Yoshio Sakai, who runs a workshop called “Rokurosha” in the Kawada district of Sabae City, Fukui Prefecture, the birthplace of the traditional craft of Echizen lacquerware, has been devising and commercializing minimalist designs that take advantage of the beauty of wood grain, which only a woodworker can appreciate.
The Shrinking Work of the Woodworker
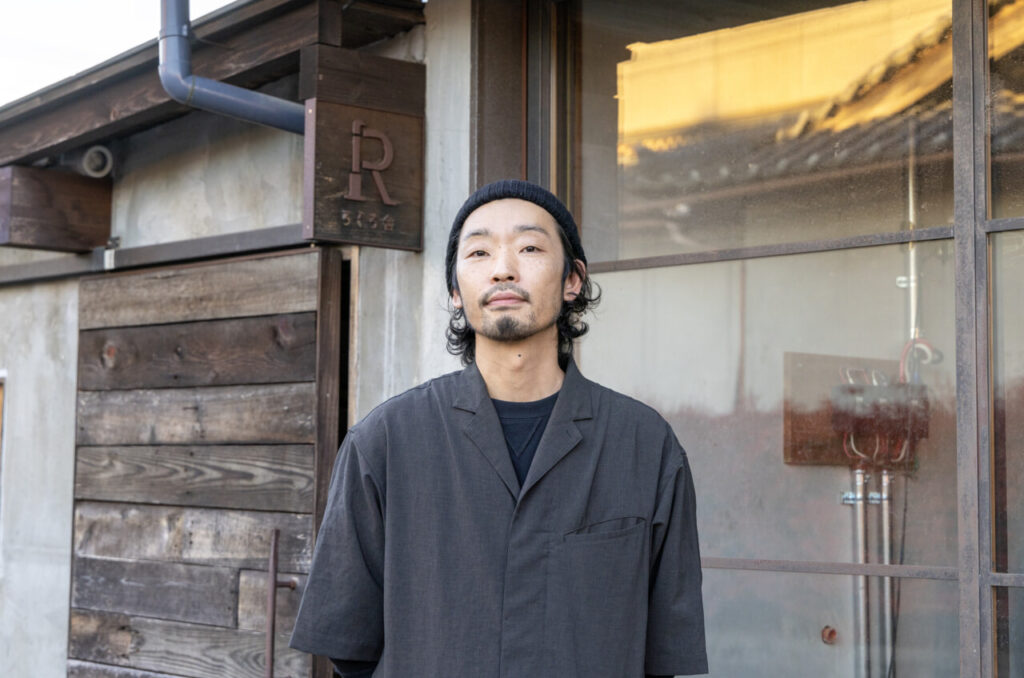
The Kawada area in the mountains east of Sabae City, located in the center of Fukui Prefecture, has been producing Echizen lacquerware for more than 1,500 years. Lacquerware production is based on a division of labor, and even today, craftsmen skilled in such specialized techniques as woodworking, undercoating, intermediate coating, overcoating, and decoration have set up their own workshops and are self-supporting.
Among these, the woodworker is also called a “jijiya” (woodworker) or “rokuro-shi” (turner), because he or she turns a potter’s wheel and applies the blade to the wood to hollow out bowls, trays, and other objects. In Fukui Prefecture, too, the name “Rokuroshi” still remains in Echizen-cho, Niugun, relatively close to the nationally known Fukui Prefectural Dinosaur Museum (Katsuyama City), indicating that woodworkers were active in the area.
Today, however, the number of woodworkers has been shrinking due to the spread of inexpensive materials such as plastic that can be cut out of molds, and only a few bowl makers remain in Kawawada. It was 15 years ago that Mr. Sakai, a native of Otaru, Hokkaido, jumped into the “declining sun” of the woodworking industry.
Using the beauty of wood grain in bowls, which only a woodworker knows how to do.
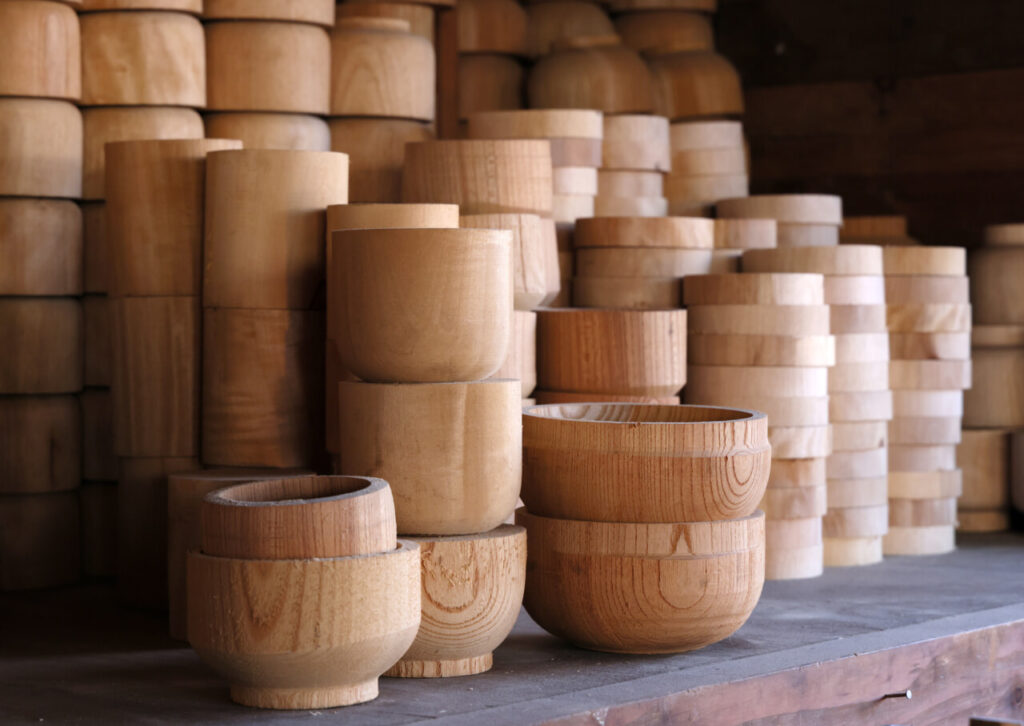
The “BASE” series of vessels, which Mr. Sakai invented and commercialized himself, features a sturdy, vertical design with a beautiful grain of wood and a ceramic-like base. The “wuki-urushi” technique, in which raw or black lacquer is repeatedly applied and wiped off with a cloth, is used to finish the product, so the original wood grain and warmth of the underlying surface can be enjoyed, and the more it is used, the more luster it acquires. The materials used include mizume-zakura, zelkova, tochi, and sen. “I wanted the users to see the charm of the grain that I felt when I was making the wooden base,” says Sakai. By applying lacquer, which is not mixed with pigments or other colors, the fine grains of the wood give it a sense of weight and a modern feel.
Hints of the unique form come from the bowls of the table
The roots of the rugged yet sophisticated shape can be found in old bowls, which Mr. Sakai likes to use. He was inspired by the bowls of the medieval times, when people ate by arranging dishes on the floor or on a table, and took inspiration from Goshika bowls, Yi Dynasty vessels, and ritual vessels made in Noto Town, Ishikawa Prefecture. The bowls are tall, easy to lift, and stable. The bowls are also suitable for serving soups, soups and rice. When used at the table, it does not stand out too much, but when placed on a shelf with other tableware, its linear form gains presence, and the longer it stays with you, the more you will be charmed by its expression that changes over time.
Receiving an order for tableware during a consultation
Another of Mr. Sakai’s representative products is the “Only Bowl. Using a “rokurosha,” a wagon that has been converted to allow work on it, he visits stores and events throughout Japan to give demonstrations and create original bowls by semi-custom order, combining shapes and lacquers. The material is zelkova, and there are five shapes, including kihon, hazori (edge warp), and tsubomi. The shapes of the bowls are also incorporated into the bowls, such as “Imoni Bowl” for Yamagata Prefecture, “Sara Udon Dish” for Nagasaki Prefecture, and so on, which are familiar to the locales and climates of the regions they have visited. Seven types of lacquering are available, including clear, wipe lacquer, and shin-nuri. The shape of the bowl is determined by counseling the customer face to face, asking them what shape, size, and purpose they need. He also provides detailed instructions on how to care for them.
A young man who wanted to be free became a craftsman.
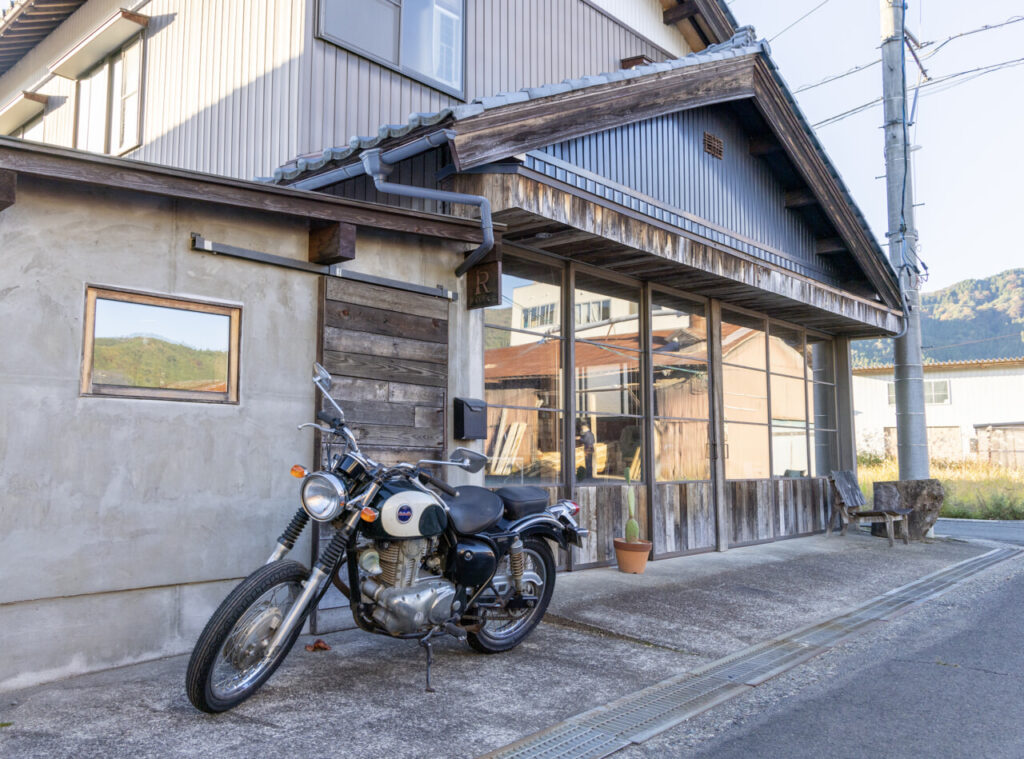
Mr. Sakai, who is tackling new challenges one after another, says of himself, “I always want to be free, and I don’t have any goals or plans. I am the type of person who goes his own way,” he analyzes. In his youth, he attended design school, went abroad, and wandered around the country until he was 25 years old, He decided to learn the techniques as a trainee at the Echizen Lacquer Ware Cooperative Association.
Questions about the position of the wood craftsman in the production area
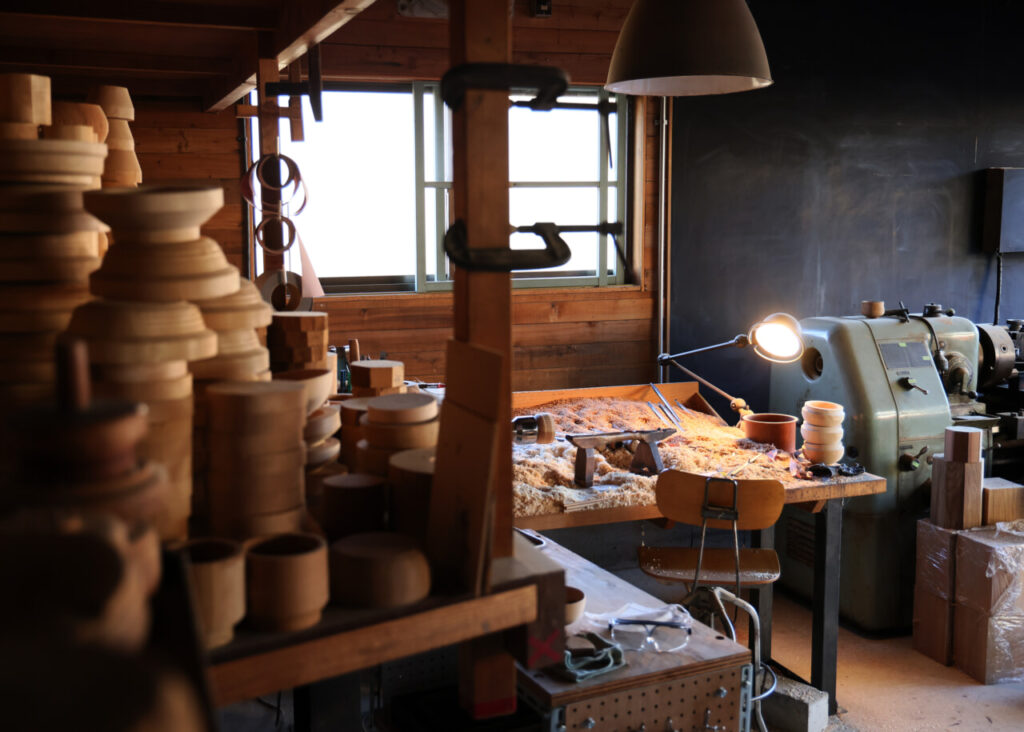
After three years of training, he established his own business, Rokurosha, in 2014 at the age of 34. At the same time, he got married, but opportunities for subcontract work did not present themselves for a craftsman with little experience. My wife’s parents are also craftsmen, so they were worried that I would have to bow down to the wholesalers or join the union,” he said. However, Mr. Sakai saw the decline of the production area while continuing to do things the old-fashioned way, and he had his doubts.
The vessels worked on by subcontractors simply go through the process of making lacquerware and then into distribution. They have no opportunity to communicate the quality of their products to the outside world, and they do not know how much they are priced. Mr. Sakai felt that if he could communicate the high quality of the bowls made in Kawada, they would reach the people who use them.
Plant planter born as an original project
If I can’t get work, I’ll make it myself,” he thought. He began planning an original product to be exhibited at trade shows and directly communicate the quality of his products to users.
He decided that there was no need to stick only to eating utensils in the first place. He changed his point of view and created a planter for plants using thinned cedar wood from Fukui Prefecture. Under the concept of “redefining value,” the planter was made of a material that would return to the soil in the end, and was designed with the idea of enjoying the fun of the process of cracking, splitting, and decay as it is used.
A path pioneered by a woodworker who cannot be pigeonholed into the conventional wisdom
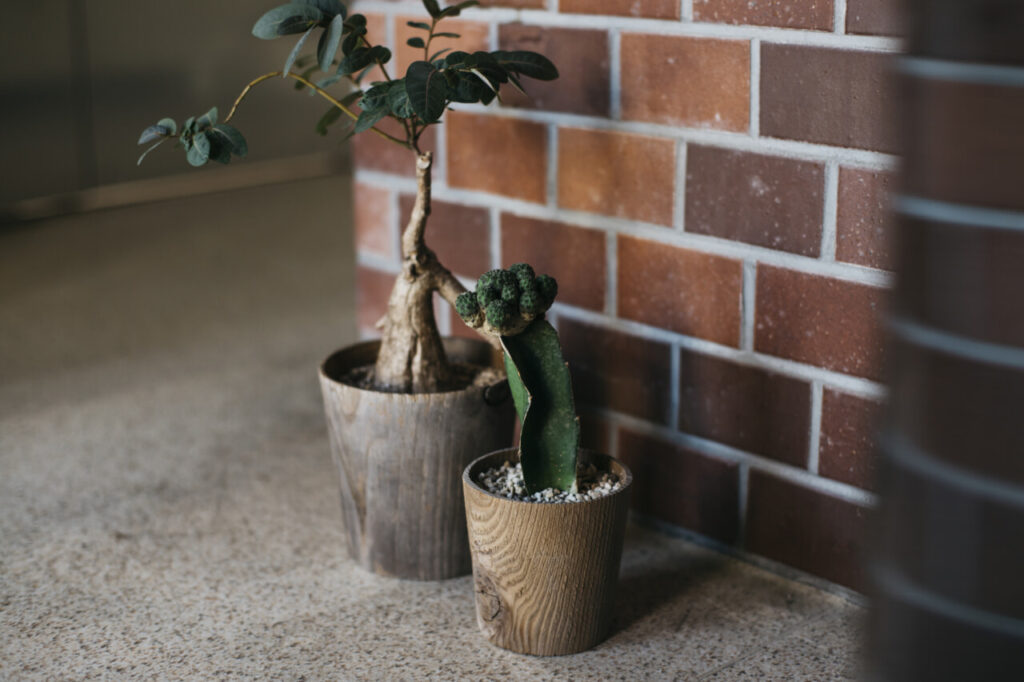
The “TIMBER POT” was carved from a cedar log that had withstood the wind and snow of deep snow in Fukui, and designed without painting to bring the individuality of the grain expression to the fore. The product was exhibited at Interior Lifestyle 2015, an international trade fair for interior and lifestyle product design held at Tokyo’s Big Sight, where it received the “Young Designer Award” for the best designer.
A big breakthrough for “TIMBER POT.”
The extra prize was an invitation to ” Ambiente ” in Germany, the world’s largest interior trade fair. It was a great stimulus to be in a place where designers and buyers from all over the world gathered. In addition, the Ministry of Economy, Trade and Industry selected the company for “The WONDER500™,” a project to promote local products to overseas markets. The concept and design of the “TIMBER POT” became the talk of the town, and was covered by many media outlets.
Only one year after becoming independent. As his name became well known, the number of subcontracting jobs increased, but then the business gradually slowed down. In the process, Sakai began to realize the immaturity of his own skills as a wood craftsman.
The response he got from the “RENEW” event in the production area
He felt that he could not compete on the same playing field as a woodworker who had been grinding on a full-fledged wheel. At that time, a trade fair ” RENEW ” was held in which traditional craftsmen in the Kawada district and other areas cooperated with each other. It was a large-scale event for traditional crafts, attracting about 37,000 visitors over three days (in 2022), including many studio tours and talk events.
Among them, Mr. Sakai’s only bowl was well received by the younger generation who visited. There are definitely people who are interested in and cherish tradition, and they go to great lengths to visit the countryside,” said Mr. Sakai. We hope we can deliver our approach to craftsmanship and our commitment to quality to these people,” he said.
He would make samples of each process, including shape, paint, and process, and explain them directly to customers face-to-face. Seeing a breakthrough in this area, Sakai decided to travel throughout Japan himself, relying on acquaintances with whom he had been maintaining close ties through social networking services and other means.
Winning Patterns” in Human Connections
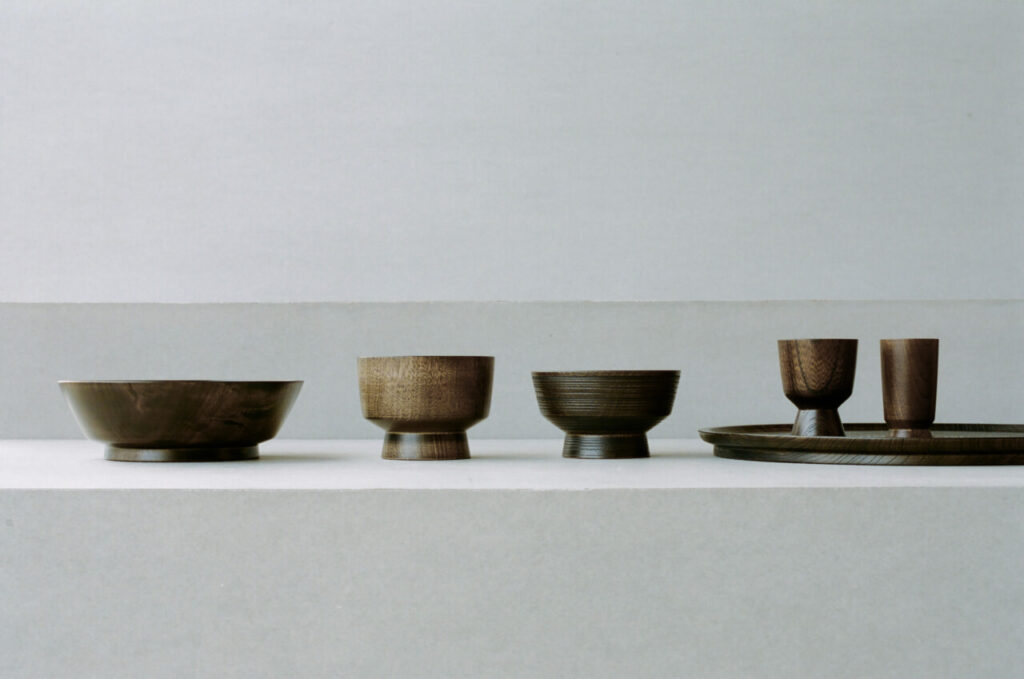
As he traveled to nationally known boutiques and small local general merchandise stores to take orders for bowls, “I began to see a winning pattern,” he said. Orders are paid for in advance, but delivery takes six months, and the price is a hefty 10,000 to 20,000 yen. Even so, he has found that the motivation to purchase Mr. Sakai’s bowls is not the location or brand, but trust in the person. In other words, going to a place where people (shopkeepers) are accompanied by people (customers), and then carefully conveying one’s thoughts and feelings to foster trust in the product is what moves customers.
The Challenge of Crowdfunding
Next, Mr. Sakai came up with the outlandish idea of moving the workshop itself and having customers watch him work at various destinations. He believed that responding to customers’ detailed requests on the spot and allowing them to experience the manufacturing process itself would lead to the greatest trust and interest in his products. Local wood could also be used as a material.
Thus, in June 2020, Sakai launched a crowdfunding campaign for the production of a mobile workshop “rokurosha,” and thanks to widespread enthusiasm expressed through social networking and talk events, the project was a success with much support from the younger generation, mainly from urban areas. The project raised approximately 3.3 million yen, nearly twice the target amount. The completed “rokurosha” has now visited 20 stores in 15 prefectures.
Thinking about the lacquerware industry as a craftsman who lives in the production area
Currently, Mr. Sakai is actively planning original products. He is actively involved in the planning of original products. He also undertakes product planning in collaboration with interior design stores and other companies, and shares the work he creates with local craftspeople. He says, “I hope I can be of some help in making the production area as prosperous as possible and helping it to survive.
Facing the world anew as a craftsman
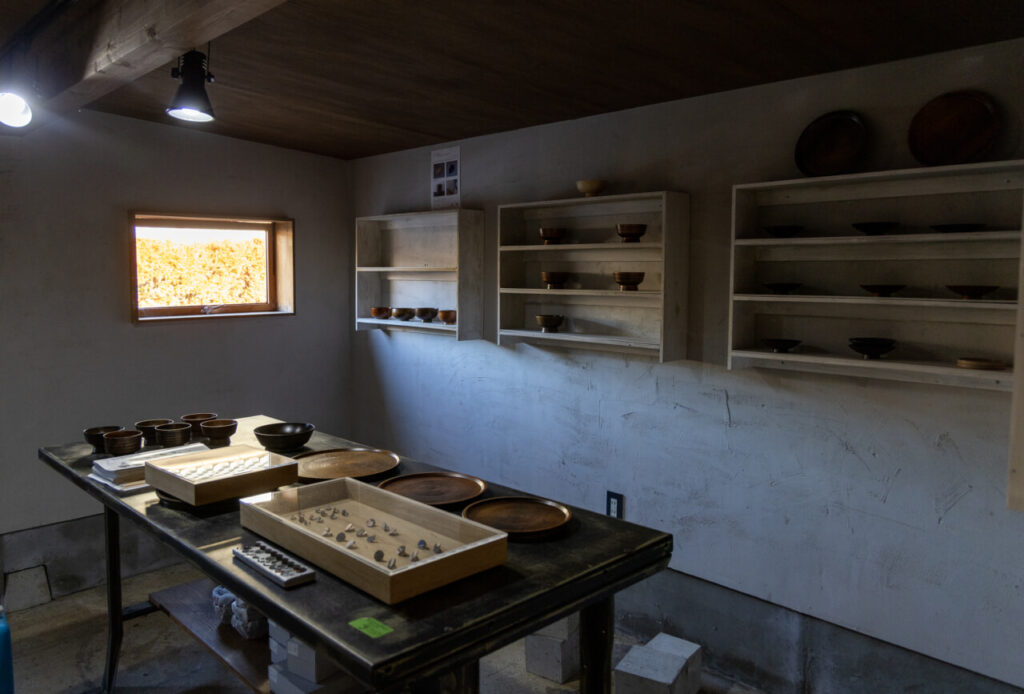
Even now that his manufacturing business is on track, Mr. Sakai feels that “in the end, what I have been doing is not the high road as a craftsman.
What I devote most of my time to now is facing the process of making. He spends more time in the workshop to further develop his skills and knowledge. He is also interested in researching the history of wood-working and the Ainu lacquerware culture of his native Hokkaido.
He says, “I had never studied craft, design, art, or business properly, so I had to research and learn each time. But before I knew it, it had become part of my blood.
His own projects have led to an increase in business, and the production area has become more prosperous. In this way, he has felt the joy of working on projects with the help of “everyone. Now, however, he thinks it is more important to improve his own skills as a craftsman and hone his techniques. I feel that communicating this to the public will add something new to the craftsmanship of the production area.
How will the vessels that Mr. Sakai creates in the future change? The future of the wood craftsman may be one of the patterns that emerge.