Mr. Tatsuhito Iwama is a potter of Echizen ware, one of the “Six Old Kilns of Japan”. His representative work, the “Echizen Usukuchi Sake Cup,” is a flat sake cup with a drinking spout only 1 mm thick, a challenge to achieve the extreme thinness that was considered impossible for Echizen ware. The charm of this cup is its unparalleled smoothness when drinking sake. Kuroryu Sake Brewery, a leading sake brewery in Fukui, has also taken notice of the Echizen usukuchi sake cup and asked Mr. Iwama to create an original sake cup for them.
An unprecedented ultra-thin flat sake cup was born in Echizen ware.
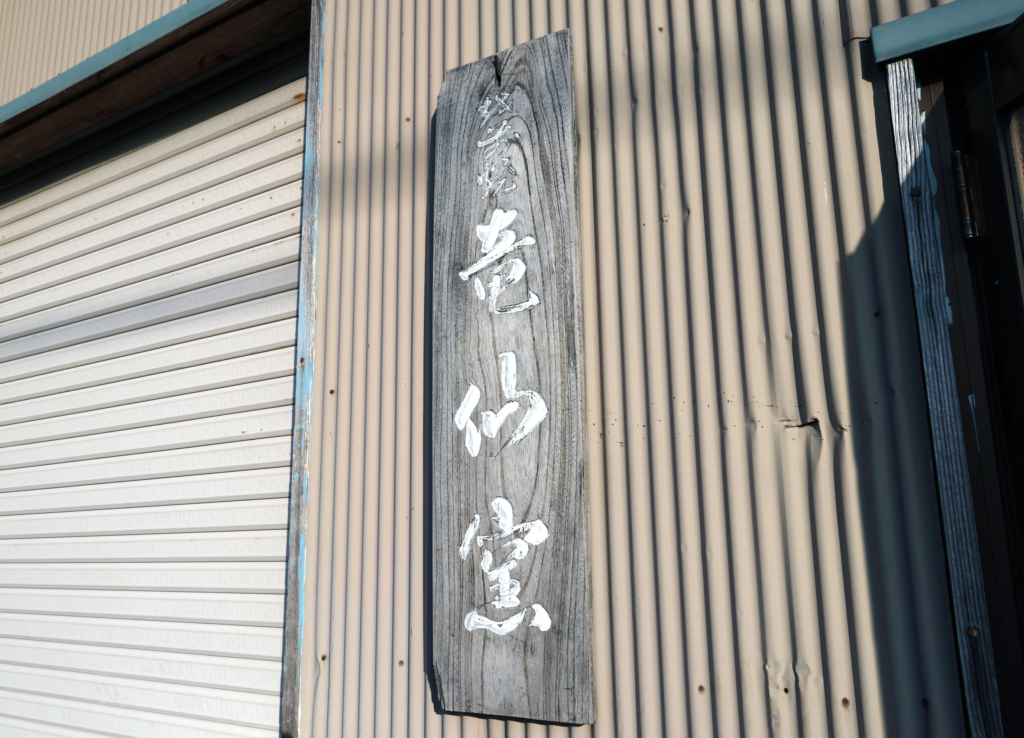
Mr. Iwama has his “Ryusen Kiln” in Echizen-cho, located southwest of Fukui City and facing the Echizen Coast. Nearby is the Echizen Pottery Village, where artists who have entered the village have set up studios, galleries, and other bases for their creative activities. Mr. Iwama is one such artist and was certified as a traditional craftsman in 2019.
Echizen Pottery, which experienced a revival after a period of prosperity and decline
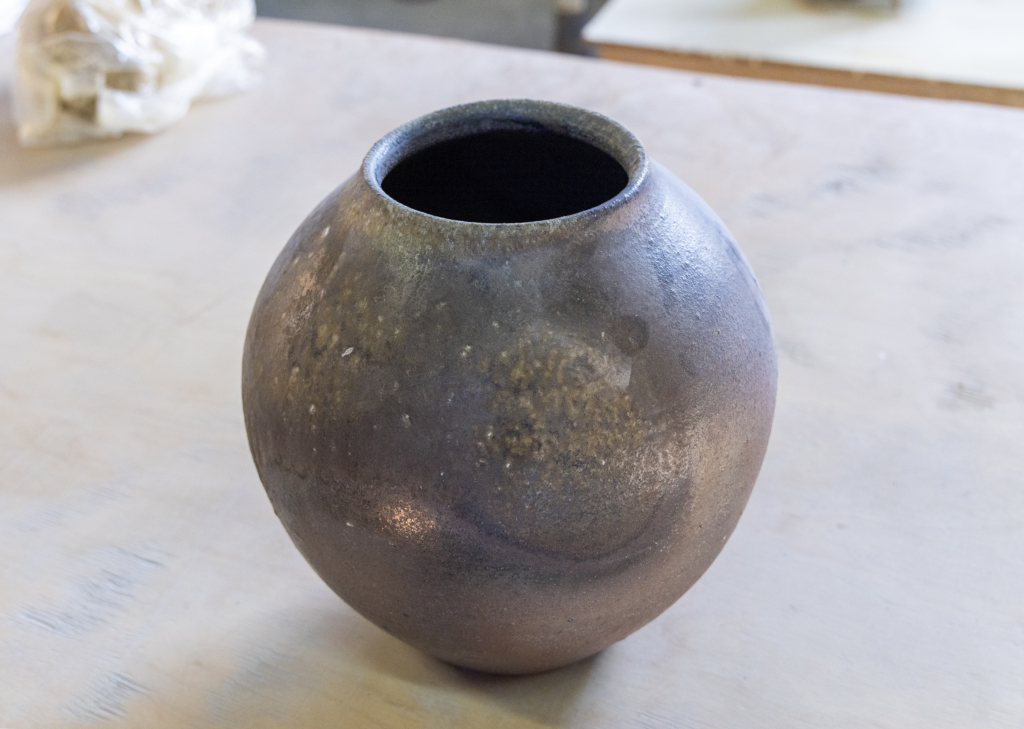
Echizen Pottery began at the end of the Heian Period (794-1185) and initially produced mainly miscellaneous daily-use ware such as water jars and mortars. By the late Muromachi Period (1333-1573), Echizen Pottery had become the largest pottery production area on the Sea of Japan side, and was distributed over a wide area from Hokkaido to Shimane Prefecture. However, it gradually declined in the mid-Edo Period due to the rise of other pottery production areas, and from the late Meiji to Taisho Periods, a number of pottery makers closed their businesses. In 1986, Echizen pottery was designated as a traditional craft by the national government, and in 2017, it was recognized as one of the “Six Old Kilns of Japan” by the Japanese government. Echizen Pottery has been revived and is now recognized as one of Japan’s Six Old Kilns.
Echizen Pottery is one of the simplest among the many types of pottery, and its simple, warm appearance that brings out the texture of the clay is appealing. In the past, Echizen pottery was characterized by the absence of glaze, but in recent years the use of glaze has been on the rise, and modern vessels in vivid hues, fired with layers of pigment-colored decorative clay, have also appeared.
Flat sake cup with a drinking spout only 1 mm thick
Pottery is broadly classified into ceramic and porcelain, and Echizen Pottery, which Mr. Iwama produces, is classified as ceramic.
While pottery is made mainly from clay, porcelain is made mainly from stone powder made from ground pottery stones and fired at 1,300 to 1,400 degrees Celsius. Firing at high temperatures melts the raw material into glass, making porcelain harder and thinner than ceramics.
Conversely, it has been difficult to reproduce the thinness of porcelain in ceramics. Mr. Iwama took up the challenge of producing Echizen ware that is thinner than porcelain and completed a piece called “Echizen Usukuchi Sake Cup. Needless to say, the greatest feature of the cup is the thinness of the mouth. The contour of the cup is only about one millimeter, and when you hold it to your mouth, you can only feel the texture of the cup, allowing the sake poured into the cup to flow naturally into your mouth. The sharpness of porcelain and the naturalness of Echizen ware combine to create a sake cup with an unprecedented tactile experience.
The challenge of creating ultra-thin Echizen ware, which seemed impossible, was also a struggle for Mr. Iwama to survive as an artist.
Fascinated by Echizen Pottery, Becomes an Artist
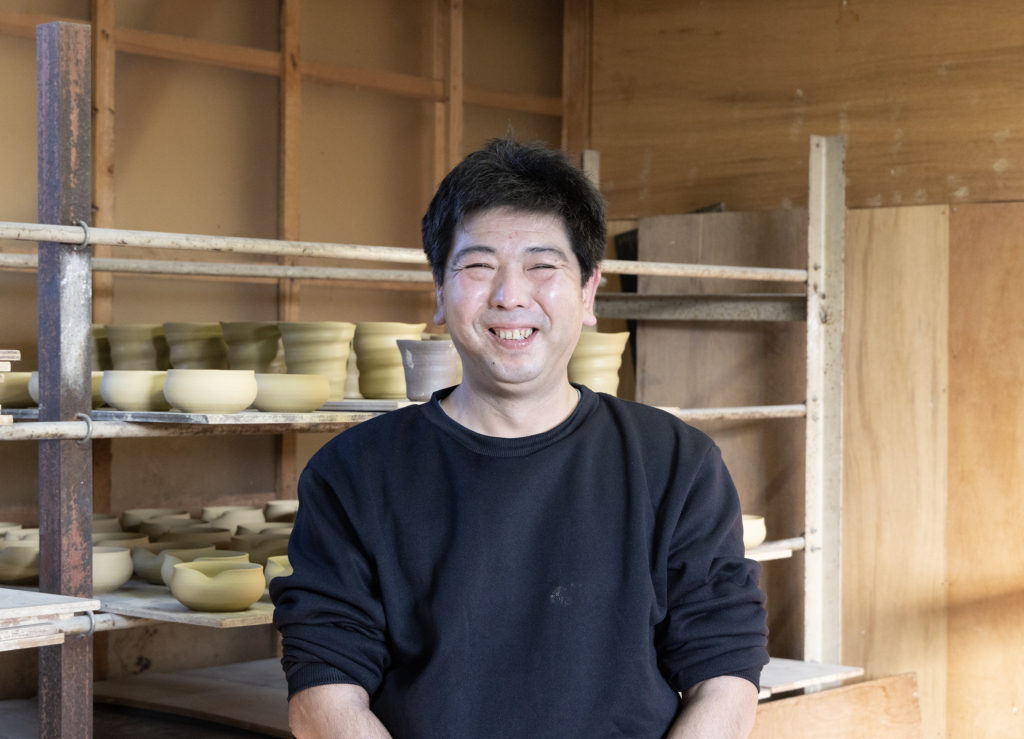
Mr. Iwama became fascinated with the world of pottery when he joined a local pottery club during his junior high school years, and in 1991, he joined a kiln in Echizen City and began working there as a live-in worker. From that year to 1994, he was selected for the Fukui Prefecture Art Exhibition for four consecutive years, gaining experience as a promising young artist. Gradually, his ability as an artist was recognized, and Iwama’s works began to appear in catalogs issued by the Echizen Pottery Cooperative Association to wholesalers and other dealers. In 2007, after receiving a certain number of orders for his work, he decided to open his own studio, partly on the recommendation of the cooperative. He borrowed the necessary funds from a financial institution to invest in an expensive gas kiln and other equipment.
Became independent as a writer. Continuous trial and error
When he first became independent, he received congratulatory new orders, but within two years, the orders stopped coming in. Orders from the cooperative, his main client, were also sluggish, and he was told that customers would get tired of his traditional Echizen pottery style alone. So, he repeated trial and error, including the production of brightly colored vessels made of decorative clay. People around him said, “His style changes from time to time,” but this was a result of his emphasis on the Echizen ware that customers wanted, rather than his persistence as an artist. Mr. Iwama was unsure of his path as an artist when his union approached him for advice, and this marked a turning point in his career.
Finally, an ultra-thin flat sake cup is completed.
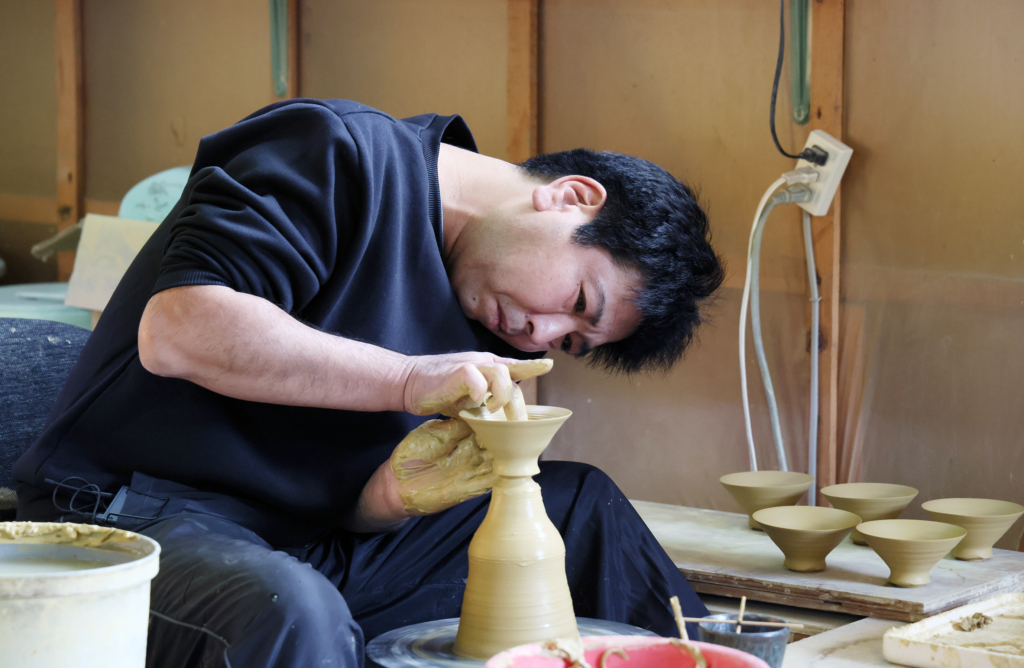
A customer wants a thin flat sake cup with a thin mouth. Can you make a very thin one? When Mr. Iwama heard the request from the union, he knew it would be difficult, but he was determined to do it. However, the struggle was more than he expected.
The clay is then placed on a potter’s wheel and stretched upwards and downwards in a process known as “dochi-kiri,” or “clay killing,” to further prepare the clay and create the central axis. The clay is then placed on the potter’s wheel and stretched upwards and downwards in a process called “dochi-koshi,” in which it is stretched upwards and shrunk downwards to form the central axis. After adjusting the clay to make it harder, we thought we had finally succeeded in molding the clay, but when we fired it, it cracked. Next, he tried to make the clay dry longer after molding.
Finally, he completed an ultra-thin flat sake cup, but there were days when he was only able to mold a few pieces after a full day’s work. Mr. Iwama thought daily about how he could increase his production in order to earn his living as an artist.
Repetition is the shortcut to improvement.
Since he could not afford to hire an employee, Mr. Iwama thought the only way was to increase his own productivity, so he increased orders for flat sake cups. He decided to increase the accuracy and speed of the molding process by repeating the thin-stretching process. After consulting with the cooperative, he set the selling price of the flat sake cups at an unbelievable 1,000 yen or less, and orders poured in. As he continued to work hard on the molding process, he went from being able to make a few pieces a day to four or five pieces an hour, and is now able to mold about 10 pieces an hour. After molding, he dries the pieces, shaves the base, dries them moderately more, unglazes them at about 800 degrees Celsius, glazes them, and finishes by firing them at about 1200 degrees Celsius. It takes at least two weeks from the time of molding to the time of firing.
Ultra-thin flat sake cup of recognized value
Today, Mr. Iwama’s Echizen usukuchi sake cups are sold through a cooperative, and their prices are nearly five times higher than when he first started out on his own. In 2016, about three years after Iwama began making ultra-thin flat sake cups, the Kuroryu Sake Brewery, which had paid attention to Iwama’s work, commissioned him to make an original flat sake cup, which was released as the “Kuroryu Flat Cup. With the same ultra-thin finish as the Echizen usukuchi sake cup, it is gaining popularity as a sake cup that enhances the flavor of Kuroryu’s cold sake.
Continuous pursuit of perfection in the work
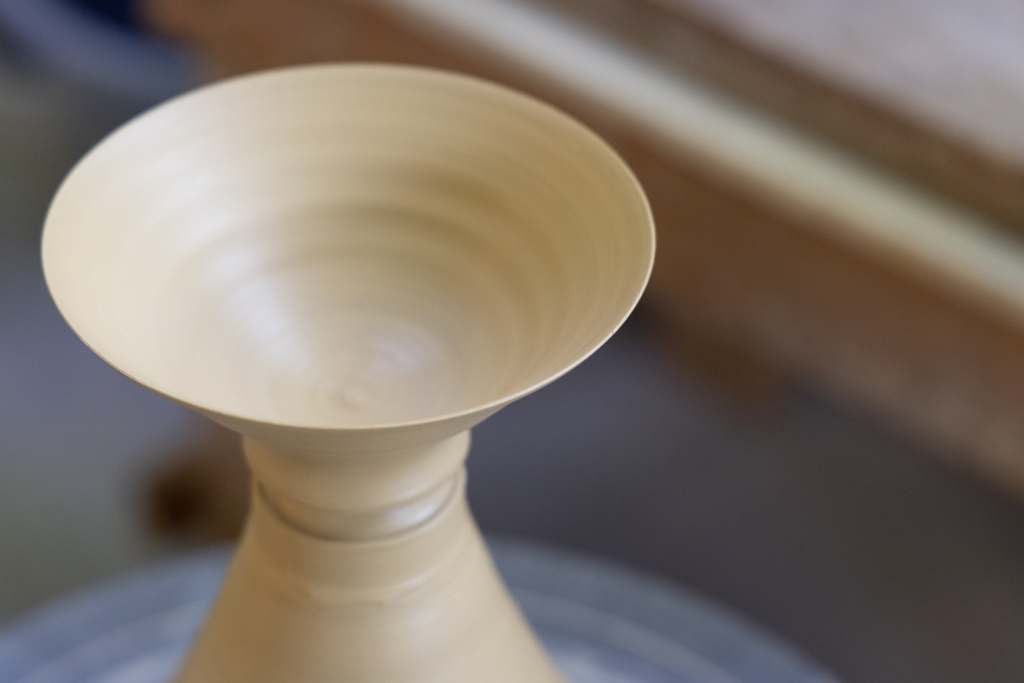
While holding his own work, which looks perfect to others, Iwama says, “I would like to make the mouth of the cup 0.1 mm thinner to further improve the perfection of the piece. The starting point for his pursuit of excellence as a ceramic artist is the experience of being fascinated by pottery at a pottery club he once attended. Now, Mr. Iwama teaches pottery-making classes for parents and children organized by Echizen Town and the local cooperative. Through these efforts, children will be introduced to pottery, and this will lead to a prosperous future for the production area.