Hiroe Kitagawa is one of the few makers of handspun cotton products who performs all processes by herself, from yarn spinning and dyeing to kasuri weaving, patterned weaving, and weaving on a loom. The elaborately patterned obis and kimonos that Mr. Kitagawa creates are in keeping with Japanese tradition, but they are also imbued with ideas that go beyond the traditional.
Hand-spun cotton yarns are spun and woven by hand
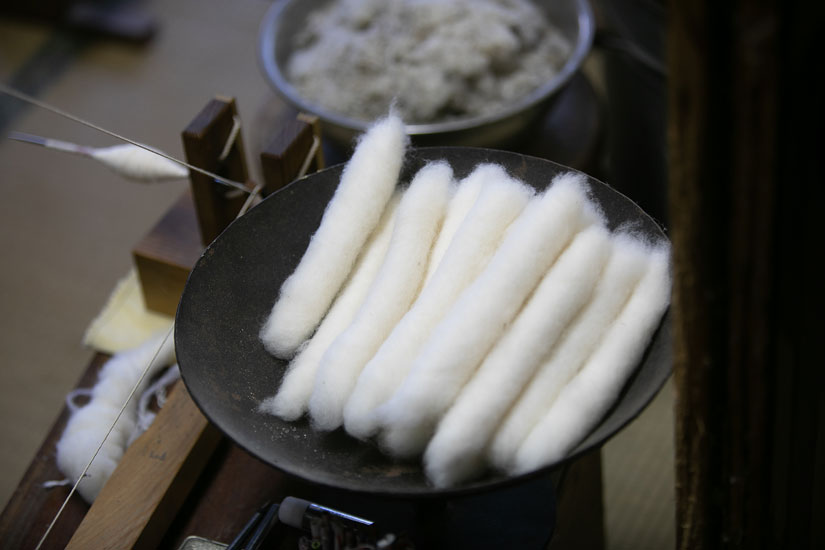
Handspun cotton is a fabric made by spinning yarn from cotton using a spinning wheel, dyeing the yarn with plants and other materials, and weaving the fabric on a handloom. Hiroe Kitagawa, who produces handspun cotton textiles at her home and studio in Kurashiki City, Okayama Prefecture, has been weaving women’s obis and kimonos with handspun cotton textiles for several decades. Her textiles have many fans, and when she distributes them to wholesalers, they are sold out in no time. Her creations are so attractive that they are in high demand.
Encounter with Izumo Ori
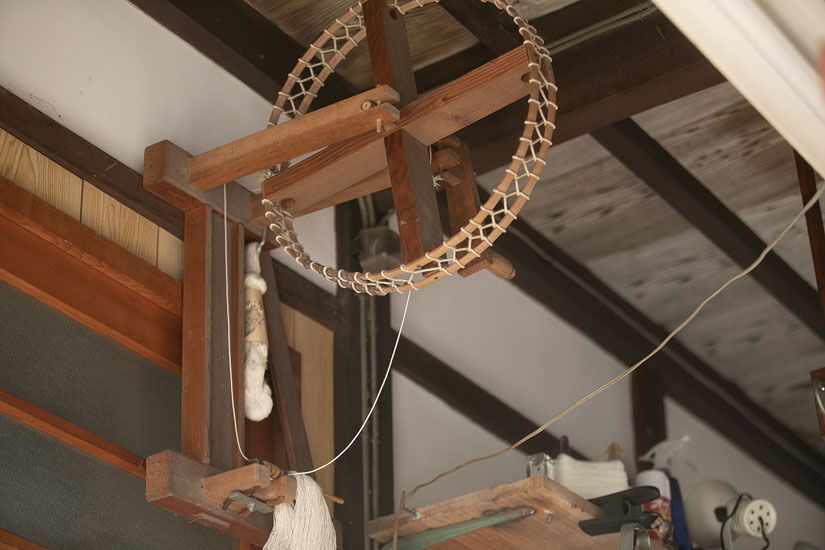
Long before he started his handspun cotton business, Mr. Kitagawa had a passion for “making things. He was familiar with Japanese-style paintings, watercolors, and copperplate engravings as hobbies, and one day, at the suggestion of an acquaintance, he exhibited his own work in an exhibition. However, as soon as her work was exposed to the eyes of others, she felt embarrassed, as if she were hanging naked on the wall.
He recalls, “I was looking for something to express myself, but as soon as I felt ‘me’ showing, I hated it.
One day, she stopped by a bookstore and casually picked up a trade magazine on dyeing and weaving, and learned that Yumie Aoto, an Izumo weaver, was looking for trainees at her studio. Although she did not know much about Izumo weaving, she was inspired and immediately contacted Yumie, who accepted her offer at the age of 42.
Creation in which the ego does not appear
Izumo weaving is based on cotton kasuri, which was used as stray clothes. In Yasugi City, Shimane Prefecture, where Mr. Aoto’s workshop is located, farm women have spun yarn from cotton and dyed it with natural indigo to weave it while working on the farm since the Edo period. It was Ms. Aoto who brought modern patterns to this traditional kasuri and established it as “Izumo weaving. Mr. Kitagawa started from yarn spinning under Mr. Aoto and learned traditional pattern weaving for two years.
While seeking “something expressive,” Kitagawa disliked the idea that her ego would come out in what she created, but she was never bothered by this feeling while weaving. When I look at the finished product, I think it is something that is uniquely me, but it doesn’t show my ‘self’ in a concrete way,” she said. This is probably because I create within the rules of weaving. I think it suits my nature.
Referring to American textiles of the 17th and 18th centuries
After learning Izumo weaving and returning to Kurashiki, he began to receive requests from wholesalers to produce obis through Mr. Aoto’s introduction. At first, he wove traditional patterns, but sometimes he felt they were not enough. At that time, he found a book that compiled textile designs that were popular in the United States during the pioneer period of the 17th and 18th centuries. The book introduced textiles used as bedspreads, wall hangings to keep out the cold, and rugs for the floor, and I was attracted by the simple and free use of patterns and colors. As I read the patterns alone and wove what inspired me, I found it interesting and irresistible. This feeling continues to this day, and in Kitagawa’s creations, patterns from faraway lands are fused with Japanese traditions.
Spinning yarn according to what you want to weave
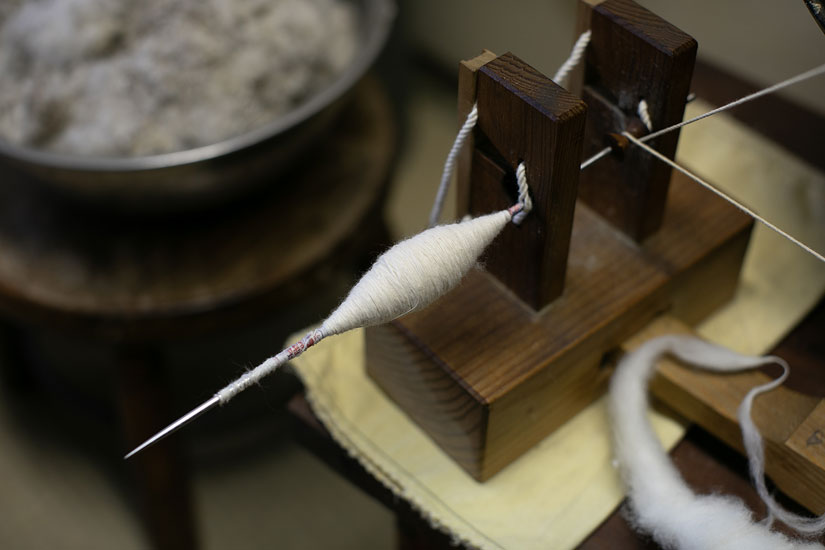
Creation begins with the spinning of yarn from cotton. A large number of yarns are spun and dyed as weft yarns, which are selected for use at the weaving stage. Cotton is used in different forms, including Japanese jiwata, Indian cotton, American cotton, Mexican cotton, and other types of cotton. The properties of cotton vary greatly depending on the region where it is produced, with Egyptian cotton being the most suitable for kimono because of its fine fibers and ability to spin long yarns. The cotton is spun and woven while getting accustomed to the characteristics of each.
Become one with the spinning wheel
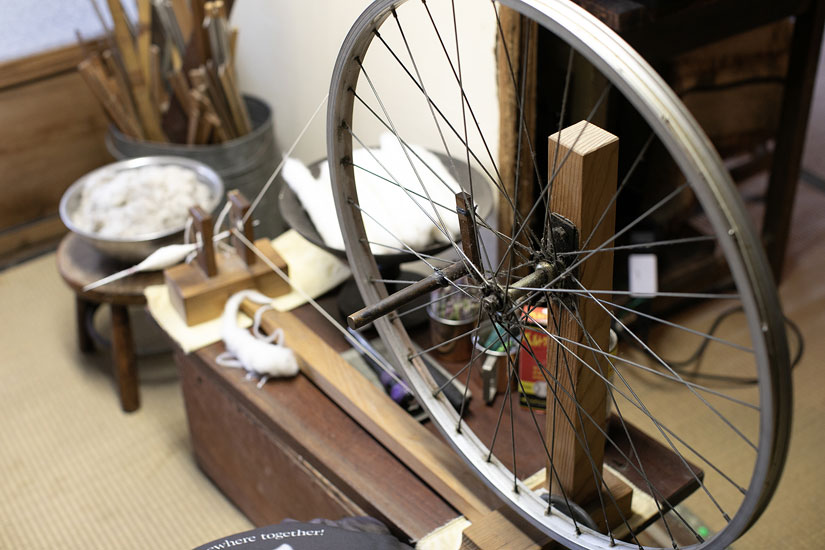
Mr. Kitagawa says that the used yarn wheel he uses now is his “alter ego. In fact, he has a trusted mechanic for his looms close at hand. He is Mr. Masakazu Higuchi of “Chikusendo,” a company that makes handlooms and their accessory parts in Kurashiki City. Mr. Higuchi is familiar with the structure of these machines and quickly discerns the relationship between the weaver and the machine. Kitagawa was troubled by this and consulted Mr. Higuchi. He asked Mr. Higuchi for advice and was told to “bring a bicycle wheel,” and Mr. Higuchi attached a bicycle wheel to the difficult-to-use spinning wheel, adjusting it beautifully.
When I use this wheel, the fibers from the cotton are spinning easily, as if they are saying, ‘I want to intertwine with other fibers, I want to intertwine with other fibers,’” he said. I got so absorbed in spinning that I spun for days and nights until midnight, and I even calculated how much I had already spun to reach the moon,” Kitagawa says, laughing.
In Kurashiki, where Kitagawa and Higuchi grew up, there is the Kurashiki Honzome Hand Weaving Institute, which was established as a craft center attached to the Kurashiki Mingeikan. Higuchi-san was exposed to the world of hand weaving as a child. When Mr. Kitagawa was in high school, he heard a lecture by Kichinosuke Tonomura, the first director of the Kurashiki Mingeikan, and pondered the relationship between “things” and “decoration. The two share the same attitude of being willing to go to great lengths.
For example, an old machine that has become familiar to the weaver often produces better cloth than a new machine. In short, they say, “We just have to adapt to what is in front of us. Both weavers have mastered the art of not pursuing efficiency, but rather learning the materials and machines they use, and becoming familiar with them as they go along.
90% of the production is done until we get to the plane
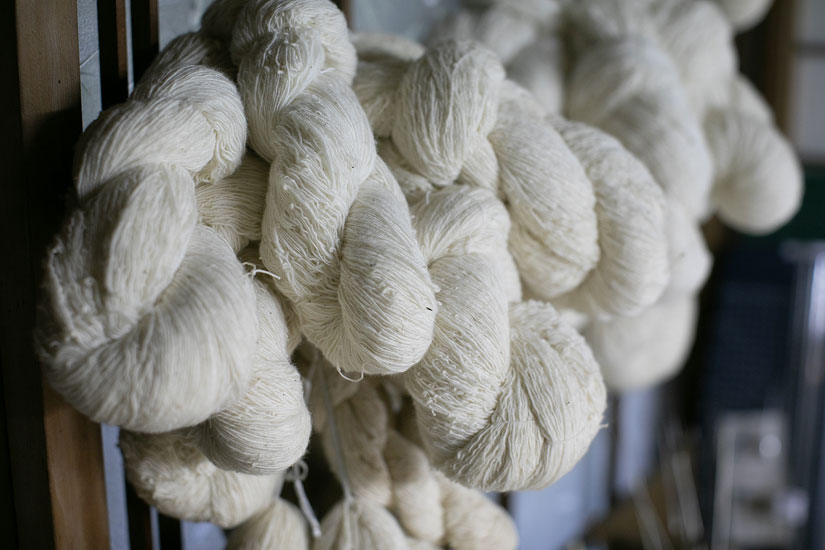
When the yarn has been dyed to the desired color, it is finally ready for the machine. This is the most enjoyable time, says Mr. Kitagawa. Ninety percent of the production process takes place up to this point. Moreover, hand weaving progresses only 1 to 2 cm (3 to 5 cm) per hour. Even so, once you start weaving, the woven fabric spreads out in front of your eyes. That joy is irreplaceable.
I see myself in what I make
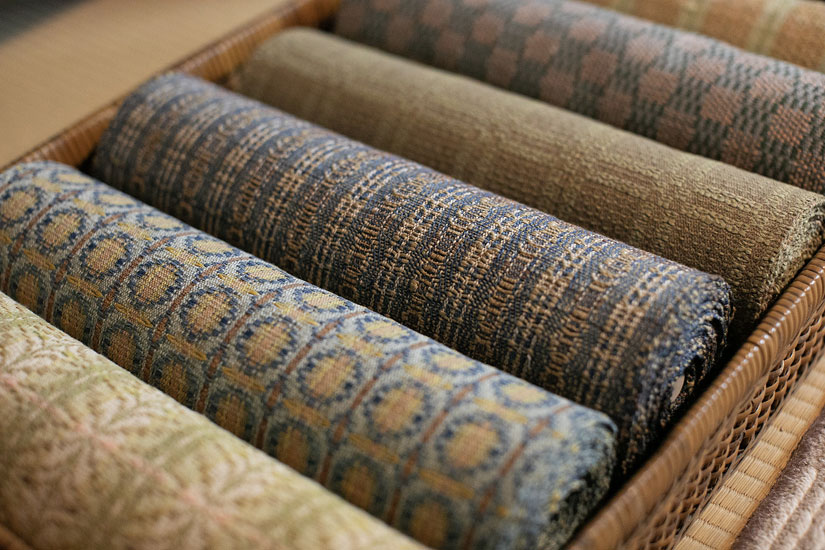
The obis and women’s fabrics that Ms. Kitagawa creates are in demand by people of all ages. What she keeps in mind when creating is “to live one’s life with purity and sincerity. This is not only in the area of work, but also in his daily life. The things I make reflect the creator,” he says. And since the things I make are for people to wear, I want to give them to them in a pure way. I believe that good things cannot be created unless the maker lives a proper life.
If you weave according to the spun yarn, you can weave well. If you take the time and effort to weave, you will get a good taste. The more you wear the finished garment, the more it will fit your body. Although the use of power-driven spinning has made it possible to mass-produce fabrics in a short period of time, there are still many people who seek out Kitagawa’s work, which has been described as unique in its natural texture and design, because he hand-dyes, spins, and weaves all the fabrics himself. In order to meet such needs, and more importantly, because Kitagawa himself knows that only hand weaving can produce such quality, he will continue to express “Hiroe Kitagawa’s sensibility” in his hand-woven cotton fabrics.