During the Edo period (1603-1867), a unique culture blossomed in Nagasaki through Dejima, the only island in Japan open to Europe. Nagasaki tortoiseshell, an ornament made from the shell of the turtles called “taimai,” was also born in Nagasaki, a center of cultural exchange at that time, and its beauty fascinated people. We will visit the workshop of Makoto Fujita, a leading Nagasaki tortoiseshell craftsman, to learn about the history and appeal of tortoiseshell.
What is tortoiseshell?
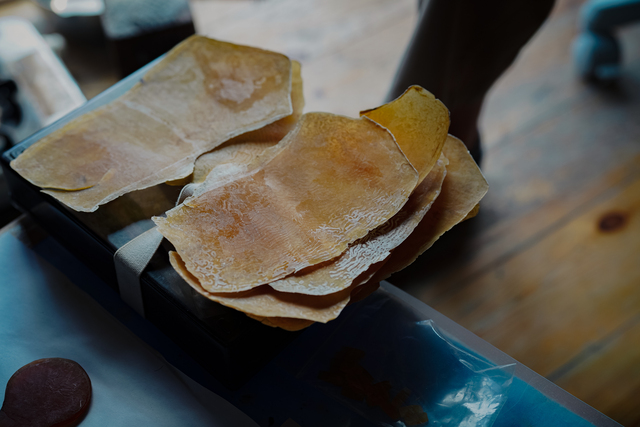
Tortoiseshell is a type of sea turtle called “tortoiseshell turtle. Tortoiseshell work, made from the shell of the tortoiseshell turtle “taimai, ” has long been prized as a luxury item because of its beauty and rarity.
Currently, the import of tortoiseshell work is completely banned under the Convention on International Trade in Endangered Species of Wild Fauna and Flora, also known as the Washington Convention. In other words, only stock imported in the past can be used in the future. The limited availability of raw materials further enhances the value of tortoiseshell work.
History of Tortoiseshell Work
Tortoiseshell work has a long history, said to have begun in the 6th century during the Sui Dynasty in China. Tortoiseshell work was first introduced to Japan during the Nara period (710-794), and the “Shosoin Gomotsu” at Todaiji Temple in Nara Prefecture preserves such treasures as the “tortoiseshell staff” and “tortoiseshell ruyi,” ceremonial Buddhist implements made of tortoiseshell and bearing the name “taimai,” the raw material for tortoiseshell work, and the “raden sandalwood biwa (five stringed biwa)” with tortoiseshell work on the top. and other treasures are preserved.
Tortoiseshell Work in Nagasaki, the Place where Tortoiseshell Work began in Japan
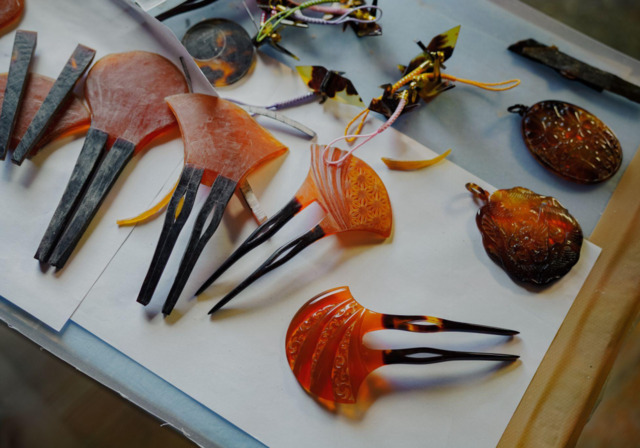
The history of tortoiseshell work in Japan began in Nagasaki during the period of national isolation. The reason for this is that Nagasaki was the only place in Japan that was open to the rest of the world and had a trading post called “Dejima”. At that time, Nagasaki was the gateway to Asian and European cultures, including China and the Netherlands. The “Japanese, Chinese, and Dutch” culture, a mixture of various people, things, and events, was born in Nagasaki, and the city was a bustling center where many merchants, prominent figures, and foreigners gathered. Tortoiseshell, which was brought from the Caribbean and Indian Ocean by Chinese and Dutch ships, was unloaded at the port of Nagasaki and processed by craftsmen living nearby. This was the beginning of Nagasaki tortoiseshell, and in addition to combs, ornamental hairpins, cosmetic boxes, and tobacco cases were also made. Tortoiseshell work with its beauty and elegance was loved by geiko and prostitutes in Nagasaki’s Maruyama, one of the three major flower districts along with Yoshiwara in Edo and Shimabara in Kyoto, and colored the world of glamour.
Technology Spreading from Nagasaki
With the signing of the Port Opening Treaty in the late Edo period, many foreigners began to enter and leave Nagasaki. Since “Nagasaki tortoiseshell” was popular among the foreigners residing in the city, craftsmen studied and refined their techniques and designs to suit the lifestyles of the foreigners. As a result, Nagasaki tortoiseshell became well-known both at home and abroad, and the technique was spread to Edo (Tokyo) and Osaka.
Visit to the workshop of Makoto Fujita, the leader of “Nagasaki tortoiseshell”.
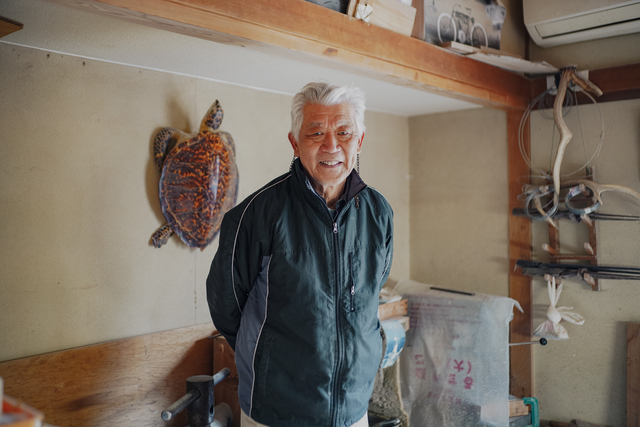
The Fujita family has been carving Nagasaki tortoiseshell for more than 100 years since the Taisho era (1912-1926), and the workshop of Makoto Fujita, the third generation of the Fujita family, is located on a hill in a residential area spreading out like a mortar, typical of the port city of Nagasaki. The house overlooking the town below is located at the top of a flight of stairs that winds up the slope of the house. In the workshop, where a vise, small knives, engraving knives, and polishing machines are crammed into a small space, we were welcomed by a smiling Mr. Fujita.
The Fujita Family’s History of Over 100 Years
The process of purchasing materials from wholesalers, designing, processing, and engraving, and finally completing the product. Mr. Fujita is the only tortoiseshell carver specializing in tortoiseshell work in Japan who carries out all these processes by himself. He does not have his own store, but rather wholesales the pieces he creates in his home workshop to retailers, a style that has continued since his grandfather, Yasutaro, founded the company, which has been branded ” Kizan ” since Makoto’s generation. The name “Kizan” has been used since Makoto’s generation to express his wish that his products would bring joy like that of a mountain. It was a little embarrassing to give it a brand name, but it was requested by our customers…,” says Mr. Fujita, who has been a tortoiseshell craftsman for about 60 years. He has been a tortoiseshell craftsman for about 60 years. He learned the techniques handed down from his grandfather by watching his father Hiyoshi’s back. I later realized that part of my father’s name was included in the character for “Ki,” and now I am glad that I named my brand after him,” he says.
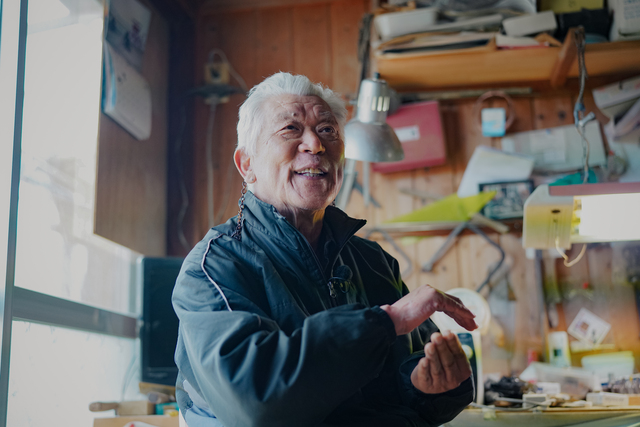
Mr. Fujita and Tortoiseshell Work
Although Mr. Fujita had been in contact with tortoiseshell work since he could remember, he began to study tortoiseshell work in earnest under his father when he was 16 years old. While enjoying his youth at a dance hall, which was popular at the time, he steadily improved his skills as a craftsman. He was motivated by the fact that he could make customers happy and earn money by doing his work. In the 1980s, he got married and started a family, and at the same time the company entered the bubble economy. He was so immersed in his work that he had no time to sleep until he was 45 years old. It was a time when even though I made a lot of things, it was never enough. Looking back, I had the best time of my life.
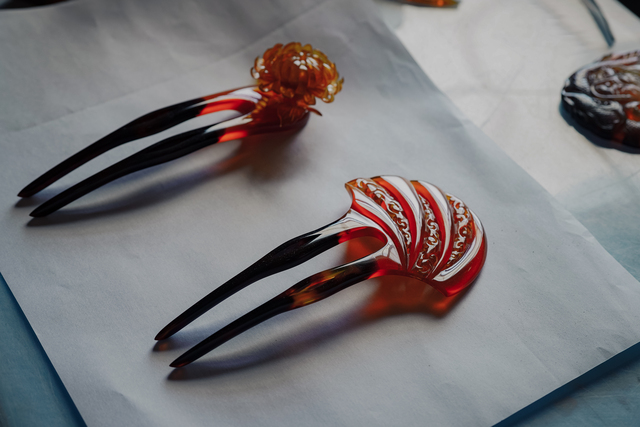
Tortoiseshell was the key to my life. I can only be thankful for that,” says Mr. Fujita, but he has not fostered successors. In addition to the difficulty of securing raw materials, the appearance of inexpensive materials to replace tortoiseshell and declining demand due to changes in lifestyles are the reasons for this. My son wanted to become a tortoiseshell craftsman, but it is a profession that is destined to disappear in time. Unfortunately, he decided not to become a tortoiseshell craftsman. The number of craftsmen, including Mr. Fujita, who take over as successors is decreasing year by year. Not a few craftsmen are refusing to let the current generation take over their craft.
Work Process of Tortoiseshell Work in Nagasaki
Stuffed tortoiseshell turtle, tortoiseshell stock, carving knives, polishing machines, and modified dental tools. Sitting at his desk surrounded by special tools, Mr. Fujita spends about 10 hours a day from morning to evening working on tortoiseshell work.
The process begins with “design. He draws beautiful curves and intricate patterns entirely freehand. Since tortoiseshell is a natural material with no two pieces having the same texture, it is important to choose the right materials to make the best use of the design. He selects the appropriate tortoiseshell material from the back shell, claws, and belly shell, and cuts them with an itonoko to match the shape of the design. This process is called ‘kirimawashi. This process is called ‘kirimawashi,'” he says, “and the saw has been used since my grandfather’s generation. I use it while changing the handle to fit the shape of my hand. The most important thing for a craftsman is to create a tool that suits him,” says Mr. Fujita, holding the handle of the saw to his chest and manipulating the cut at will.
After “kirimawashi,” Fujita shaves off the unnecessary parts using a file and a small knife. This process is called “kisagi” because the word for “scrape” is “kisagu” in the Nagasaki dialect. While scraping with a distinctive sound, Mr. Fujita says, “For some people, it may be an unpleasant sound, but for us, it is the chirping of a cute bird. His smile conveys his love for his work and his charming, mild-mannered personality.
To make a plate-shaped work, several pieces of tortoiseshell are stacked and pressed into one piece to make it uniform in thickness, but to prevent the stacked pieces from shifting, they are first temporarily attached with a hot iron plate. After this process, called “hibashi,” the tortoiseshell is pressed all at once in a vise. The work is then finished into a single plate using only water, heat, and pressure, without the use of any adhesives. This is why tortoiseshell work is called “a work of art made with water and heat. The tortoiseshell work is called an “art form of water and heat,” because the tortoiseshell shell is made by the process of grinding the fibers on the surface of the shell to make them fluff up, and then water, heat, and pressure are applied to the fibers, causing them to intertwine tightly.
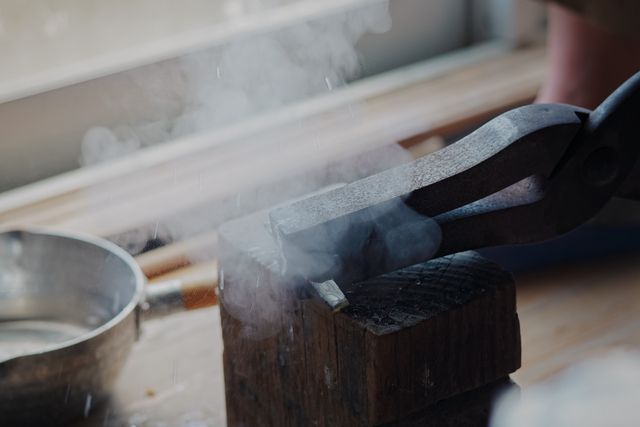
Taimai come from Cuba, Africa, the Philippines, Indonesia, and other places. Like the annual rings on a tree, the shell overlaps like tiles as it grows and becomes thicker. Of all the regions, Caribbean tortoiseshell turtles are the finest, with “excellent color, transparency, and thickness,” says Mr. Fujita. Tortoiseshell is made of the same protein as hair and nails, which deforms when heated. Using this property, tortoiseshell craftsmen have developed a technique to bend and crimp tortoiseshell using only water and heat. For example, to create a warped shape like a hairpin, the tortoiseshell is softened and curved in the process of “oshi-gote,” in which a hot iron is applied to the tortoiseshell.
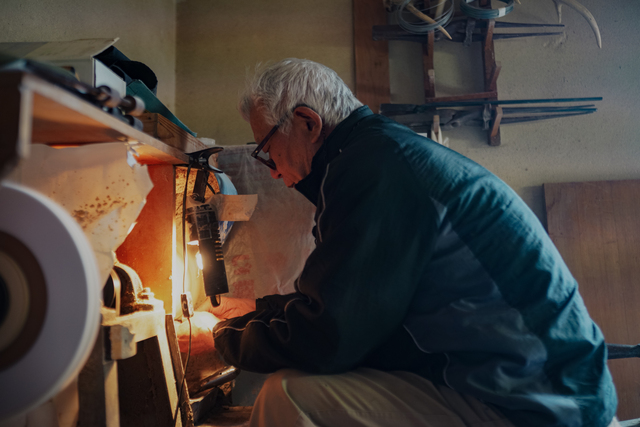
The work is then “sculpted” and “assembled” before being “polished” to complete it. Tortoiseshell pieces polished by a polishing machine give off a unique smooth luster. In the polishing process, diffused reflections on the surface are turned into positive reflections. If you remove the unevenness, not only the tortoiseshell but also your heart will shine,” says Mr. Fujita with a mischievous smile.
Nagasaki Tortoiseshell Work Brand “Kiyama
All of Mr. Fujita’s “Kiyama” Nagasaki tortoiseshell work is one-of-a-kind, produced in his small workshop. The beautiful openwork carvings by Japan’s only professional tortoiseshell carver specializing in tortoiseshell are so beautiful that one can hardly take one’s breath away. Mr. Fujita currently responds to requests from customers all over Japan, and at the same time, he is creating a highly artistic piece every year or two by applying his own techniques. This is because he wants to give form to the various teachings he inherited from his father. Whether it sells or not is of secondary importance. I will continue to make tortoiseshell work to maintain my skills. Tortoiseshell work is not affordable, but there are still people who choose my work and wear it. I am truly grateful.
Seeking a masterpiece that will be created once every few decades
Mr. Fujita faces long hours of work every day, for which concentration and physical strength are essential. When asked what the secret is to his energetic work, he replies, “To play hard. Whenever I have money and time, I take my wife out. The other day I went to Shikoku on a Harley-Davidson motorcycle with a displacement of 1,800 cc. In order to play, I never fail to build up my body. Along with muscular strength comes energy, and I guess that leads to good work,” he says.
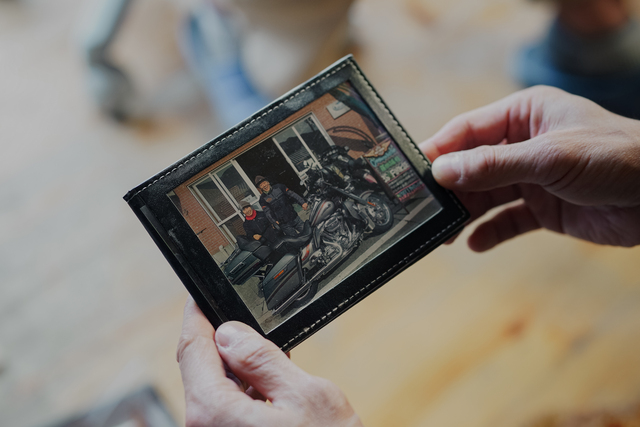
In the 60 years he has worked as a tortoiseshell craftsman, he has only been convinced three times that his work is a masterpiece. I want to experience that moment of joy a few more times. That is why I intend to continue working until I am 90 years old. He will produce a masterpiece once every few decades. With his passion in mind, Mr. Fujita continues to work on Nagasaki tortoiseshell work today.