Bizen Pottery is the most famous pottery in Okayama. Bizen Pottery is a type of pottery with a strong earthy flavor that is fired over a long period of time. Koichiro Isezaki grew up with a grandfather and father who were both Bizen potters, and he grew up in an environment where pottery making was close at hand. However, his desire to create Bizen Pottery came later than expected, around the time he graduated from university, where he studied sculpture. He found himself drawn to three-dimensional modeling using clay.
Japan’s Six Old Kilns, dating back 800 years to the present
Bizen Pottery is one of the “Six Old Kilns of Japan,” named by antique ceramics researcher Fujio Koyama along with Seto, Shigaraki, Echizen, Tokoname, and Tanba Tachikki-yaki as representative ceramic kilns that originated in the Heian and Sengoku periods, the so-called Middle Ages, and continue to be produced today, and was recognized as a Japanese Heritage in 2017. Its production area is located in the vicinity of Ibe, Bizen City, in the southeastern part of Okayama Prefecture. The brownish-brown color of Bizen ware is created by using iron-rich soil from this region and “firing without glaze. The kiln takes more than a week to fire the pottery, and the temperature is raised slowly to make it more durable. Although the pottery is not decorated, various colors and patterns can be produced depending on the placement of the kiln and the way the wood is used to fire the kiln.
Techniques that have continued to the present day, adapting to the times.
It began about 800 years ago. At the end of the Heian period (794-1185), a group of potters moved to this area in search of abundant clay and firewood. During the Kamakura period (1185-1333), they began to produce daily utensils such as suribachi (mortar and pestle), jars, and tsuyu (earthenware made of porcelain and porcelain). In the Azuchi-Momoyama period, the tea ceremony became popular, and it is recorded that Sen no Rikyu and Toyotomi Hideyoshi frequently used Bizen ware jugs and other tea utensils at tea ceremonies.
Bizen ware potters have continued to produce what the times demanded using the clay and firing methods available in this area. Even if a tea master in the capital asked for a particular shape, it was not possible to create it exactly as it was. The clay we make with our own clay, which has a strong and firm consistency, is suitable for that purpose. I think we have worked hard to think about what we can do and adapt to what we can do. Koichiro Isezaki thinks back to the Bizen potters of ancient times.
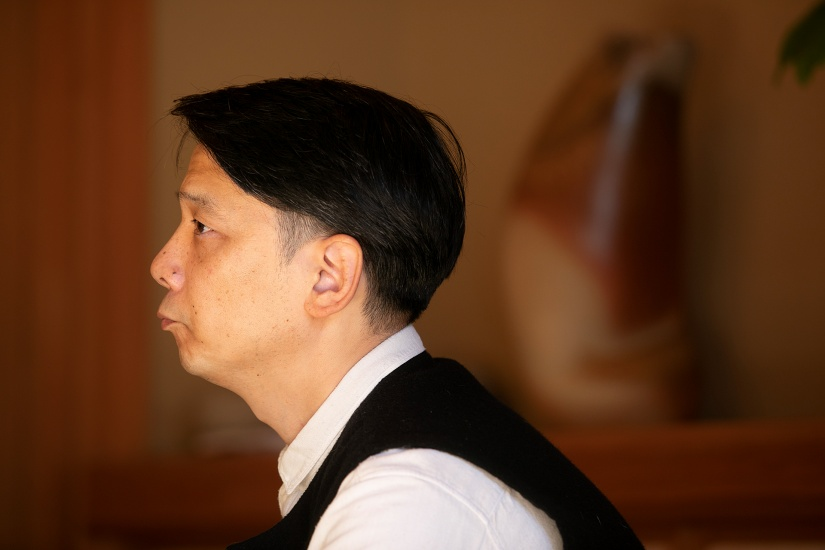
Studied sculpture at university and yakizome in the U.S.
Mr. Isezaki was born in Ibe, Bizen City, in 1974 as the eldest son of Jun Isezaki, a Bizen potter. He grew up in an environment where his father and his apprentices were busy at work and bookshelves were lined with collections of sculptures and art works. Naturally, creativity was close to his heart and always in his mind. Wanting to study sculpture at university, he entered the Department of Fine Arts at Tokyo Zokei University. When he left home, he told his father, “I don’t think I will do pottery,” to which his father responded, “Hmmm. He had been carving wood, but as he neared graduation, he decided that he wanted to try his hand at three-dimensional modeling using clay. After graduation, he studied with his father for a year and then moved to the United States to study under Jeff Shapiro, a longtime friend of his father’s and one of America’s leading ceramic artists.
Shapiro has a studio in the suburbs of New York City, where he studied pottery with yakishime for two years. After spending days watching Mr. Shapiro’s movements as he pulled the potter’s wheel, which seemed to be in a session with the clay in front of him, and through stimulating encounters with many people, Mr. Isezaki’s position on Bizen Pottery changed. Rather than wanting to make Bizen Pottery or vessels, I want to do three-dimensional modeling using clay, fired over a firewood fire. I want to share the goodness of clay with others and empathize with them. This was his entry point into Bizen Pottery.
Working side by side with my father
When Mr. Isezaki turned 30, his father, Jun Isezaki, was certified as an Important Intangible Cultural Property holder (Living National Treasure) in Bizen ware. Currently, father and son both work at their respective studios on the same site. From Mr. Isezaki’s point of view, his father Jun’s work can be summed up in one word: “generous. His personality comes through, and his creations do not intimidate people. On the other hand, Mr. Isezaki’s works, while adhering to traditional techniques, have unique forms that seem to express the strong energy of the clay, and are finely detailed and expressive in a variety of colors and textures. Jun and Isesaki have three kilns side by side at the foot of the mountain behind their studio, the largest of which is about 15 meters long and the medium-sized one about 10 meters long. Mr. Isezaki uses the same medium-sized kiln and a smaller kiln about 5 meters long, and fires the kilns two or three times a year.
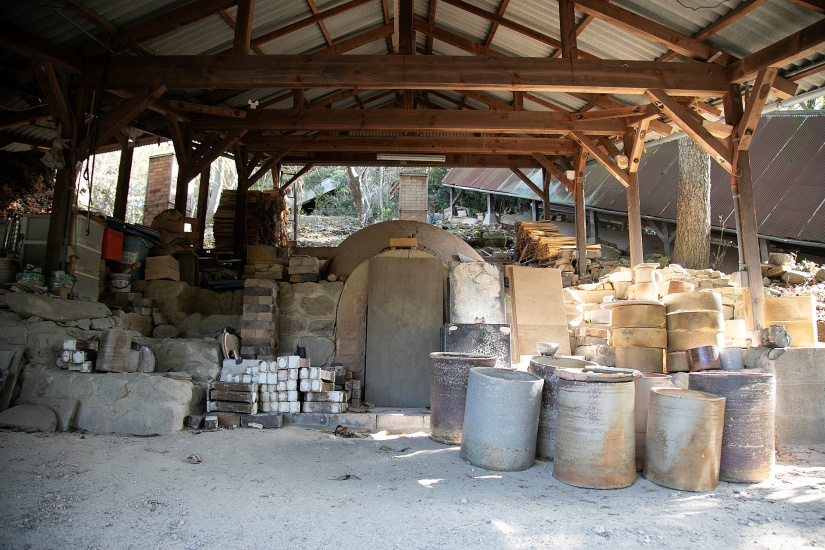
Painting with Kiln Filling
The kiln-filling process is what determines the finish of Bizen ware. In order to arrange several hundred pieces in the kiln, the “burn” (finish) is controlled by reading how the flame hits the pieces and how the ash falls on them, the distance from the kiln opening, the placement of pieces of different sizes, and the angle of the pieces in relation to the flame. He calls it “painting in the kiln,” and says that arranging the pieces one by one is like putting together a puzzle. Basically, the pieces that are exposed to the flame are reddish brown, and those that are not exposed to the flame, such as the shadows of objects, are white. The ashes from the firewood of the red pine trees fall on the surface and melt at high temperatures, producing patterns such as “sesame,” which is a characteristic of Bizen ware (due to the natural glaze). No matter how long the kiln is, the front and the back of the kiln are connected, and the pieces placed in the kiln affect each other. For this reason, from the molding stage, he imagines where and how the pieces will be placed before making them.
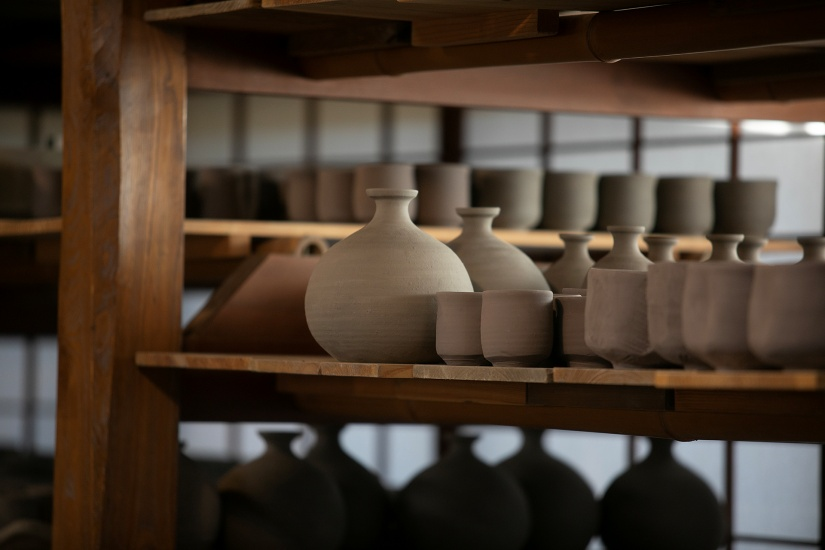
However, it is not possible to produce the desired burn in millimeters. If you want everything the way you want it, you don’t choose this method. Mr. Isezaki says, “If you want everything the way you want it, you don’t choose this method. I think people who believe there is something important in this process are making this pottery here. When I tried using a different kind of clay and an electric kiln in the past, I realized that I was being kept alive by the emotion that comes from a wood-fired kiln. When you are dealing with nature, there are many uncertainties. But I think it is important to have the ability to deal with such things. I want to keep the sense that I can make my creations work in an environment that is constantly changing.
Kiln firing is a feeling of communion with nature
Kiln firing takes 13 days in a 15-meter kiln and one week in a 5-meter kiln. The temperature is raised slowly because the clay shrinks greatly, and if the temperature is raised too high at the beginning, the clay tends to break easily. Each kiln has its own theory, and the amount of firewood and firing time are calculated to ensure that each piece is fired to the expected temperature and time, with the three of them taking turns firing day and night every eight hours. Mr. Isezaki says he likes this time. He says he likes this time because it gives him time to clear his head. The last day and a half of firing is called “attack” or “big firing,” in which the front door is closed and wood is burned through a hole in the side of the kiln. Then the ashes fly all over the kiln. The temperature rises, baking the clay and melting the ashes at high temperature. The maximum temperature is 1250 to 1260 degrees Celsius. If the kiln is only to be fired, four or five days are sufficient, but if the potter wants to obtain the desired “burn,” such as a deep scarlet color, this is the number of days required.
The appeal of wood-fired pottery is the feeling of communing with nature. The wood has a life of its own, and we are allowed to burn it. The use of red pine, which has a high fat content and burns at high temperatures, is a form of wisdom discovered by our ancestors. Similarly, clay is a natural resource and finite. Bizen Pottery has become a technique that has continued to the present day because of this soil, which was created over millions of years, and there is a strong sense that it is made up of takarikimono. It is similar to agriculture, forestry, and sake brewing, and I believe that it is the farmer’s job to draw out the power of the ingredients so that he can produce what he considers “tasty. I believe that Bizen Pottery is absolutely necessary for people to live with nature.
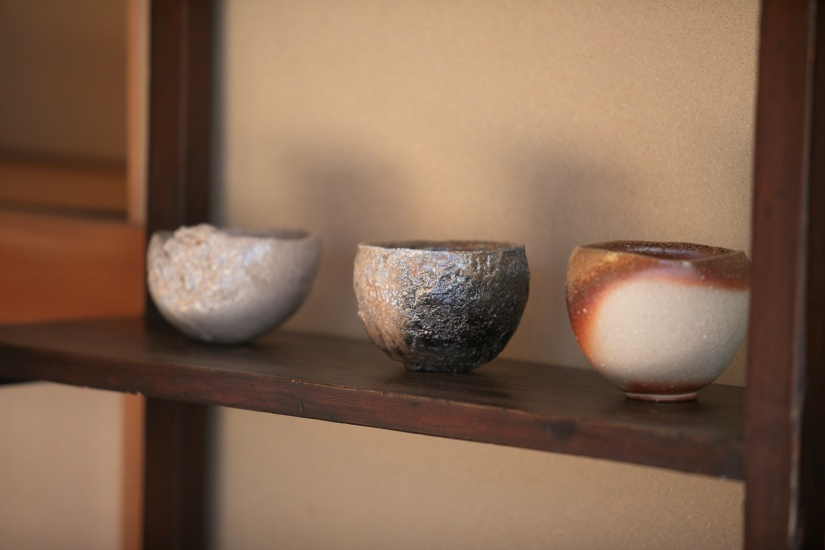
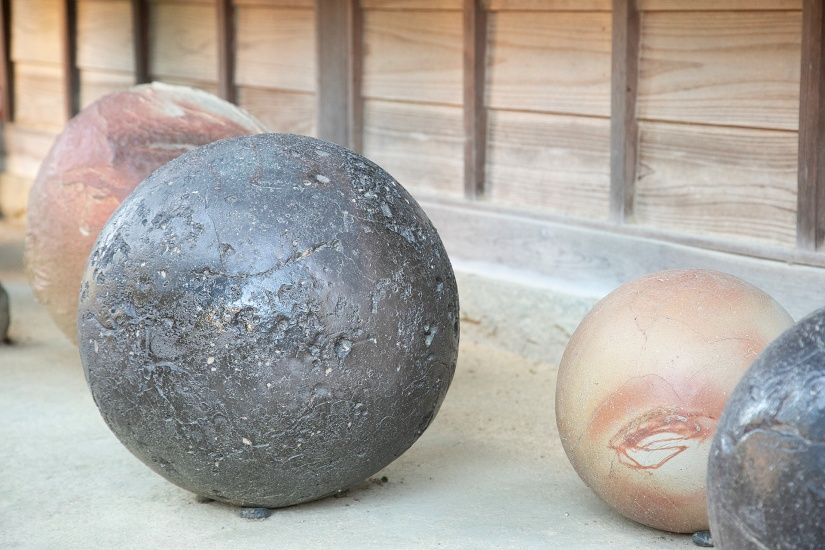
Find the power of baking tightening that you have not yet realized.
Mr. Isezaki was awarded the 2022 Ceramic Society of Japan Award. The award is given to the most outstanding artist of the year in the ceramic art world. It has been 21 years since he began to show his works in public. In a family where not only his grandfather and father but also many of his relatives are Bizen potters, he has been able to express himself because when he took the plunge and started a new experiment, he met people who encouraged him and said, “Interesting. That is why I only pursue works that are attractive in themselves. I am still searching for the power of the firing process that I have not yet discovered, thinking that there must be more colors and textures to be found before I can be convinced that the finished piece is “good. His philosophy is that there must be more, there must be more, and based on this philosophy, Mr. Isesaki’s pottery continues to be updated on a daily basis.