Bringing out the natural colors
We visited dyer Kofu Suwa, who uses natural dyes made from plants and flowers to dye threads and weaves them into textiles. Born to a family of dyers in Yonezawa, Suwa helped the family business and learned the skills naturally.
Seeking a unique methodology, he studied and publicized shellfish dye using domestic shellfish. He also studied saffron dyeing, gromwell root dyeing and other rare dyeing methods. He is an artist who developed many “colors”. Currently he is the representative of the Yamagata Safflower Dyeing Weaver’s Council and promotes the branding of “Yamagata Safflower Dye”. When he showed us Yamagata Safflower textiles, he explained the meaning of the mark on the label. The red marks mean 100% dyed with safflower, the pink marks mean dyed with safflower and other natural dyes, yellow ones are dyed with safflower and artificial dyes. All 3 types use domestic silk and clear exacting standards to maintain quality.
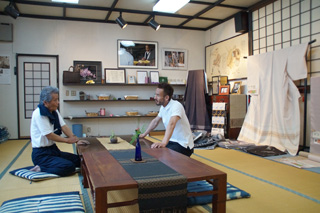
Weaving various textiles
The Oitama region where the workshop is located, is famous for its textile industry and has a tradition of thread spinning and highly sophisticated “kasuri” pattern textile skills. Suwa’s son, Goichi, who is also a dye-weaver, showed us around the workshop. A large thread spinning machine caught our eyes.
“The textile production skills for hemp threads from Joetsu (southern Niigata) was the start of textiles of this region. This equipment has been used since the olden times. There are only a few workshops left that still use this kind of equipment. “ he explained.
In the workshop, there were several types of looms, ranging from the large “takabata” loom to smaller ones, and some that are partially mechanized. It showed that the workshop deals with a multitude of weaving techniques.
Also, rather surprisingly, baskets and bags using wild vine and tree barks were under production. The looms were operated by female craftsmen, and baskets were woven by men. The sound of the looms echoed incessantly in the workshop.
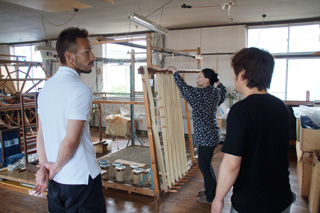
The difficult process of “building” indigo
Suwa has been dyeing with indigo since about 30 years ago. For indigo dyeing, you must first “build” indigo. ”Build” means to bring indigo ingredients ”sukumo” and lye together in a pot, ferment it, and have the textile absorb it.
“How long does it take to “build” indigo?” asked Nakata.
“It depends on the temperature, but we spend about 7 days on average. Those 7 days are very intensive“, described Suwa.
“It’s really difficult. We have no idea what can happen. You can do this for 20 years, 30 years and only then do you develop the intuitions that you need to get it right. “
He said with deep emotion.
That day, the indigo was not doing well. The cotton cloth that was sunk into the pot for testing was a deep green when it was pulled out. “It is green in the beginning. It turns blue after it touches the air, but it has to be a more beautiful blue.“ Goichi-san said, wondering what was wrong.
Indigo can only dye while the fermentation process is going on, so sometimes “sake” is added to promote fermentation. Yes indigo is “alive”. The condition of the indigo needs to be watched every day.
We got to see a rare dyed textile. “Sakurazome”, or cherry blossom dyed textile. Dye for “sakurazome” is made by boiling the tips of the branches before they blossom.
“An amateur would think that color would come from the flower petals.” Nakata said.
“Yes maybe, but the cherry tree in early spring has its vitality all tanked up before the blossoms bloom. But when it blooms, all the vitality is used up and we can’t get any color from the actual blossoms.” The “sakurazome” textile was a very subtle color that was indescribable in words.
The skills that were brought up in a land with a long and flourishing textile industry, and the skills of natural dyeing that Suwa pursued. The combination of the two created textiles that reflect the features of Yamagata.
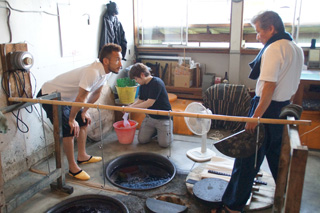
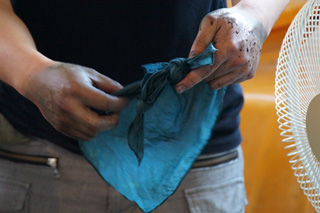