Yuki-tsumugi representing Ibaraki
After the cocoons are boiled for about an hour, skilled workers carefully form silk floss in tubs. Sild thread is carefully pulled from the floss. This traditional method is still being used to create Yuki-tsumugi in Yuki, located in the western part of Ibaraki prefecture. Yuki-tsumugi is a traditional craft from Ibaraki and is also a registered UNESCO intangible cultural heritage.
“We use our saliva to weave the thin threads together. The protein in saliva allows us to bundle the thin fiber together to form the thread.”
Hajime Mori is one of the craftsperson who carry on the tradition of Yuki-tsumugi. The atelier is equipped with a “jibata”, or weaving machine, and a stand used to dye the thread before its woven.
Yuki-tsumugi uses a method where the thread is dyed before it’s woven. There is careful calculation involved in creating the flowers, plants, and other designs by weaving the dyed thread vertically and horizontally.
Portions of the thread are covered with cotton thread to allow the original color to remain during the dye process, and used to create the final design.
The dyed thread are beautiful even before they are woven, and Nakata commented that “displaying the thread would be attractive.”
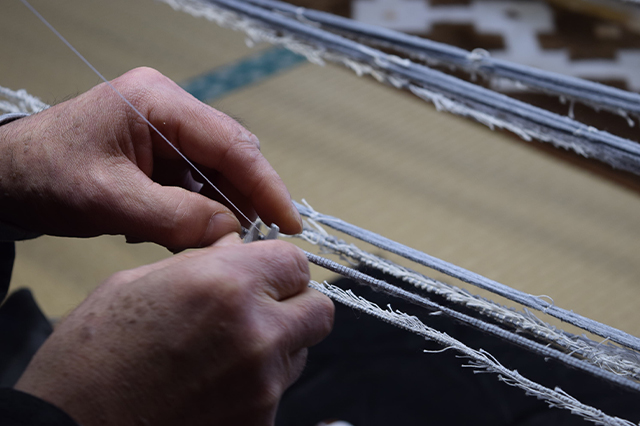
The quality of Yuki-tsumugi is recognized around the world and has been used for collaborations with renowned brands to create suits and fabric. We spoke with Yoriyuki Okusawa, the 5th generation of Okujun, the weaver which has carried on the traditions of Yuki-tsumugi since its establishment in 1907.
“The characteristic of Yuki-tsumugi is that the thread is hand-pulled from the silk floss and woven with a `jibata` weaver. The `jibata` is low to the ground compared to other weavers, requiring the weaver to use the entire body. The unique shape is said to be the inspiration for the folk tale `the crane’s gratitude`. It can take up to 5 months for 1 sheet of fabric because there are more than 40 steps involved including pulling the thread from the floss. Complicated designs can take a few years.”
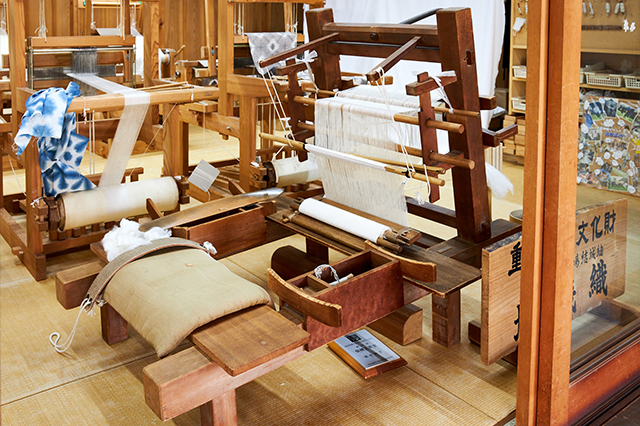
Museum telling the story of Yuki-tsumugi
Pulling thin fiber from a large floss of silk and threading them by hand. The daunting task of making thread can take up to three months.
“The cocoon protects the silkworm. It doesn’t allow ultraviolet rays through, maintains a comfortable level of humidity, and even has anti-bacterial properties. This is incorporated in the Yuki-tsumugi, allowing for the comfort when you adorn it.” (president Okusawa)
The dyeing process is also painstaking. Tying cotton string to the silk thread to create a pattern. Bunching several millimeters of thread together and adjusting the cotton thread to achieve the desired pattern. The knots must all be the same tightness. On some days, Mr. Mori repeats this process more than 2000 times in a single day. Yuki-tsumugi is light and graceful, a result of the many painstaking hours of labor. It must be delightful to be enveloped in a kimono made from this very special fabric. It is sure to be a top candidate when Nakata has a new kimono made.
Okujun is involved in planning, designing and selling Yuki-tsumugi as a wholesaler. In 2006, a museum was opened on the property housing documents that relay the technology and history of Yuki-tsumugi. Okujun is also involved in developing new products such as scarves and small products in addition to the traditional kimono. There is also a store selling Yuki-tsumugi items and a workshop where visitors can experience the craft. It is a comprehensive cultural facility that passes on the significance of Yuki-tsumugi.
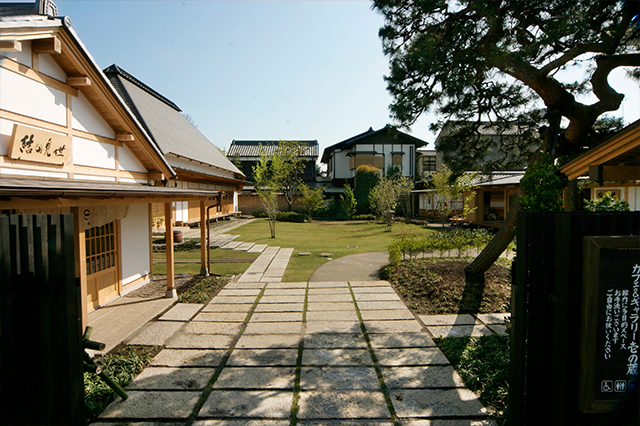