusive to this island.
|
Oshima-tsumugi is one of the world’s top 3 textiles, alongside the French Gobelin’s tapestry and Persian rugs from Turkey.
It take anywhere from 6 months to more than 1 year to create one sheet of Oshima-tsumugi which requires 30-40 steps. Characteristics of Oshima-tsumugi include the beautiful shine which results from the careful handwork of the craftsperson and the lightweight warmth that is also wrinkle resistant. Made durable to last 150 to even 200 years, many pieces are worn by three generations. “Oshima-tsumugi has a history of about 1300 years, and is a staple craft of Amami characterized by a division of labor. I left Amami, but came back to take over the atelier when I was 25. I enjoy the interaction with both the locals and transplants, thinking of ways to carry on this tradition.” (Yukihito Kanai) |
![]() |
![]() |
Using a plant that is local to Amami, the tannin reacts with the iron in the dirt, bringing out a dark black. Although the plant is seen around the country, the breed in Amami has a particularly dark color.
“Many think of the shiny black silk kimono representative of Oshima-tsumugi, but how many times do you have to repeat the dyeing process to achieve the black color?” (Nakata)
|
The dirt contains a lot of iron that seeped out from 150 year old soil layers, bringing out a black color that is exclusive to this area. While it is a craft that is rooted in local nature, only 4 or 5 ateliers remain from the more than 100 that used to thrive on the island. In the adjacent gallery, tapestry, scarves, t-shirts, dresses, and other items dyed in dirt are displayed and sold. Known for fusing traditional and modern techniques, Kanai Kougei is often approached by brands interested in collaborative efforts. The beauty of Japan is supported by skilled craftspeople who are committed to their craft, and the intuition of the young is helping to unearth the potential that Japan has to offer.
|
![]() |